2seal installation – Flowserve High Temperature Metal Bellows Seals User Manual
Page 3
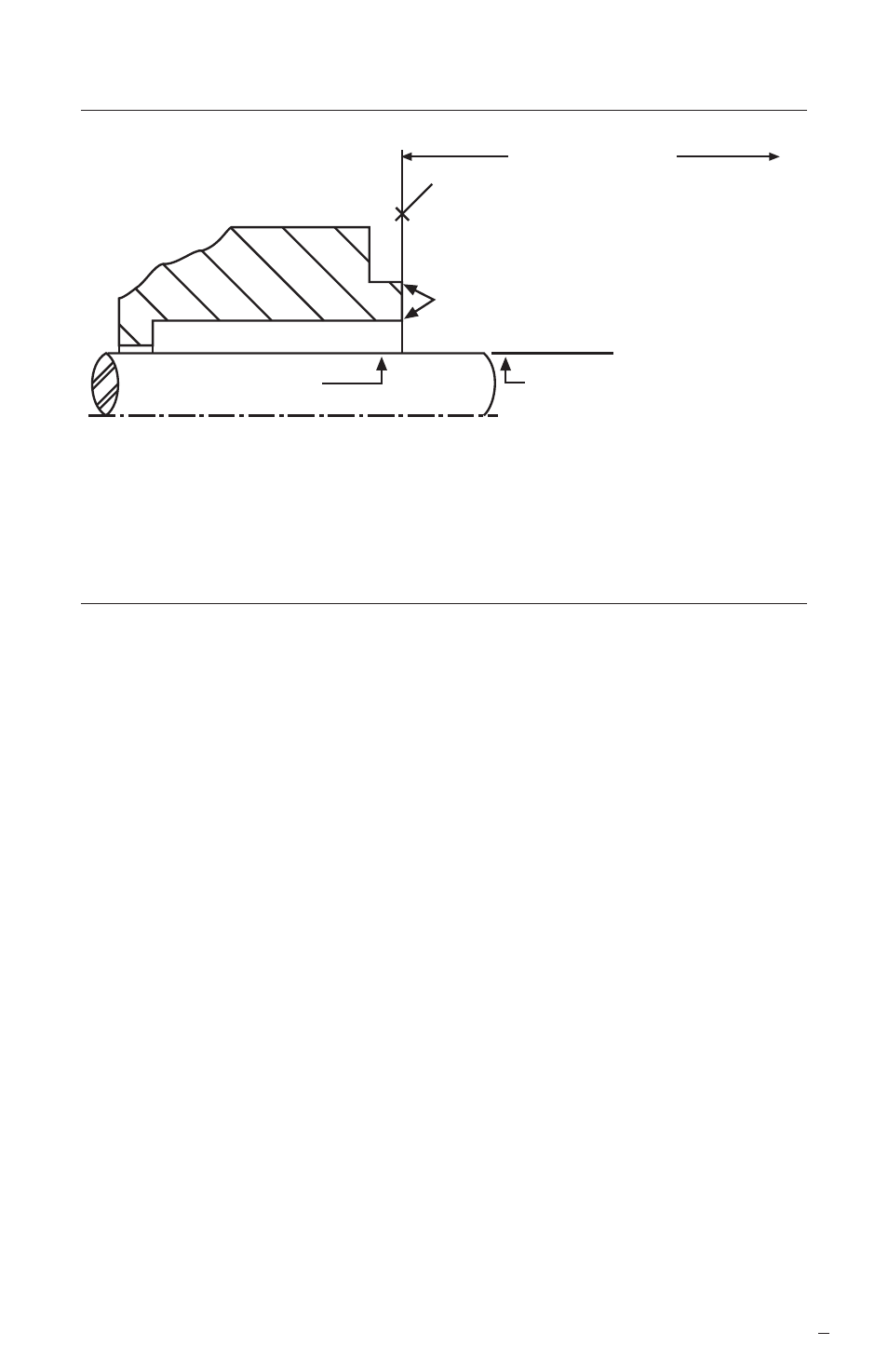
3
Seal Chamber Requirements
Figure 1
2
Seal Installation
Cartridge high temperature bellows seals are packaged in a manner to protect
the flexible graphite gaskets during shipping. Carefully unpack the cartridge seal
and separate the gaskets. Flexible graphite gaskets are very fragile; handle
with care.
2.1 Some mechanical seals are sensitive to rotation direction. Verify that the
directional rotation of the shaft corresponds to that of the mechanical seal
before installation. Seals for between-bearing shaft pumps may use
different designs for each end of the pump; check the seal assembly
drawings carefully.
2.2 Remove the axial drive collar screws and drive collar, if installed.
2.3 Place seal gland gasket into its groove. Small dots of grease may be
applied in the seal gland gasket groove in 4 to 6 places to hold the gasket
in position. Care must be taken not to get grease on the seal faces.
2.4 If the sleeve includes a sacrificial O-ring, lightly lubricate it to facilitate
sliding along the shaft. Use a lubricant appropriate for the application.
2.5 For overhung shaft pumps:
2.5.1 Slide the drive collar onto the shaft with the gasket side of the
collar facing the seal chamber. Note: the gasket is installed
separately, in the next step. If the collar assembly includes a key
drive, pin and/or lock ring, install these items. Again, refer to the
assembly drawing.
2.5.2 Carefully slide the flexible graphite gasket along the pump shaft
and seat uniformly against the drive collar.
To first obstruction
Seal housing bore to have 3.2 μm
(125 μinch) R finish or better
Sleeve or shaft finish to be
0.8 μm (32 μinch) R or better
a
a
Shaft or sleeve OD
+0.000 mm (+0.000 inch) API 610/682
-0.025 mm (-0.001 inch) DIN/ISO
• Bearings must be in good condition
• Maximum lateral or axial movement of shaft (end play) = 0.25 mm (0.010 inch) TIR
• Maximum shaft runout at face of seal housing = 0.05 mm (0.002 inch) TIR
• Maximum dynamic shaft deflection at seal housing = 0.05 mm (0.002 inch) TIR
Face of seal housing to be square to the
axis of the shaft to within 0.0005 mm/mm
(0.0005 inch/inch) of seal chamber bore TIR
and have a 1.6
μ
m (63
μ
inch) R finish or better
a
Gland pilot can be at either of these
register locations, concentric to within
0.125 mm (0.005 inch) of shaft or
sleeve OD TIR