4performance testing of pumps – Flowserve High Temperature Metal Bellows Seals User Manual
Page 5
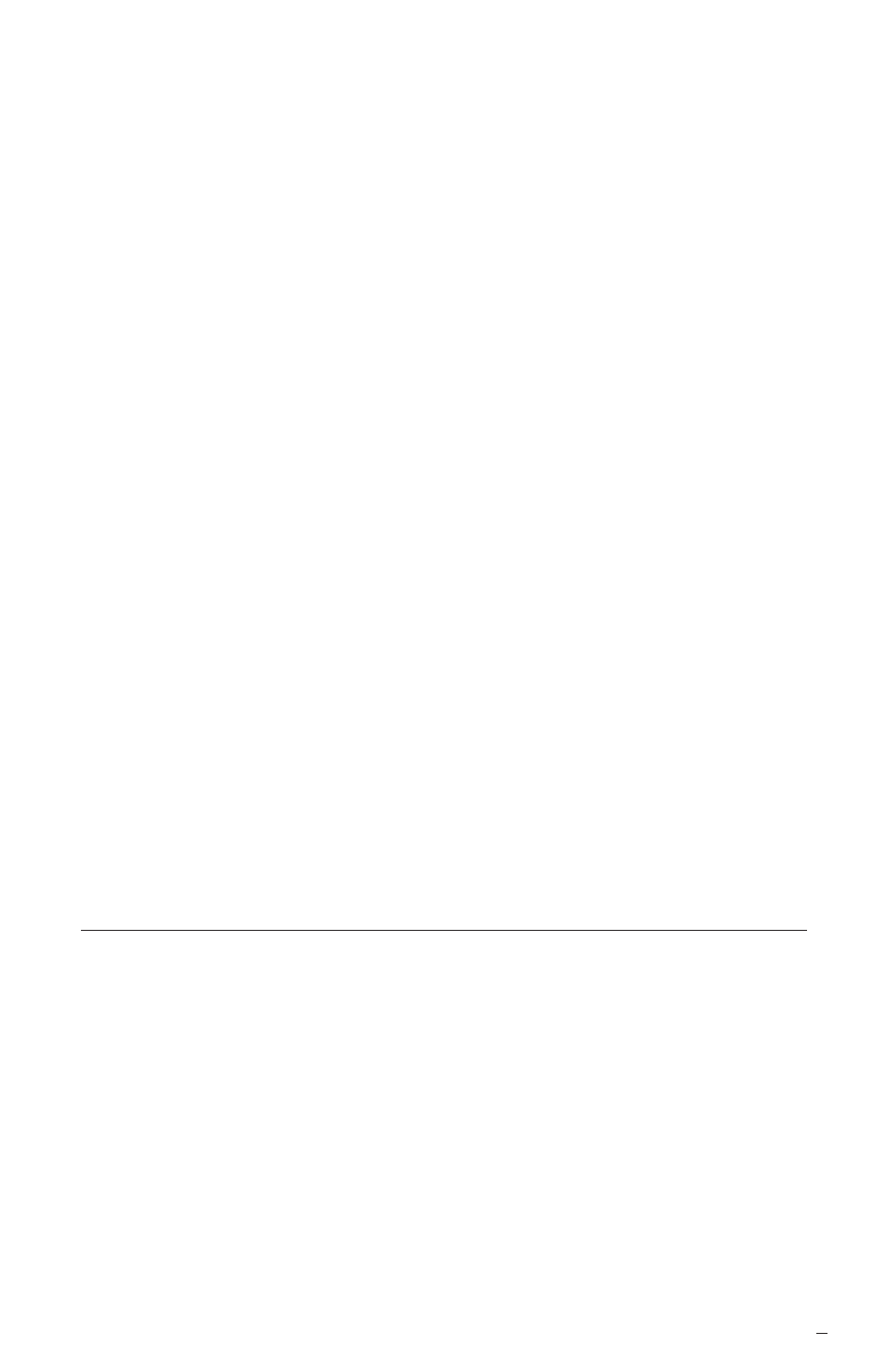
5
Per API 682 / ISO 21039 and unless otherwise specified, the minimum internal
diameter for piping should be 12.7 mm (0.500 inch) for shaft sizes up to 60 mm
(2.500 inch). Larger shaft sizes should use a minimum pipe diameter of 19 mm
(0.750 inch).
For “loop type” systems (Plan 23, 52 and 53 A, B, C)
All piping loops should allow a high point vent. Minimize restrictions, total tube
length and the number of bends. Use smooth, large radius bends; do not use
elbows, tees, etc. Tubing runs should be sloped continuously up or down to allow
adequate circulation, proper venting and draining. Make sure the loop, including
seal gland, does not include vapor traps. Unless otherwise specified, reservoirs
and coolers must be mounted 45 to 60 cm (18 to 24 inch) above the seal inlet
or outlet connection, whichever is the highest, to promote thermal siphoning in
standby conditions. Refer to the Flowserve Seal Support Reservoir Installation
Instruction (FIS123eng) for additional information regarding proper reservoir
installation.
For steam quench systems (Plan 62)
A steam quench is an essential plan on single high temperature bellows seals.
Steam pressure should be maintained less than 0.2 bar (3 psi) such that wisps
of steam are visible exiting the seal gland area. Steam quench inlet should be
on top of the gland with a drain at the bottom. Steam traps designed for this type
of service should be installed and maintained. Before startup, ensure that all
condensate is drained from the supply line. Open the steam quench slowly
before the pump is preheated to prevent thermal shock.
Seals Equipped with Excess Leakage Detection
Excess leakage detection, used normally with single seals or dual un-pressurized
seals, is commonly achieved by monitoring liquid level or pressure increases.
With such an arrangement, the drain line must slope down continuously to the
point of exit.
4
Performance Testing of Pumps
Pump manufacturers will often run pump performance tests on water with
the mechanical seal installed. If the product pumped during field operation is
not equal to water, then seal designs and face materials will require special
precautions to prevent damage to the seals during these tests. For example,
in seals with two hard faces, alternate face materials or seal designs may be
provided that are more suitable to the test medium. These faces are to be
replaced with the specified face materials after testing is complete. A mechanical
seal with a hard face combination can be safely tested on water provided that
seal chamber pressure during the test does not exceed 5 bar (73 psi) and face
speeds do not exceed 10m/s (33 ft/s).
When high temperature seals with flexible graphite gaskets are tested on water,
the seals must be carefully dried to remove any water that may have been