Flowserve MARK 3 GROUP 4 User Manual
Page 29
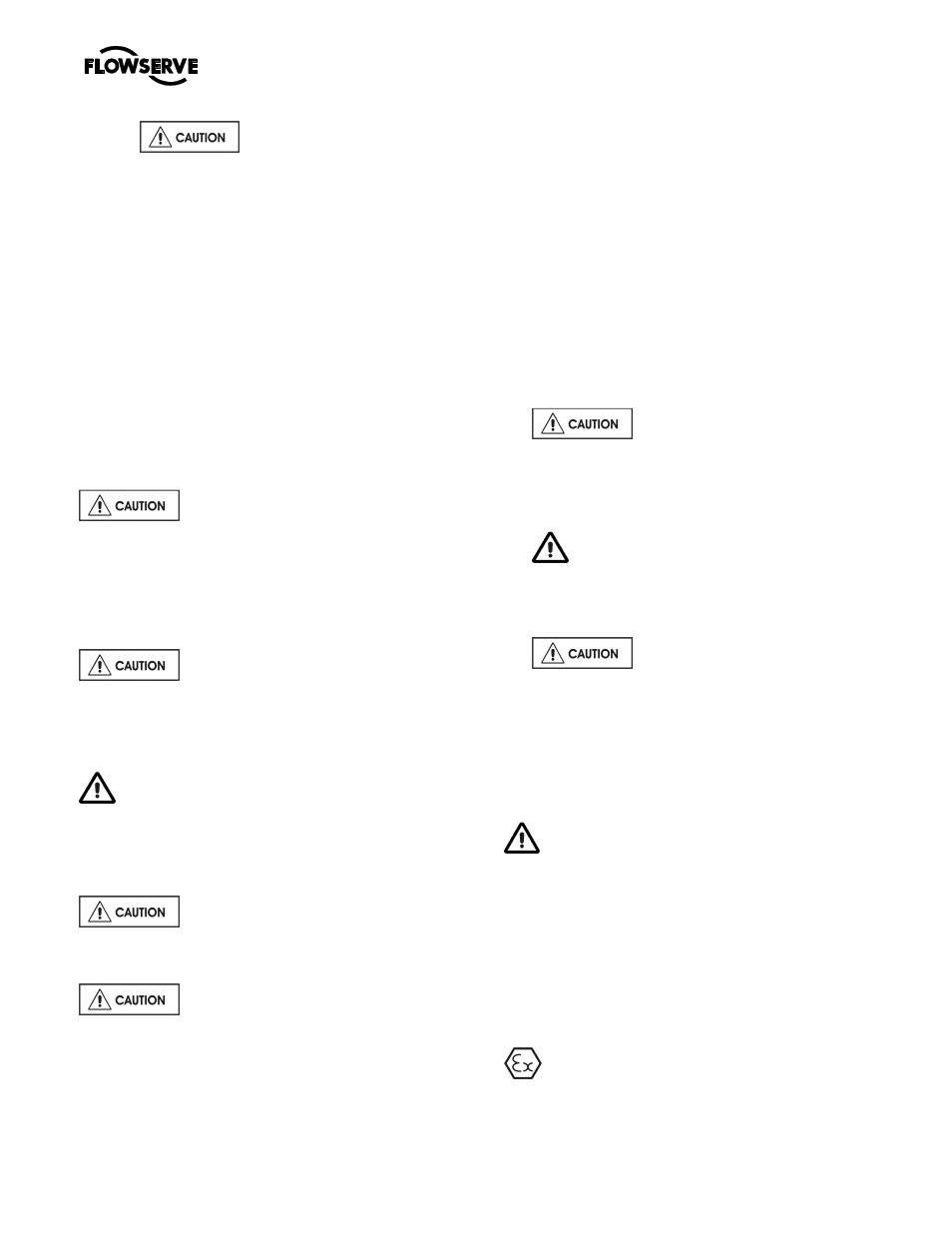
MARK 3 GROUP 4 USER INSTRUCTIONS ENGLISH 71569286 08-12
Page 29 of
48
flowserve.com
®
5.2.3
Lubrication schedule
5.2.3.1 Oil lubricated bearings
Normal oil change intervals are 4 000 operating hours
or at least every 6 months. For pumps on hot service
or in severely damp or corrosive atmosphere, the oil
will require changing more frequently. Lubricant and
bearing temperature analysis can be useful in
optimizing lubricant change intervals.
The lubricating oil should be a high quality mineral oil
having foam inhibitors. Synthetic oils may also be
used if checks show that the rubber oil seals will not
be adversely affected.
The bearing temperature may be allowed to rise to
50 ºC (90 ºF).above ambient, but should not exceed
82 ºC (180 ºF). A continuously rising temperature, or
an abrupt rise, indicate a fault.
5.3 Direction of rotation
Ensure the pump is given the same
rotation as the pump direction arrow cast on the
pump casing. Rotation is clockwise when the pump is
viewed from the driver.
To avoid dry running the pump must either be filled
with liquid or have the flexible coupling disconnected
before driver is switched on.
If maintenance work has been carried
out to the site's electricity supply, the direction of
rotation should be re-checked as above in case the
supply phasing has been altered.
5.4 Guarding
Guarding is supplied fitted to the pump set. If
this has been removed or disturbed ensure that all the
protective guards around the pump coupling and
exposed parts of the shaft are securely fixed.
5.5 Priming and auxiliary supplies
Ensure all electrical, hydraulic,
pneumatic, sealant and lubrication systems (as
applicable) are connected and operational.
Ensure the inlet pipe and pump
casing are completely full of liquid before starting
continuous duty operation.
5.5.1
Suction pressure above atmospheric
pressure
Open vent connection (6521] on top of the pump
upper casing to allow the trapped air to escape. Let
liquid run out until free from air bubbles.
5.5.2
Suction lift with foot valve fitted
Fill suction pipe and casing with liquid at a pressure
of 1 to 2 bar from an external source. Vent as
described in section 5.5.1.
5.5.3
Suction lift without foot valve
Pump casing vents on the suction volute must be
connected to an external vacuum pump priming
system. If in doubt please consult Flowserve.
5.6 Starting the pump
a)
Ensure flushing and/or cooling/
heating liquid supplies are turned ON before
starting the pump.
b) CLOSE the outlet valve.
c) OPEN all inlet valves.
d) Prime the pump.
e)
Ensure all vent connections are closed
before starting.
f) Start motor and check outlet pressure.
g) If the pressure is satisfactory, SLOWLY open
outlet control valve.
h)
Do not run the pump with the
outlet valve closed for a period longer than 10
seconds.
i) If NO pressure, or LOW pressure, STOP the
pump. Refer to section 7,
Faults; causes and
remedies
, for fault diagnosis.
5.7 Running the pump
5.7.1
Venting the pump
Vent the pump to enable all trapped air to
escape taking due care with hot or hazardous liquids.
Under normal operating conditions, after the pump
has been fully primed and vented, it should be
unnecessary to re-vent the pump.
5.7.2
Pumps fitted with packed gland
If the pump has a packed gland there must be some
leakage from the gland. Gland nuts should initially
be finger-tight only. Leakage should take place soon
after the stuffing box is pressurised.
The gland must be adjusted evenly to give
visible leakage and concentric alignment of the gland
ring [4120) to avoid excess temperature. If no