Mathey Dearman CGM Cold Cutting System User Manual
Page 20
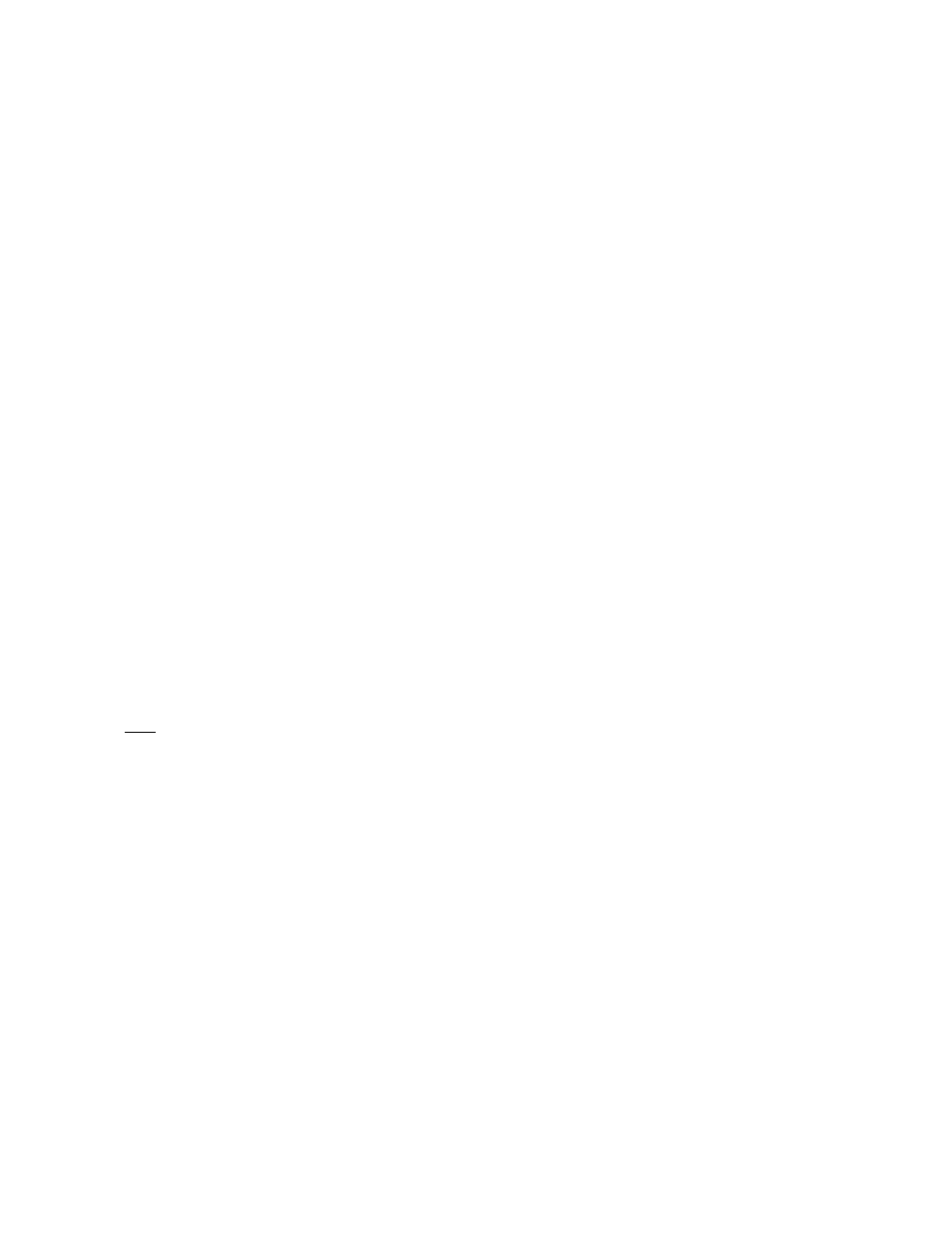
20
K. Remove all chips and other debris from the machine with a brush and water or air pressure.
L. Check all nut, bolts and fittings for tightness.
M. Spray a light film of oil on the CGM-1.
N. Place the CGM-1 in its Storage Box.
O. Store the Machine in sheltered area to avoid damage.
9. MAINTENANCE
9.1 ROUTINE MAINTENANCE
Plan all routine maintenance to the CGM-1 when the machine is not in operation. When the machine is cutting “heavy
wall pipe or high strength alloy pipes”, it is recommended the machine be thoroughly checked after each cut.
GENERAL –
A. Inspect the Cutter Blades for wear, chipped, damaged teeth and the integrity of the cutting after each cut.
B. Check the tightness of all nuts, bolts, screws and fittings at the end of each day of operation,
C. If applicable check the Double Mist Lubrication System on a regular basis during the cutting process make sure both
sides of the system are working properly. After each use check the Nozzles for obstruction and clean as required.
Always keep the synthetic coolant plastic bottle clean to avoid debris or dirt that may obstruct the Injection Nozzle.
PNEUMATIC MACHINE
-
A. Check the Air Filter / Lubrication Device and periodically check the assembly to be certain it is functioning properly
when using the Air Drive CGM. Drain the water from the water separator of the Air Filter / Lubrication Device on
a regulator basis. Replenish the oil in the inline Lubricator of the Air Filter / Lubrication Device with pneumatic oil
as needed.
B. Periodic checks should be performed on the Air or Hydraulic Power Supply as required by the manufacturer to
insure that the CGM will function properly.
Report any irregularities to the responsible manager.
HYDRAULIC MACHINE
–
In order to obtain the best performance from the CGM-1, it is important to choose a hydraulic fluid with the best
viscosity index for the ambient temperature the CGM will be working. To get the best performance out of the CGM,
especially under extreme cutting conditions, with variations in temperature, use synthetic additive oil with a high degree
of stability. For applications with vegetable biodegradable oil and special mixture (i.e.: glycol-water) contact Mathey
Dearman, Inc. and/or C.I.A. Mathey’s technical department.
A. When adding hydraulic fluid to the Reservoir of the Hydraulic Power Supply, filter the oil through a 25 micro filter.
Note: Failure to do filter the fluid may cause damage to the hydraulic blade and forward motors.
B. When adding hydraulic fluid to the Hydraulic Power Supply, use the same manufacturer of the hydraulic oil that
was originally in the reservoir.
WARNING:
Never run the CGM with a Hydraulic Power Supply that does not have a minimum of a 25 micro filtration system.
Do not mix various manufacturers’ hydraulic and viscosity fluid together.
Do not mix Hydraulic Oil or use varying viscosities fail due to the impacting of the machine performance and may
cause damage to the CGM-1 “O”.
C. Never use reprocessed hydraulic fluids.
D. Never disperse hydraulic fluid into the environment.