Insinger SW-48-RI User Manual
Page 11
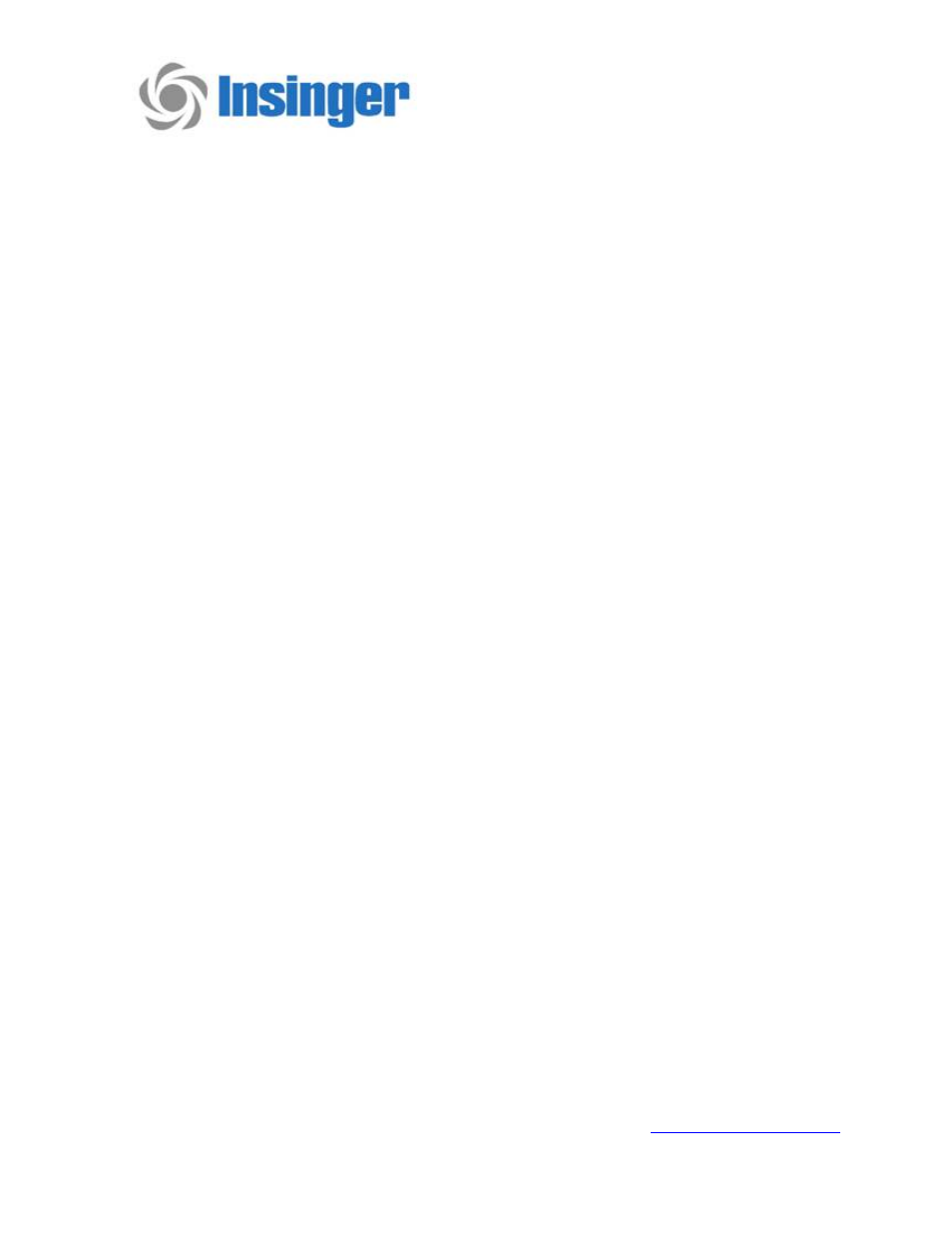
11
DOC SW‐48‐RI 2.2010
www.insingermachine.com
Step 4 DRAIN
: Provisions for the drain should be made next. The rack washer has a copper drain located as
shown on pages 26 - 28 of this manual (see page 6 for drain size). The drain should be plumbed
according to local code. Local ordinance may require a grease trap, vent, and/or a floor sink. If
required, these should be installed before the machine is installed. It is strongly recommended that
unions be used to allow the machine to be easily moved. Failure to do so may void the warranty.
Models that set in a pit do not require a drain connection because the wash tank drains directly into
the pit
.
Step 5 WATER SUPPLY HOOKUP
: The factory recommends 140° F (120° F minimum) hot water at
the machine (see page 3 for water line size). This may require a dedicated water heater for the pan
washer. If hard water is present, the manufacturer recommends installing a water softener or calcium
filter. Hard water deposits will shorten the life of many of the components on the pan washer, resulting
in higher maintenance costs. Please note that a union is installed at the point of hookup (see pages 26 -
28). This will allow the machine to be moved for service and cleaning. The customer must furnish a
shutoff valve on the supply side of the union. This shutoff should be easily accessible to the operator of
the machine.
Step 6 STEAM VENT
: The machine is equipped with a collar for 8" duct work as shown on pages 26 -
28. This duct should be directly vented to the outside of the building. DO NOT vent into a wall, attic,
or any other concealed space of the building, and avoid horizontal runs of duct.
The factory recommends 8" plastic pipe or stainless steel duct for the vent. If stainless steel is used, the
duct work should be installed with reverse joints so that the condensate inside the vent can drain back
into the machine without leaking. All seams should also be sealed with silicone sealant.
Generally, the machine is ordered with the fan option; a 700 cfm, ½ hp squirrel cage fan (3/4 hp on 50
Hz machines). The 700 cfm fan and adapter (provided) should be mounted and siliconed directly to a
flange on the top of the machine before the ductwork is installed. The ductwork attaches directly to the
exhaust of the fan. Wire is provided to wire the fan directly into the control panel. A dedicated breaker
and contactor for the 700 cfm fan are provided. The 700 cfm fan is controlled by a timer and runs for a
short time at the end of each cycle.
Note: Consult the factory before connecting any fan not supplied with the machine
Step 7 ELECTRICAL CONNECTION
:
The electrical connection to the machine should be made by a qualified
electrician. All steps should be taken to insure that the supply voltage to the machine is the same as the rated
voltage of the machine. Also check that sufficient amperage is supplied to the machine (see page 6 or page 7 for
ratings).
A main power shutoff, supplied by the customer, must be installed near the machine in a place easily