Worcester actuation systems – Flowserve DRC-17 User Manual
Page 21
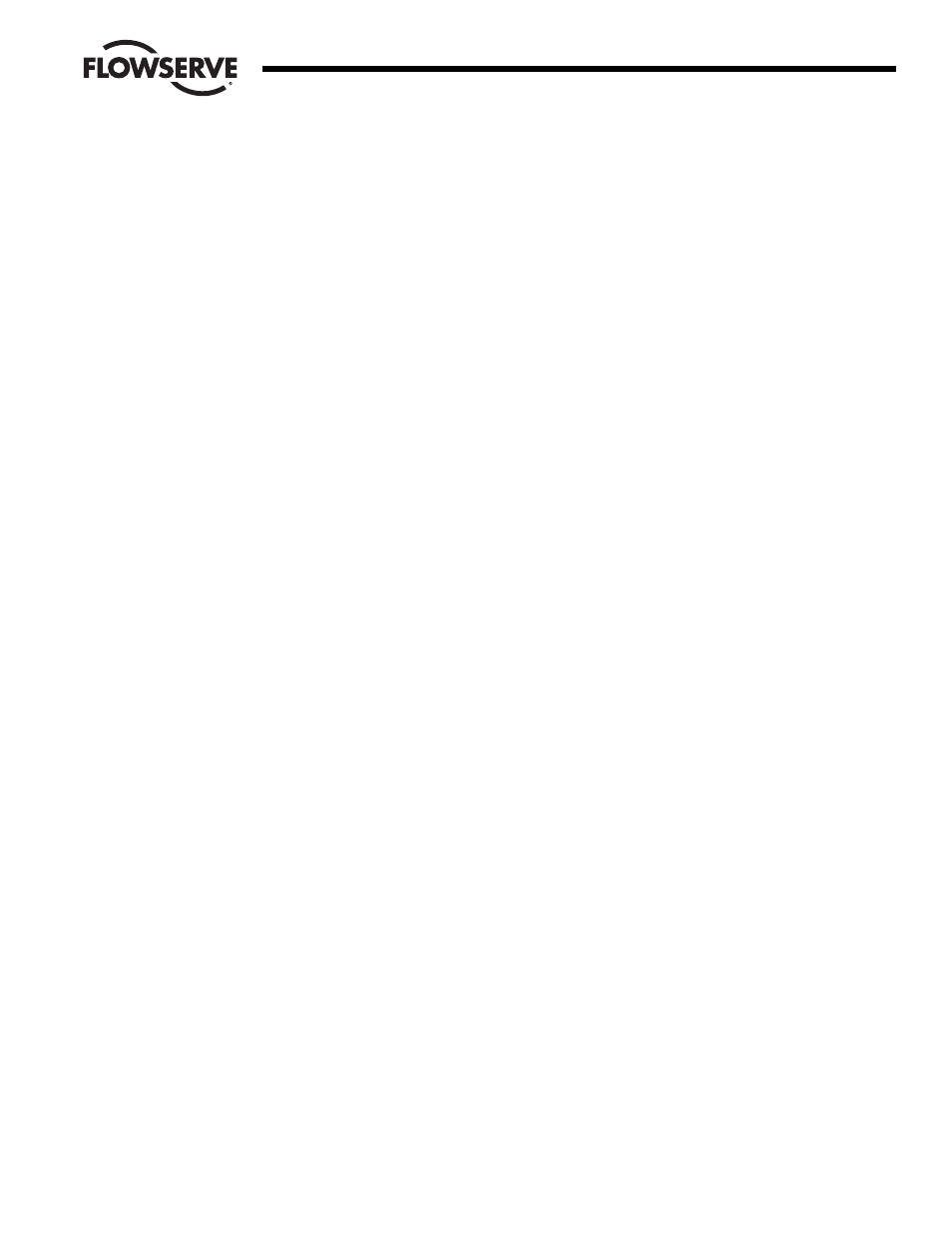
WCAIM2058
DataFlo Digital Electronic Remote Controller DRC17
21
established in Program Mode (paragraph 4.6.2). When
the correct manual setpoint is displayed, press the ENT
key to lock the value.
The display will alternate Man Setp and the setpoint value.
Press
to return to the Run Mode and use the manual
setpoint specified.
4.8 Manual Position Mode
Manual Position Mode is used to manually position the valve. All
control ceases while in this mode and the valve position is
shown. This mode is also used to access the Auto-Tune feature
of the DRC
4.8.1 Entering the Manual Position Mode
In the Run Mode, press either the
key or the
key
until the mode display appears.
Press ENT to edit the value. It will start blinking the
current mode.
Press either
or
until MPOS is visible.
With MPOS blinking, press the ENT key to change to the
Manual Position Mode. The name Shft Pos will alternate
with the valve shaft position. 0% is the full clockwise
position; 100% is the full counterclockwise position.
The Manual Setpoint Mode is exited by pressing the
key to return to the Run Mode.
4.8.2 Changing Valve Position
When the mode is entered, the display will alternate
between Shft Pos and the valve shaft position. Press and
hold the
key to rotate the valve in a clockwise (CW)
direction; press and hold the
key to rotate the valve in
the counterclockwise (CCW) direction. The valve will
rotate as long as the key is pressed.
Note: It is possible to exceed the calibrated CW and CCW
position limits in this mode. Care should be taken when
rotating the valve when its position is close to the limit of
travel in either direction.
The valve position expressed as a percentage of travel will
be displayed as the valve rotates. When the valve is not
commanded, the display will alternate between Shft Pos
and the valve shaft position.
4.8.3 Auto-Tune
Auto-Tune is a feature of the DRC that allows an operator
to determine a starting point for PID control parameters.
Once the necessary data is entered, the Auto-Tune
procedure is performed automatically. Before Auto-Tune
is performed, the valve shaft should not be at either end
of valve travel. A shaft position close to 50% would be a
good starting point.
Remember that Auto-Tune results are only suggestions
for the PID terms. Automatic tuning does not always
determine optimum terms. The operator should closely
examine the results before installing them.
4.8.3.1 Starting Auto-Tune
NOTE: At any point in the Auto-Tune procedure, the
procedure can be aborted by pressing the
key
which will return control back to the Manual Position
Mode.
Using the
and
keys, set the valve position to the
desired starting point. This is a center point about
which the tuning will be performed. The shaft should
not be located close to either travel limit (i.e., full CW
or full CCW).
When ready to start the tuning, press the ENT key.
The display will show the Autotune name followed by
Shaft dS alternating with a default valve increment.
The valve increment is the amount the valve will move
during the Auto-Tune procedure.
If the valve increment displayed is already correct,
this step can be skipped by pressing the
key.
Otherwise, press ENT to edit the valve increment
amount. Use the the
and
keys to adjust the
amount to the correct increment. The value will not
be able to be set less than 1% nor greater than either
40% or the distance to the nearest travel limit,
whichever is smaller. When valve position is changed,
it is important to allow the process to settle with the
new position. When the value is correctly displayed
and the process has stabilized, press the ENT key and
the automated procedure will begin.
4.8.3.2 The Automated Auto-Tune Procedure and Results
NOTE: At any point in the automated procedure, the
procedure can be aborted by pressing the
key
which will return control back to the Manual Position
Mode.
The automated procedure begins by measuring
fluctuations in the process. The display will alternate
between Fluct and a measure of tenths of a unit of
process variation. This measurement will continue for
one minute.
When the fluctuation measurement has completed,
the shaft will be moved clockwise by the specified
valve increment. The display will show Step #1 while
the valve is moving.
When step 1 valve movement has completed, the
display will alternate between Step #1 and the number
of seconds the step has taken. Step 1 is waiting for
the process to stabilize at the new valve position. If
the process does not stabilize within 30 minutes, the
tuning procedure will be aborted and the TIMEOUT
message will be displayed. The error message will
remain until the ENT key is pressed.
When step 1 has completed, the shaft will be moved
counterclockwise by twice the specified valve
increment. The display will show Step #2 while the
valve is moving.
Flow Control
Worcester Actuation Systems