Repair procedures – Flowserve V-377 R4 Edward Valves User Manual
Page 13
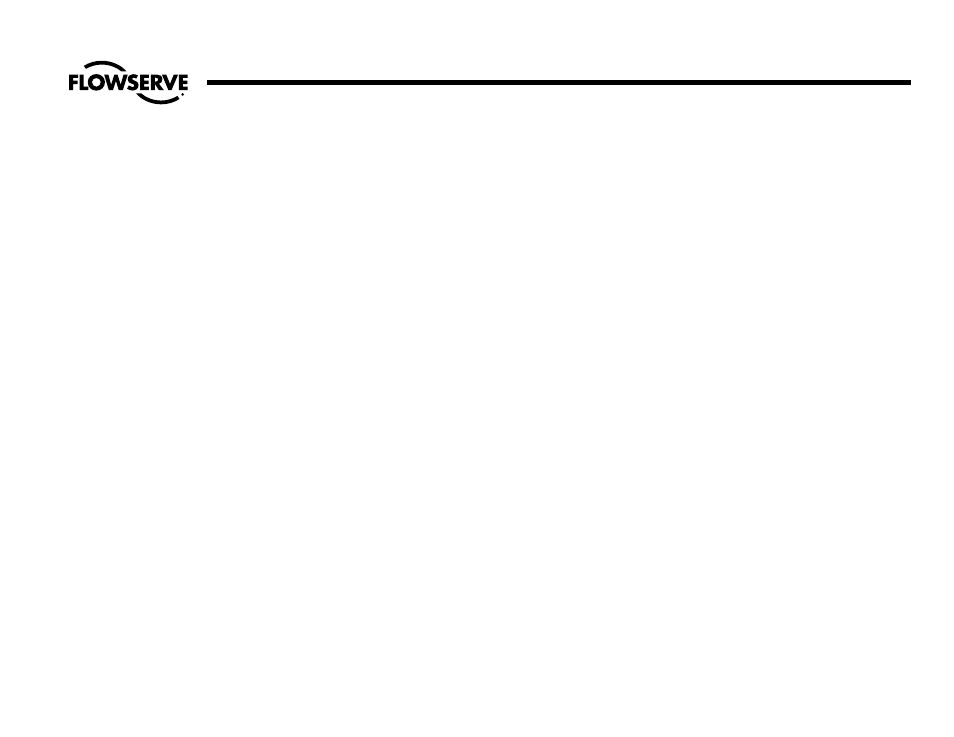
13
Flow Control Division
Edward Valves
VALVE BODY REPAIRS
Body Bore Gasket Seal Area Repair
with Metal Gasket Only
Pressure-seal valves made prior to 1952
were made with a 47° bonnet seal angle
and the body bore seal was in the parent
metal of the body castings. In 1952 the
design was changed to a 25° seal angle
and the body castings were inlayed with
18-8 stainless at the seal area. When a leak
developed on the older valves, the gasket as
well as the body bore were wire drawn.
If the depth of defects are .010” or less,
the seal area can be honed using a
portable Sunnen Hone. This device is
adjustable for different bore sizes and can
be operated by one man using a portable
electric drill of 1/2“ to 3/4“ capacity.
When the defects are greater than .010”,
welding will be required to cut down the
repair time.
First make visual inspection all around this
area, noting, if possible, where flaws may
occur. Next wash the area with a suitable
solvent, drying with clean rags and, if nec-
essary, polishing with a fine grade of
emery cloth to remove any undesirable
scale or foreign matter that may have been
deposited on the area suspected of having
flaws. Use a dye penetrant test if cracks
are suspected.
Where it is necessary to repair the body
inlay by welding, note the following:
1. Prior to any cutting or welding opera-
tions being performed on the valve, it
is necessary that adequate seat joint
protection be provided and some
means of insurance against getting
chips, weld spatter or other foreign
matter into the pipe line if the valve is
permanently mounted. A round piece
of sheet metal placed over the seat
and taped in place will furnish
adequate protection.
2. Chip out the defective area in the
body, being careful to remove the
affected portion to its end, inside
the casting, and to thoroughly clean
it away.
3. With a small hand grinder, grind the
chipped area smooth.
4. Preheat an area large enough
around the imperfection so that dur-
ing the entire welding operation heat
will be retained at approximately
400°F.
5. Use a stainless steel inlay selected
from either 18-8 stainless steel rod,
Harstain 18-8, Stainlend “K” 18-8,
Stainweld 18-8 or equivalent.
6. Lay the weld in thin, even layers,
peening each layer before proceed-
ing with the next, and being careful
to maintain a temperature above
400°F in the area being repaired.
Peening the bead actually stretches it
and counteracts its tendency to con-
tract and shrink as it cools. The last
layer of weld must overlap onto the
sound metal to ensure a weld without
an undercut at the edges. The over-
lapping should be done along this
edge by using a welding rod of 1/8”
maximum diameter. The last layer
should bring the height of the welded
area up to 1/16” above the original
surface, as checked with a straight
edge along the body bore.
For this type of weld repair, it is rec-
ommended that the last layer be
pounded while still hot with the flat
face of the hammer. Thermal stress
relieving is not recommended.
With a hand grinder, rough grind the
welded surface to within about .010”
of the finished surface. A simple
template cut from thin sheet metal
and having the same arc as the body
bore diameter, and a straight edge
laid along the body bore can be
used as a guide. A final cut then can
be made, using a fixture similar to
the one shown in Illustration No. 9.
Final finishing can be done with the
adjustable Sunnen hone described on
page 17.
After removing all dirt, chips, slag,
spatter, and grinding dust from the
body, the bore should be polished
with fine emery cloth and then thor-
oughly cleaned before reassembly of
the valve.
It is best that a new pressure-seal gas-
ket be used upon reassembly.
Body Bore Guide Rib Repair
Where more than one guide rib is
involved, each rib should be preheated
and welded before proceeding to the next.
1. Follow steps 1 through 3 of the sec-
tion titled “Body Bore Gasket Seal
Area Repair” on this page.
Repair Procedures