Formax FD 670 User Manual
Page 13
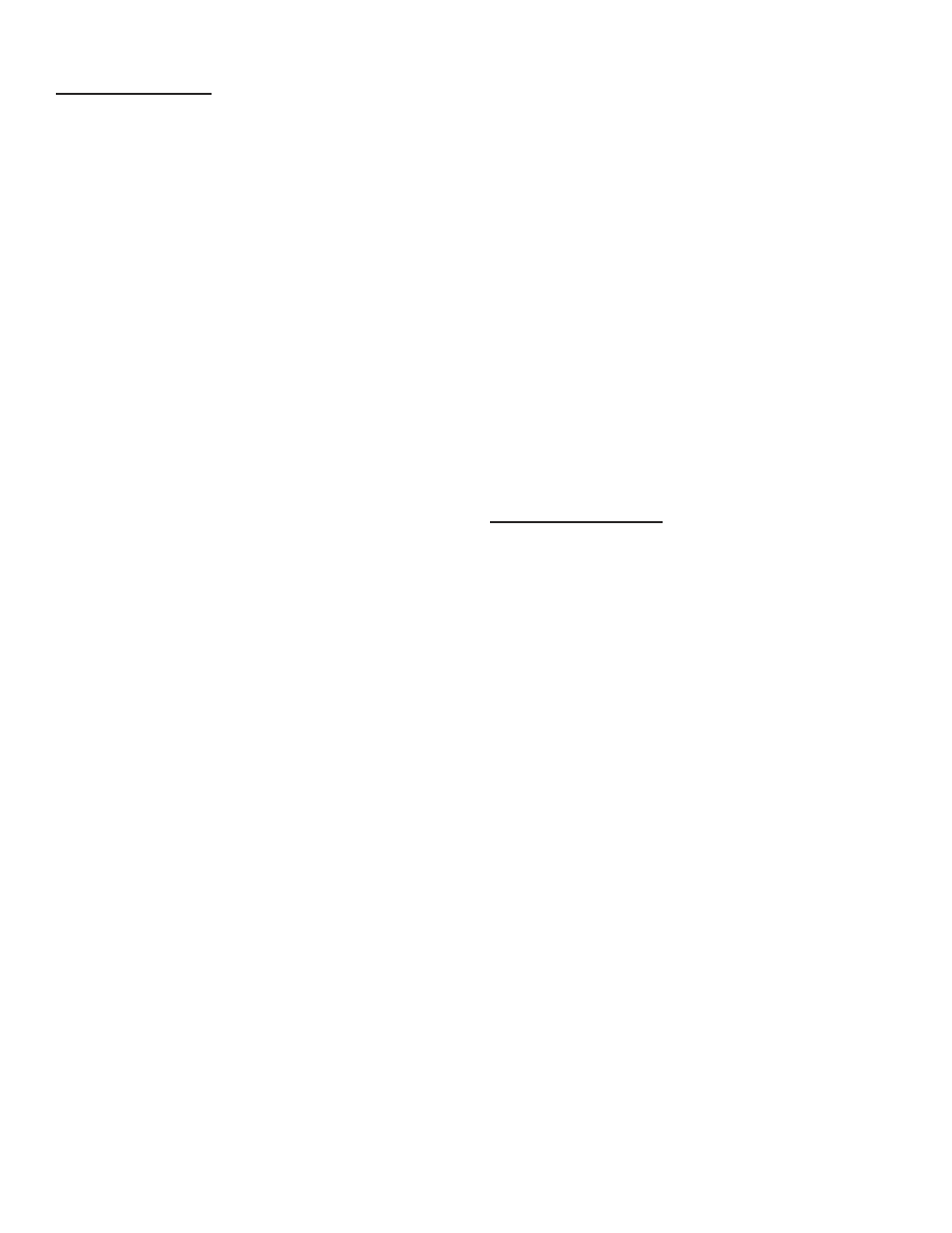
9
FORM SET-UP PROCEDURES
WITH IMPRINTER
NOTE: It is recommended that
numbered forms or
checks fed into imprinter should be last form first, right
side up.
1. Center leading edge of form at infeed end of
machine so that outer edges of form extend equally
beyond guide straps on each side. If you find that
edges come within about 1/4” of guide straps, offset
form in either direction to avoid this condition.
2. If form length is 3 1/2”, 7”, 10 1/2” or 14”, rollers
must be timed. Time rollers by activating jog switch
until timing marks on the rollers are vertical and in view
in cutouts in feed and snap roller covers.
3. Position tractors by releasing and sliding to proper
form width. Raise tractor gates. Place forms on feed
pins as shown in (Fig. 8). Close tractor gates and
secure in position.
4. Loosen thumbscrews on ink roller unit and slide unit
away from signature area on form. (Fig. 12)
5. Loosen setscrew on plate cylinder. if setscrews are
not in view, rotate free wheeling cylinder until they are
in view.) Horizontally align plate cylinder with signature
area on form. Tighten setscrews. (Fig. 12)
6. Loosen setscrews on imprint cylinder. (if setscrews
are not in view, use jog switch to bring them into view.
Fig. 11)
7. With no signature saddles on imprint cylinder, move
forms forward so signature area is centered over plate
cylinder shaft.
8. Center signature cylinder over signature area
(NOTE: Setscrews should be facing you.) and center
signature plate locator pins directly over imprint area
on form. Tighten setscrews.
9. Advance forms forward so that next horizontal
perforation aligns at top edge of plastic tractor or
alignment mark on metal tractor. (Fig. 11)
10. Move timing collar so that mark on collar aligns
with mark on side frame. Tighten setscrews. (Fig. 11)
11. Remove forms from tractors. Install signature
patches on imprint cylinder. (Fig. 12)
12. Move ink roller directly over signature patch on
imprint cylinder. Jog forward, if necessary, so that
imprint cylinder turns to a point where signature patch
should touch ink roller. Adjust ink roll thumbscrews so
ink roll turns when signature patch makes contact.
For darker impression, turn adjustment thumbscrews
clockwise. (Fig. 19)
NOTE: The signature saddle has been factory adjusted
to fit a .092 thick signature patch. If adjustment is
required to lower or raise the height of signature
saddle for a different signature patch thickness,
release imprinter side plates from their locked
positions. Pull back latch finger to release plates. (Fig.
11. Loosen side setscrews to free top setscrew Turn
top setscrew in at half-turn increments until required
height is reached. Tighten side setscrews and slide
imprinter module back into position.
NORMAL LOADING
NOTE: Imprinter must be timed each time you load a
different form into Burster for imprinting.
1. Jog machine forward until timing collar mark is
aligned with side panel mark. (Fig. 11)
2. Place forms to leading edge of plastic tractors.
On metal tractors place forms leading edge to timing
mark.
3. Advance (jog) forms forward through imprint area.
Stop leading edge of form in front of slitters.
4. Move slitters to trim proper amount of trim
and engage slitter blades by turning wedgers
counterclockwise. Lock down slitters.
5. Advance forms through slitters and check for
proper slitting. Advance on through to Tear Bar.