Reference: grounding and strain relief, Grounding of m1500h, Strain relief of cable – MicroE 1500H Mercury User Manual
Page 15
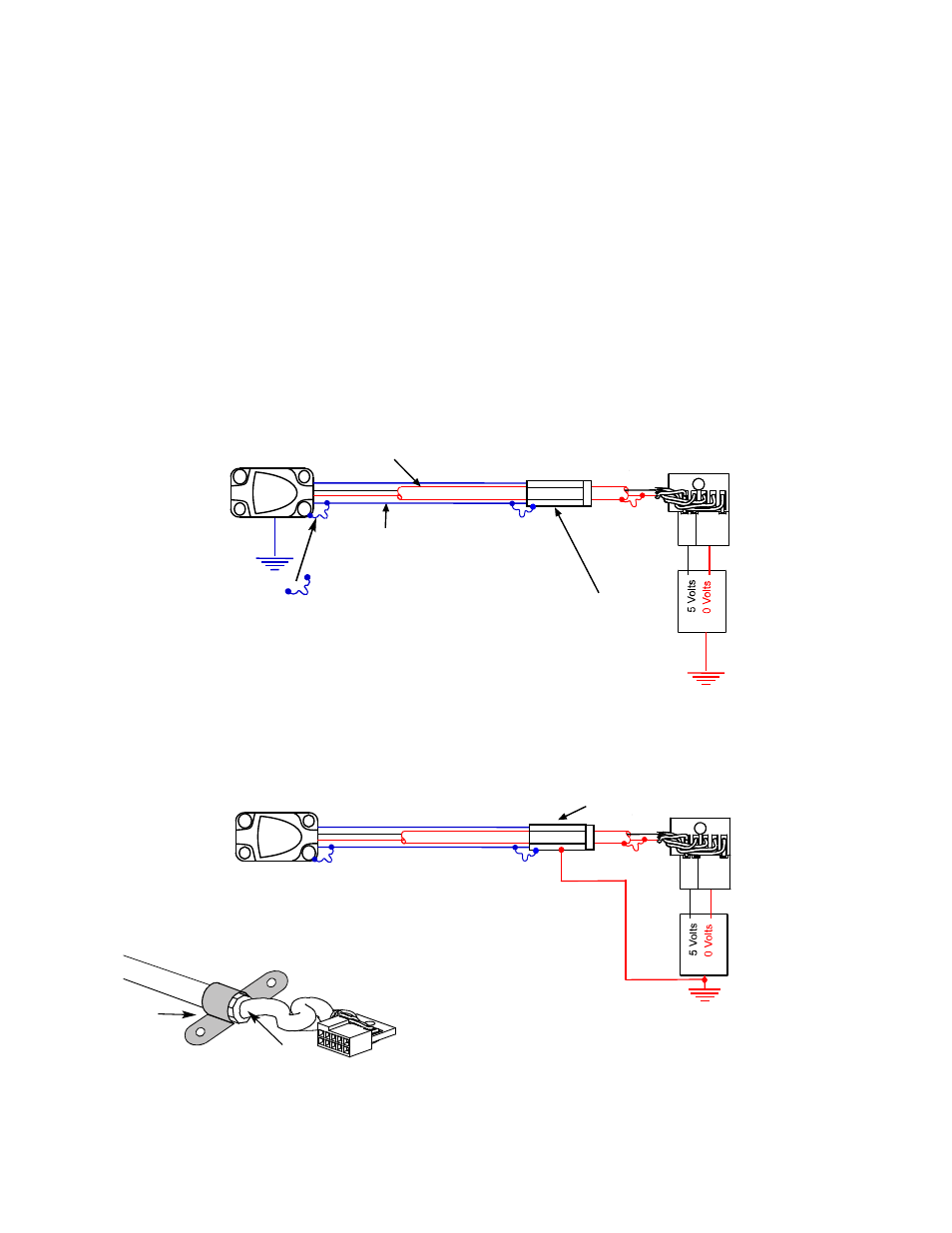
Page 13
Grounding of M1500H
Inner shield: Insulated from outer shield and
sensor case. Connected to circuit common
internally (pin 4).
Outer Shield: Connected to sensor
and hex sleeve.
Hex sleeve
do not ground
Power
Supply
Sensor mounted with good electrical contact to a well-grounded surface (preferred)
1. 5x2 micro-connector grounding: The portion of the encoder from the 5x2 micro-connector to the hex sleeve must be enclosed in a customer-supplied shielded
enclosure or shielded connector. The hex sleeve must be in intimate, electrically conductive contact with the enclosure or connector, which must be isolated from
the controller's ground. If a customer-supplied shielded cable connects the encoder to the controller, then the outer shield on the customer-supplied cable must
be isolated from the controller's ground.
2. The sensor mounting surface must have a low impedance (DC/AC) connection to ground. The encoder sensor mounting surface may have to be masked during
painting or anodizing to insure good electrical contact with the sensor.
For Mercury 1500H encoder systems to operate reliably, it is essential that the sensor and cable shield are grounded properly according to the following
instructions. The diagrams below show how to make the connections when the encoder's connector is plugged into the customer's controller chassis. If
a customer-supplied extension cable is used, it should be a double shielded cable with conductive connector shells and must provide complete shielding
over the conductors contained within it over its entire length. Furthermore, the shields should be grounded at the connection to the
controller chassis the same way as the encoder connectors in the diagrams below.
Note: For best performance, isolate the encoder outer shield from motor cable shields and separate the encoder cable as far possible from motor cables.
Sensor mounted to a surface that is grounded through bearings or a poorly-
grounded surface, or mounted to a non-conducting surface
1. 5x2 micro-connector grounding: The portion of the encoder from the 5x2 micro-connector to the hex sleeve must be located within a customer-supplied
shielded enclosure or shielded connector. The hex sleeve must be in intimate, electrically conductive contact with the customer-supplied enclosure or con-
nector, which must be connected to the controller's ground. If a customer-supplied shielded cable connects the encoder to the controller, then the outer
shield on the customer-supplied cable must be connected to the controller's ground. The controller must be grounded to earth at the point of installation.
2. The encoder sensor must be mounted so that it is electrically isolated from ground.
Mercury encoders require a minimum of 4.75V DC continuously. When designing circuits and extension cables to use Mercury encoders, be sure to account for volt-
age loss over distance and tolerances from the nominal supply voltage so that at least 4.75V DC is available to the Mercury encoder under all operating conditions.
Do not exceed 5.25V DC.
Grounding Instructions for Mercury 1500H Encoder System
Recommendations for Power
Hex Sleeve
Power
Supply
Strain relief of cable
The cable should be strain relieved in the manner shown to the left. Note: If ground
connection is made at the aluminum hex nut sleeve, then the cable strain relief strap
must be conductive. If the ground connection is made at the sensor, then the aluminum
hex sleeve must be isolated from ground.
strain relief strap
Hex Sleeve
Electrically conductive
mechanical connection
(as supplied by MicroE Systems).