3piping instructions – Flowserve High Temperature Metal Bellows Seals User Manual
Page 4
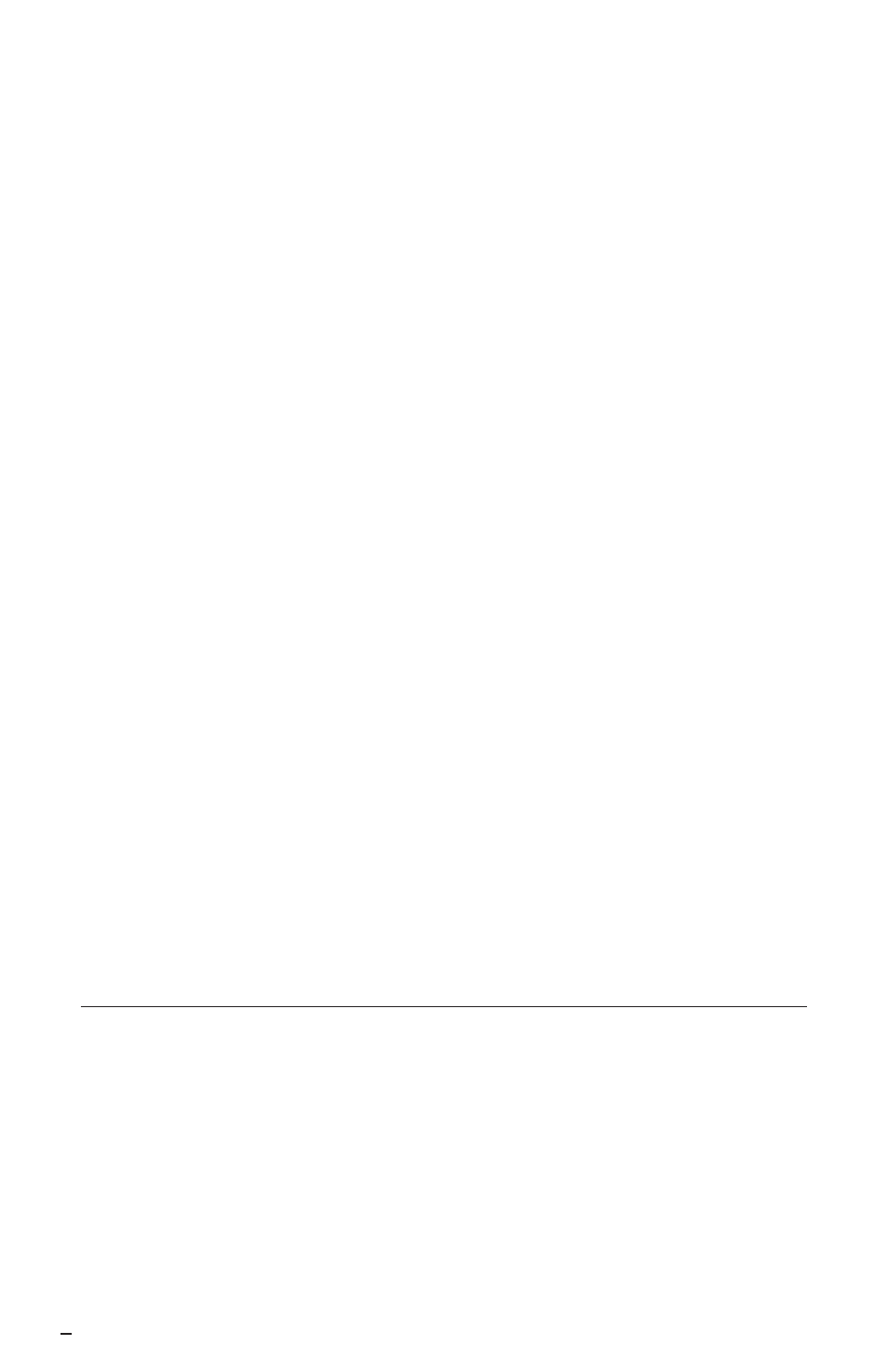
4
2.5.3 Carefully slide the cartridge assembly onto the shaft and near the
drive collar. Large size seals may require assistance to work
safely and avoid seal damage. Refer to the assembly drawing for
proper orientation and approximate axial position.
2.6 For between-bearing shaft pumps:
2.6.1 Carefully slide the cartridge assembly onto the shaft and against
the seal chamber. Large size seals may require assistance to
work safely and avoid seal damage. Refer to the assembly
drawing for proper orientation and approximate axial position.
2.6.2 Carefully slide the flexible graphite gasket along the pump shaft
and seat uniformly against the sleeve.
2.6.3 Slide the drive collar onto the shaft with the gasket side of the
collar facing the sleeve gasket. If the collar assembly includes a
key drive, pin and/or lock ring, install these items. Again, refer to
the assembly drawing. Do not lock the collar in place.
2.7 Start threading the axial drive collar bolts each a few thread turns.
The collar assembly should remain loose.
2.8 Rebuild the pump and lock the shaft in its operating position without
disturbing the seal assembly and drive collar.
2.9 Bolt the seal gland to the seal chamber. Use uniform torque on bolts to
assure contact with seal chamber face and squareness with shaft.
2.10 Tighten axial drive collar bolts evenly to compress flexible graphite gasket
to sleeve and pump shaft. Apply approximately 5.6 N-m (50 in-lbs) of
torque. A gap may remain between the drive collar and adjusting collar.
This gap should be uniform around the entire collar assembly.
2.11 Tighten drive collar set screws evenly to the shaft. Refer to the seal
assembly drawing for torque specification.
2.12 Loosen setting device attachment bolts, rotate setting devices clear of the
drive collar and re-tighten bolts.
3
Piping Instructions
Piping instructions are shown on the mechanical seal assembly drawing. These
instructions must be followed precisely to ensure correct seal operation. For aux-
iliary systems, carefully read the operating instructions provided with the system.
Establishing proper lubrication at the mechanical seals is the first step toward
reliable operation. Startup procedures and piping designs must ensure all air and
gas is vented from the pump casing, seal chamber and piping system. Do not
start the equipment dry.
Orifices should be installed as far away from the seal gland as possible. An
exception to this rule should be made for orifices fitted to drain piping. To avoid
clogging, install it at the seal gland so that conducted heat will serve to keep any
leakage in a fluid state.