0 technical data (circuit board only), Worcester actuation systems – Flowserve DRC-17 User Manual
Page 25
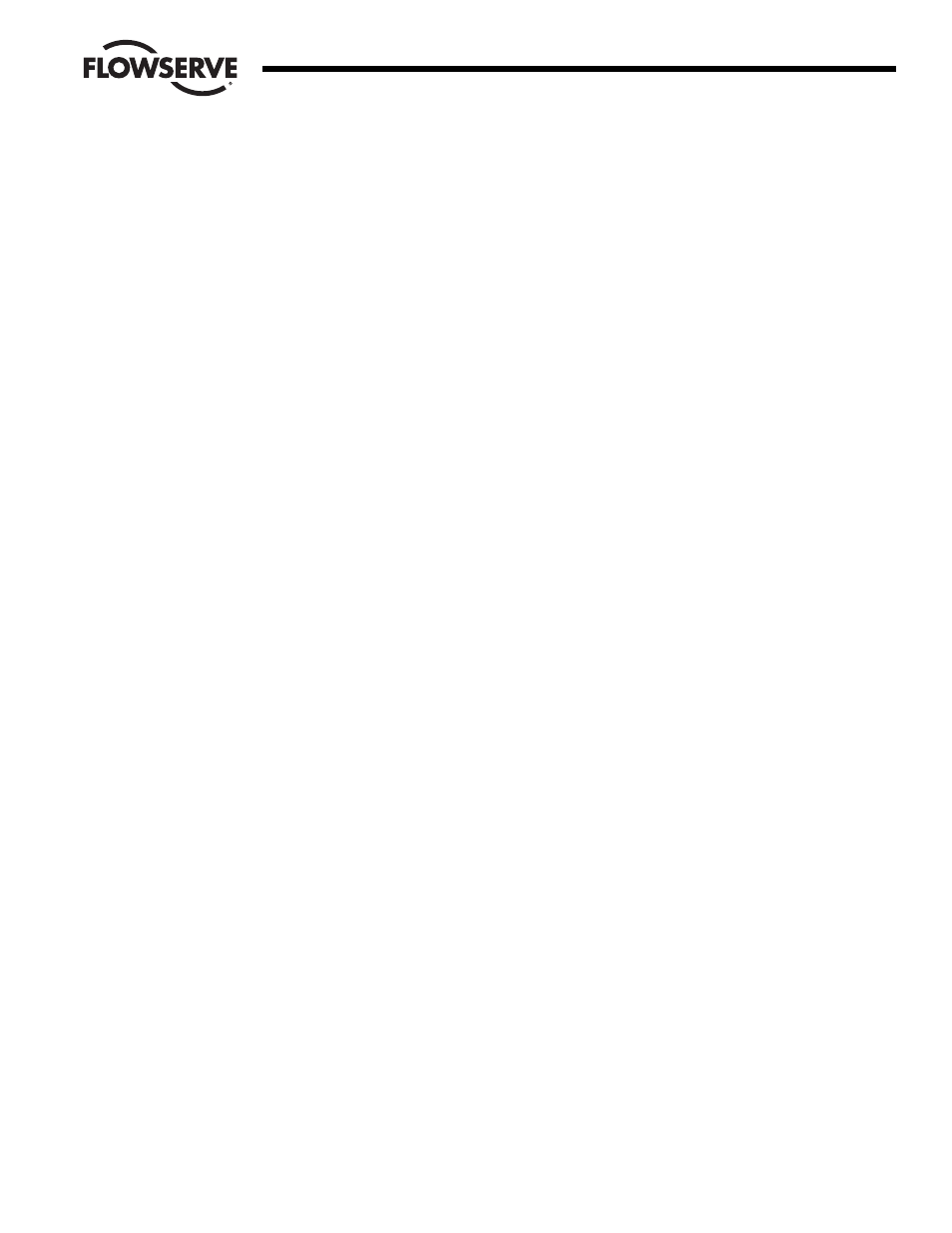
WCAIM2058
DataFlo Digital Electronic Remote Controller DRC17
25
Press ENT to begin the thermocouple calibration
procedure. The display will show TC Type alternating with
the thermocouple type. If the thermocouple type is
correct, go to the next step. Otherwise, press the ENT key
and use the
and
keys to change the type. When the
correct type is displayed, press the ENT key to lock in the
type. Note that if the type is changed, the upper and lower
ranges will be set to the widest possible range. Be sure to
check the upper and lower range after setting the type.
Press the
key to display Units alternating with the
current degree units. If the temperature degree units are
correct, go to the next step. Otherwise, press the ENT key
and use the
and
keys to change the value to either
Deg C or Deg F. When the correct units are displayed,
press the ENT key to lock in the units. Note that if the
units are changed, the upper and lower ranges will be set
to the widest possible range. Be sure to check the upper
and lower range after setting the units.
Press
to advance to the Upr Rng display which
alternates with the upper temperature range. If the upper
range is correct, go to the next step. Otherwise, press the
ENT key and use the
and
keys to change the upper
range. The upper range must be at least 100°C or 250°F.
When the upper range is correctly displayed, press ENT
to lock in the value.
Note: the lower range is fixed at 0°C or 32°F and cannot
be changed.
With the temperature range properly set, press the
or
keys to get to the Hi ADC V display alternating with its
voltage value. Press the ENT key to begin voltage
calibration. Using the thermocouple simulator, simulate
the upper limit temperature and adjust the gain
potentiometer on the module such that the voltage
displayed is between 4.200 volts and 4.700 volts. Press
ENT to lock in the upper limit voltage.
Press the
key twice to get to the Lo ADC V display
alternating with its voltage value. Press the ENT key to
begin voltage calibration. Using the thermocouple
simulator, simulate the lower limit temperature. Do not
adjust the gain potentiometer in this step! Press ENT to
lock in the lower limit voltage.
The thermocouple process module is now calibrated for
the specified range. Press
to return to the Run Mode.
5.0 Technical Data (circuit board only)
5.1 Power Supply Voltage
Model xx – DRC17 – x – x – x – 120A:
120 VAC ± 10% 50/60 Hz
Model xx – DRC17 – x – x – x – 240A:
240 VAC ± 10% 50/60 Hz
5.2 Power Consumption
Power Consumption (all models): 3 Watts
5.3 Setpoint Input Specification
5.3.1 Current Setpoint Input
Model xx – DRC17 – 4 – x – x – xxxx:
4 to 20 milliamps, approximately 220 ohms load
5.3.2 Potentiometer Setpoint Input
Model xx – DRC17 – K – x – x – xxxx:
1000-ohm potentiometer
5.4 Process Input Specification
5.4.1 Current Process Input
Model xx – DRC17 – x – 4 – x – xxxx:
4 to 20 milliamps (220 ohm burden)
5.4.2 RTD Process Input
Model xx – DRC17 – x – R – x – xxxx:
100-ohm platinum RTD only
5.5 Motor Driver Board Specifications (all models)
Maximum Normal Starting or Inrush Current:
10 amps for 1 second
Maximum Stall Current: 8 Amps for 1 minute
Maximum Running Current,
Resistive Load, 90% Duty Cycle: 5 amps
Maximum Running Current,
Inductive Load, 90% Duty Cycle: 3 amps
Maximum Peak Voltage at Load Circuit: 800 Volts
5.6 Alarm Output Driver (all models)
Maximum Voltage: 50 volts (across TB2 terminals 9 and 10)
Maximum Continuous Current: 100 milliamps
5.7 Utility Voltage Supply
Voltage Output: 5.0 volts
Voltage Tolerance: ±4 %
Maximum Continuous Current: 50 milliamps
5.8 Position Feedback Module Current Output
Maximum Voltage Output: 8 volts
Load Allowed: Less than 350 ohms
Flow Control
Worcester Actuation Systems