Replacing the seal weld univalves – Flowserve V-370 R3 Edward Valves User Manual
Page 18
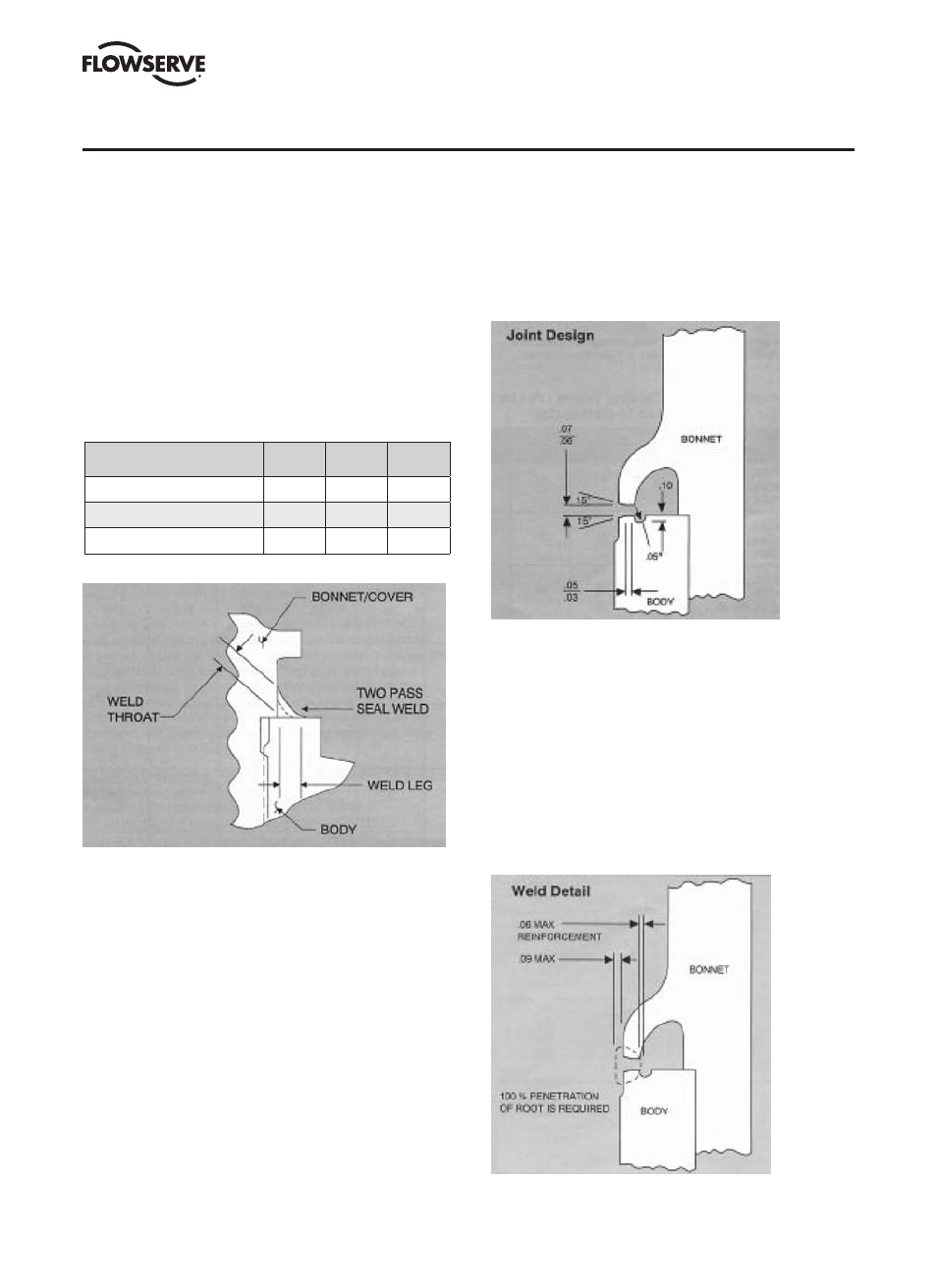
EDWARD UNIVALVE USER INSTRUCTIONS ENGLISH 12-13
18
A105 AND F22 UNIVALVES
Seal weld of A105 (Carbon) and F22 (Low-alloy) Univalves
are made using a “Fillet” weld.
RE-WELDING
• To allow welding gases to escape, do not fully seat or
backseat valve.
• Weld surfaces shall be clean and dry.
• Preheat to 300°F – 400°F.
• Weld A105 Univalves with SFA 5.1 E7018 electrodes and
F22 Univalves with SFA 5.5 E9018-B3 electrodes.
• Deposit weld metal to meet dimensions shown in table
below.
REPLACING THE SEAL WELD UNIVALVES
Univalve Size
Min. Leg
Min.
Throat
Min.
Passes
1-1/2 and smaller
3-16
1/8
2
2 (except Class 4500)
1/4
3/16
2
2 (Class 4500 and valves over 2)
3/8
1/4
2
JOINT
Seal welds of F316, F316L and F347 (Stainless Steel)
Univalves are made using a “Canopy” weld.
• Univalves should be prepared for the Joint design shown
below.
RE-WELDING
• To allow welding gases to escape, do not fully seat or
backseat the valve.
• Weld surfaces shall be clean and dry.
• Preheat to 70°F – 150°F.
• Maintain an interpass temperature of 350°F maximum.
• Weld F316 Univalves using SFA 5.9 ER316L bare rod,
F316L Univalves using SFA 5.9 ER308L bare rod and
F347 Univalves using SFA 5.9 ER347 bare rod.
• Deposit weld metal to meet dimensions shown in sketch
below.
F316 AND F347 UNIVALVES