Powermax – Hypertherm Powermax600 Service Manua User Manual
Page 32
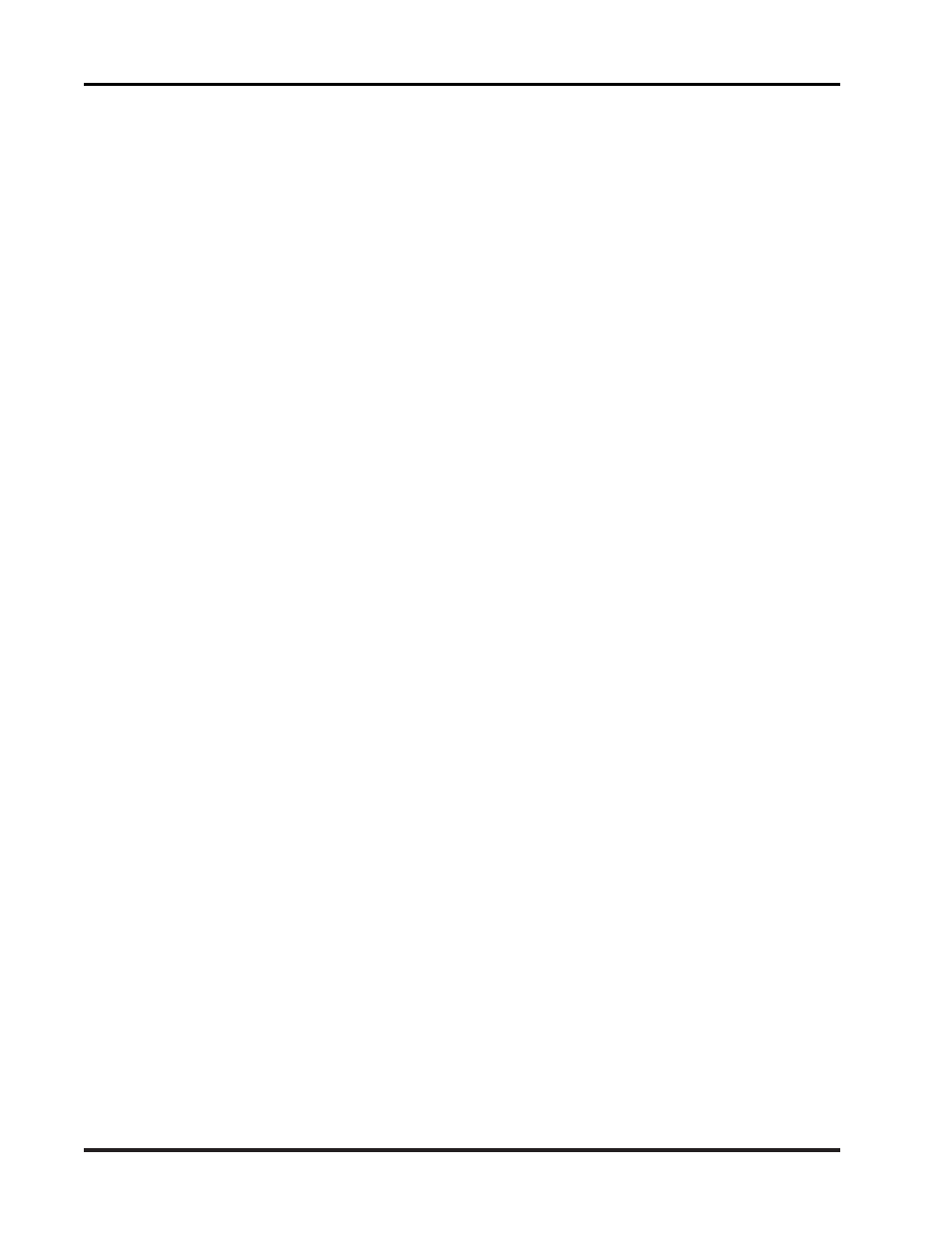
3-6
MAINTENANCE
powermax
600
Service Manual
See Figure 3-2.2.
AC power enters the system through the power switch S1 to the input diode bridge D18.
The DC voltage output from the diode bridge D1 supplies the inverter and supplies the
flyback system power supply (DC to DC converter) on the power board PCB2.
The power
board provides noise suppression and spike protection.
A
“soft start” is implemented via
power board resistor R
T5 and relay K1.
The inverter consists of several components: an isolated gate bipolar transistor (IGBT Q2),
the power transformer (T2), a current sense transformer (LEM), power factor choke and
sections of the power board.
The inverter operates as a pulse width modulator controlled
bridge circuit and is rectified by the output diode D2.
The output circuitry consists of 2 current transfer sensors located on the power board, the
pilot arc IGBT Q3 and the output choke L2.
The control board microprocessor monitors and regulates system operation and safety
circuits.
The current is set to the desired value by adjusting the current adjust potentiom-
eter
.
The system compares the set point to the output current by monitoring the current
sensor and adjusting the pulse width output of the inverter IGBT Q2.
The control board PCB3 includes a pilot arc control switch, allowing the operator to turn the
pilot arc ON (useful when cutting expanded metal) or OFF for maximum consumable life.
208-240/480 Volt Functional Description
10-99