MK Products MiniMicro Orbital Weldhead User Manual
Page 10
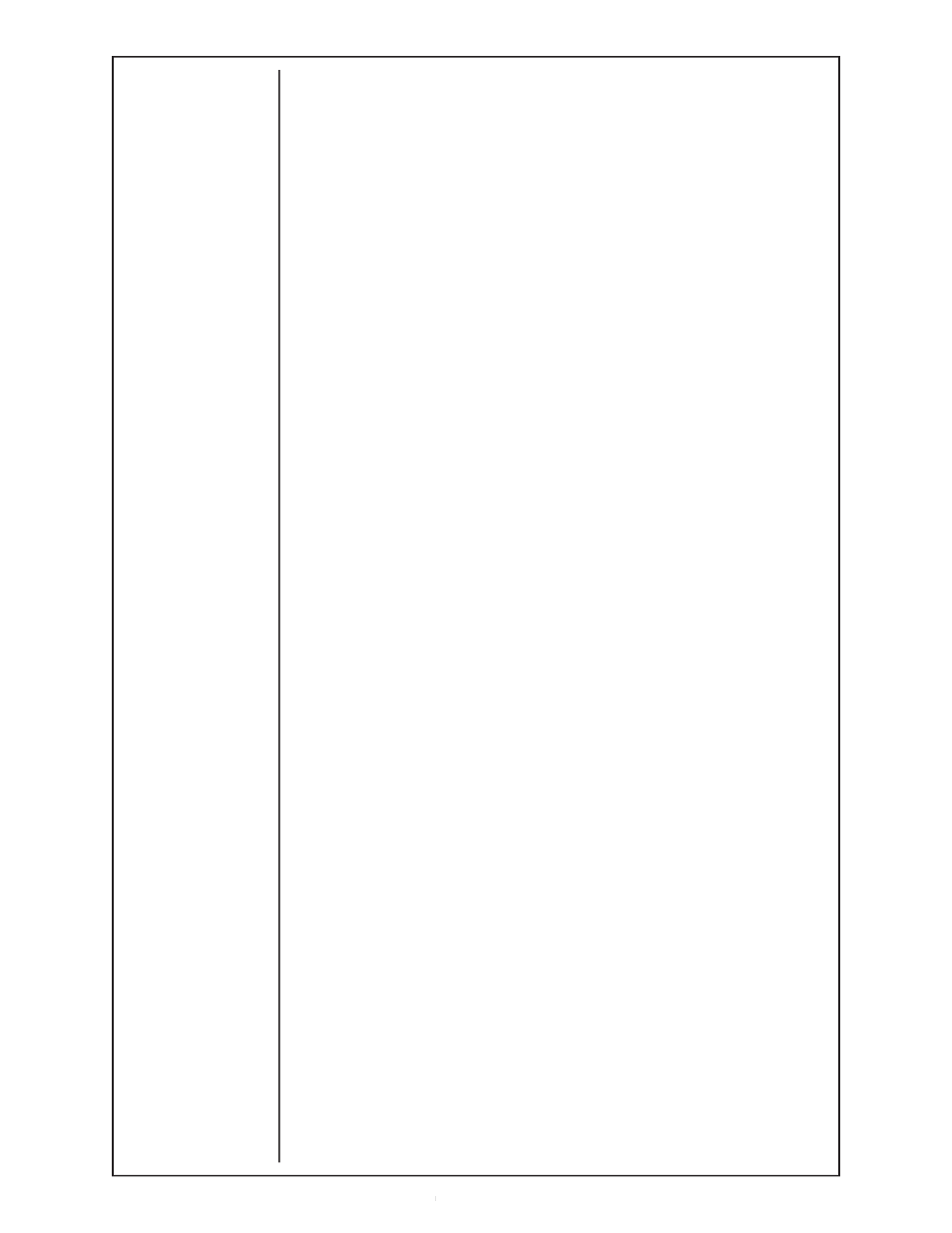
Mini Micro
®
Owner’s Manual - Page 4
®
®
Welding Leads
The two welding Power Leads use a twist-lock type of power connector.
These are designed to attach directly to the rear panel of the CobraTig
®
150.
®
®
The male connector connects to the receptacle labeled “ELECTRODE”. The
female connector connects to the receptacle labeled “GROUND”.
Control Cable
The 24 MS-type pin connector attaches to the mating receptacle on the rear
panel of the orbital welding power-supply. All of the Control, Feedback and
Welding functions of the weldhead transfer through this connector.
The operator controls are on the weldhead handle. They include: JOG, GAS/
NEXT LEVEL, FINAL SLOPE and START/STOP.
Gas Hose
The gas connector is a double-end shut-off type valve that prevents fl ow or
leakage out of either the unit or the gas hose if the connection is broken.
The gas hose connector from the weldhead plugs into the “GAS OUT”
receptacle.
Water Hoses
The water connectors are a quick-release type that prevent fl ow or leakage
out of either the CobraCooler™ or the water hose if the connection is broken.
The water hose connectors from the weldhead plug into the “WATER IN” &
“WATER OUT” receptacles on the rear panel of the CobraCooler™.
Collets
The three-piece collet assembly mounts to both the jaws and the bottom
face plate of the weldhead and maintain the weld joint alignment of the parts
to be welded. The collets are manufactured to correspond with the outside
diameter of the material to be welded. Each set of collets has three pieces;
two sides and one bottom. Two sets of collets are needed to weld two tubes
together.
Collet Adjustment (Extended Collets Only)
The parts to be welded are held in place by the Collets. The tolerance of the
outside diameter of tubes and pipes vary, so these variations are handled
through the use of brass-tipped setscrews, referred to as plungers, in the
top Collet halves. These plungers not only make up the diameter difference
between the Collet and the part to be welded, but they also act as an aid in
the grounding path between the weldhead and the tube or pipe to be welded.
The tube or pipe is forced down into the bottom halves of the Collets, which
are screwed to a line-bored concentric face in the weldhead side-plates.
The plungers are adjusted as follows:
1. Back the plungers out until the brass tip is fl ush or below the surface of
the bored Collet surface.
2. Place the parts to be welded into the Collets and clamp down the latches.
Adjust the latching mechanism of the weldhead to ensure a tight, but not
overly-tight clamping of the Side Plate Jaws.
3. Alternately adjust the plungers on one side of the weldhead until contact
is made, and then add about 1/4 turn more.
4. At this point the tube should be fi rmly held in place. The tube should not
turn if attempting to rotate it by hand.
Section
A Cont.