Groth 7658A User Manual
Page 4
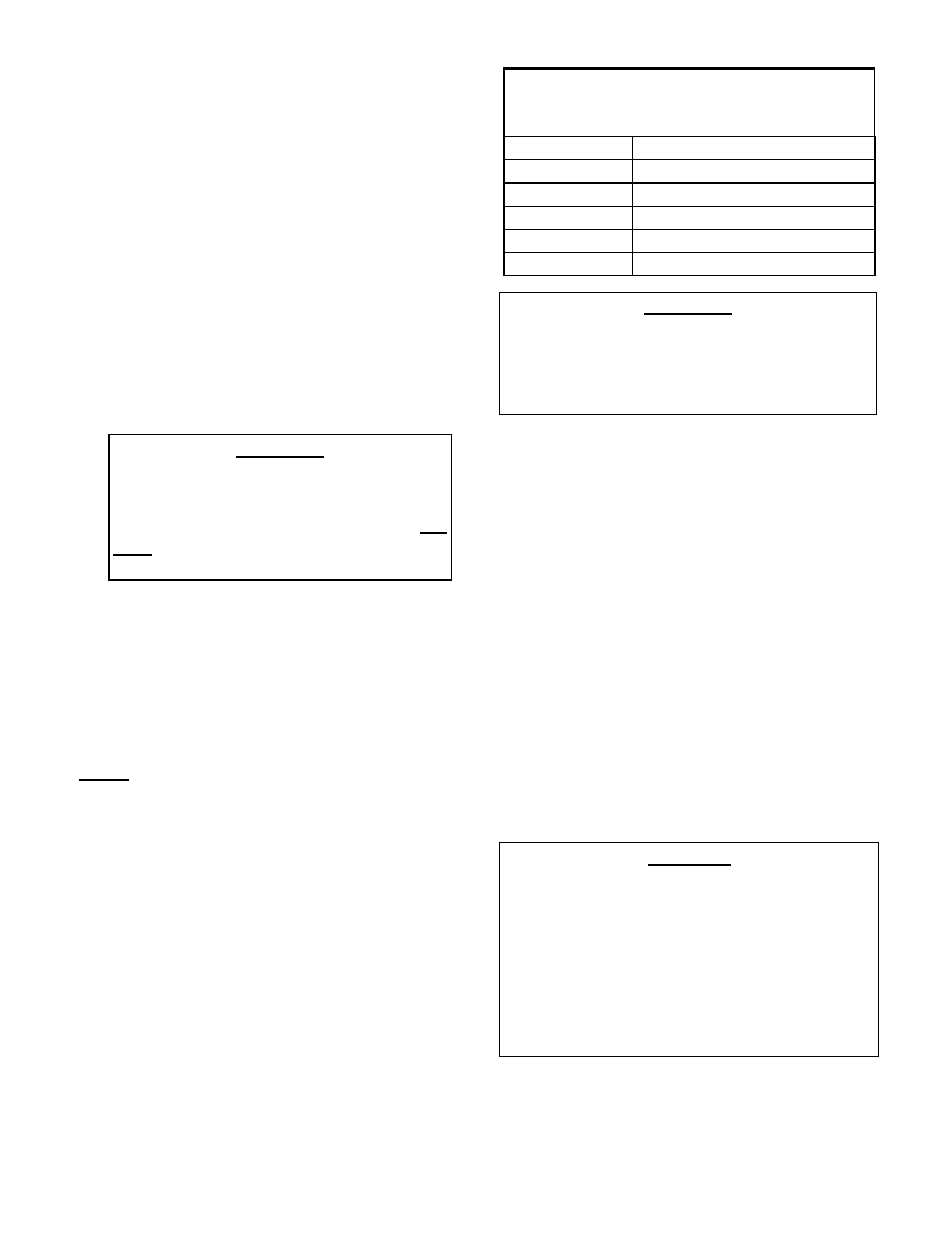
4
The following guidelines should be observed at
installation:
1. Remove any flange protectors and discard all
packing material.
2. Inspect the gasket seating surface of the
mating flanges. It must be clean, flat, free of
scratches, corrosion and tool marks.
3. Inspect the gasket; make sure that the
material is suitable for the application.
4. Lubricate all studs and nuts with an
appropriate thread lubricant. If the arrester
will see high temperature service or stainless
steel fasteners are used, select an anti-seize
compound such as moly-disulfide.
5. Center the gasket within the bolt circle.
WARNING
The lifting eyes on the element housing are
to be used for handling the housing only
during inspection and maintenance. DO
NOT use these eyes to lift the entire
detonation flame arrester assembly.
6. Set the arrester between its mating flanges or
nozzle. Position the lifting handles and
jacking nuts to facilitate future removal of the
flame arrester housing. Position the drain
and instrument ports to provide proper access
and function. (See Maintenance Instructions).
Install the studs and tighten nuts hand tight.
Notes:
•
When installing the Models 7658A in a
horizontal pipeline, use the lowest 1" ports to
drain condensed vapors from the housing.
Note previous warning when connecting the
drain piping.
7. Torque all fasteners to half the value listed in
Table 1 in a staggered, alternating pattern to
provide an evenly compressed gasket joint.
•
(Torque is an average value based on a nitrile
binder synthetic gasket, 1/32" thick and
lubricated threads).
8. Make up the final torque and check that no
further nut rotation occurs at the specified
torque value.
Table 1
PIPE FLANGE STUD TORQUE CHART
Lb.Ft. (Nm)
Size
Torque
2"
70 [95]
3"
70 [95]
4"
70 [95]
6"
110 [150]
8"
110 [150]
WARNING
After installation, all connections must be
inspected for vapor leakage. This may be
accomplished by static test, gas detector, or
"bubble" test using Snoop or similar liquid.
MAINTENANCE
For maximum operating efficiency the element of
a flame arrester must be inspected and
maintained at regular intervals. Frequency of
inspection should be based on the experience
gained in each application. Inspection of wetted
components is recommended at least once per
year or any time that one of the following
conditions occur:
•
Excessive pressure drop is encountered at a
known flow rate.
•
A flame front is detected.
Maintenance is accomplished by removing the
element assembly for inspection and cleaning or
replacement.
CAUTION
The connecting pipeline must be free of all
hazardous or flammable vapors before inspection
procedures begin. Before disassembling arrester
consult Material Safety Data Sheets (MSDS) for all
products that the arrester was exposed to in service.
The components should be cleaned according to
MSDS procedure. Take appropriate safety
precautions regarding eye protection, skin contact
& respiration.
1. When removing the element housing for
maintenance, support the weight by