0 – 1sa and up contour cutting attachment (cca) – Mathey Dearman Saddle Machine Contour Cutting Attachment User Manual
Page 17
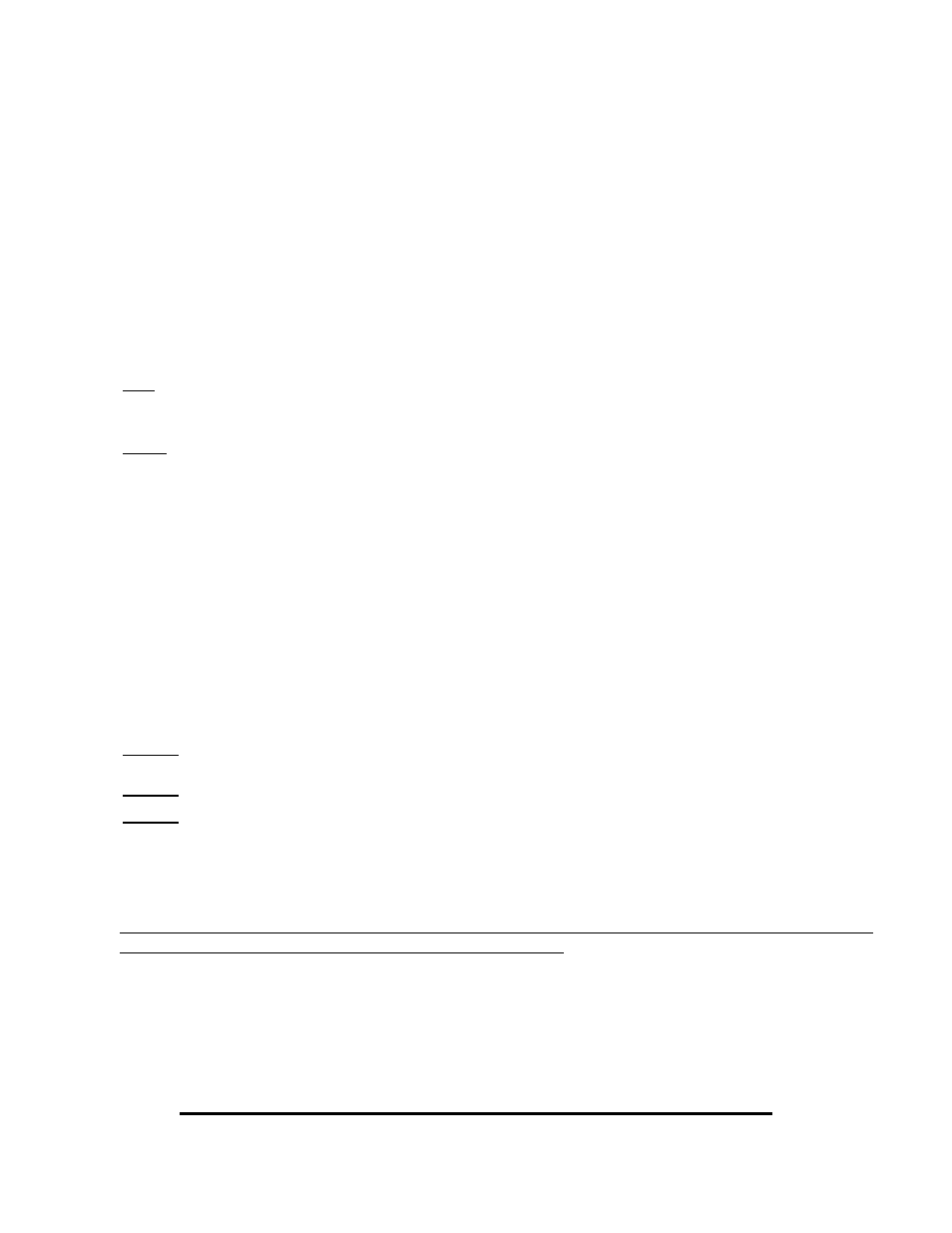
17
10.0 – 1SA and Up Contour Cutting Attachment (CCA)
Tools Require:
1 – 3/8” ratchet, 8” extension bar and 1/2” socket
2 – 7/16” combination wrenches
10.1 – Remove the Torch Arm and Torch Carrier Assembly from the Ring Gear of the Saddle Machine.
10.2 – If the Template is not installed, it should be installed at this time.
10.3 – Set-up the Saddle Machine on the pipe to be cut.
10.4 – Place a level on the pipe, check for level.
10.5– Remove the Follower Assembly from the CCA.
10.6 – Screw the R.H. Thd. Swivel Stud Ass’y of the support rods into the Ring Gear.
10.7 – Align the holes of the Beam Mounting Block over the studs in the Ring Gear and push. Secure the contour
attachment with the 2 hex nuts (5/16” x 18NC) that are provided with CCA. The L.H. Thd. Swivel Stud Ass’y of
the support rods should be installed simultaneously into the Beam End Bar.
Note: If removal of the Beam End Bar is required make sure the end of the CCA is supported.
10.8 –
Place a level on the top beam shaft and twist the Shaft Support Rod until the top Beam Shaft is at the same level of plumb
as the pipe.
NOTE: Adjust the Shaft Support Rods evenly so the CCA will not become twisted, affecting the operation and accuracy
of the machine.
10.9 –
The Torch Carriage Assembly should travel freely along the entire length of the Beam Shaft. It may be necessary to adjust
the Support Rods until free movement of the Torch Carriage is attained. Then tighten all nuts and lock nuts.
10.10 –
Install the Follower Assembly in the follower mounting block so the roller of thee follower assembly is centered on the
template. Tighten the thumb screw in the follower mount block.
10.11 – Release the Wing Screw on the back side of the Carriage Assembly
10.12 –
Rotate the torch around the pipe. Check Ring Gear as it enters and leaves the Saddle and Cap Ring assembly to make sure
there should be a minimum amount of deflection of the Ring Gear as it enters or leaves the Saddle and Cap Ring. To avoid
knocking the Saddle Machine out of time, it may be necessary to adjust the Shaft Support Rods until Ring Gear enter the
Saddle and Ring Gear properly.
10.13 –
Rotate the torch around the pipe. If the Follower Assembly does not follow the Template, adjust the Shaft Support Rods in
or out until Carriage Block moves freely.
10.14 –
Install the oxy/fuel or plasma torch (not furnished) in the Torch Holder. A Torch Holder is available for 1 3/8” / 35mm
diameter oxy/fuel or Plasma machine torch with a 32 pitch rack or a metric torch rack.
NOTE 1 – To install the plasma torch, simply remove the torch holder assembly and insert the stud on the side of the
plasma machine torch into the hold left by the removal of the torch holder assembly.
NOTE 2 – If rapid torch height adjustment is required, you will need to purchase a torch rack for machine torch.
NOTE 3 - The Contour Cutting Attachment is not designed for use with a 1 3/4" / 44.5mm or 2 ½” / 63.5mm Plasma
machine Torch.
10.15 – Increase friction of the torch in the Torch Holder by tightening Allen Head Cap Screws with a 5/32” Allen wrench.
10.16 – After the fuel or plasma torch is installed, rotate the CCA around the pipe to make sure it is maintaining the preset
distance around the pipe.
Note: When cutting the smaller diameter that the machine will cut it may be necessary to the torch bracket
(03-0116-082 to the bottom side of the torch carriage assembly.
10.17 – Light the torch by loosening the Wing Nut located at the top of the Torch Carriage and rotating the torch
outward; retighten the Wing Nut.
10.18 – After the torch is lit and the flame is adjusted, loosen the Wing Screw, move the torch to the proper torch bevel
angle on the Degree Plate and adjust torch to pipe height.
10.19 – Tighten the Wing Nuts to hold the torch at the proper bevel angle.
You are now ready to cut with the Mathey Contour Attachment