Flowserve MARK 3 GROUP 4 User Manual
Page 23
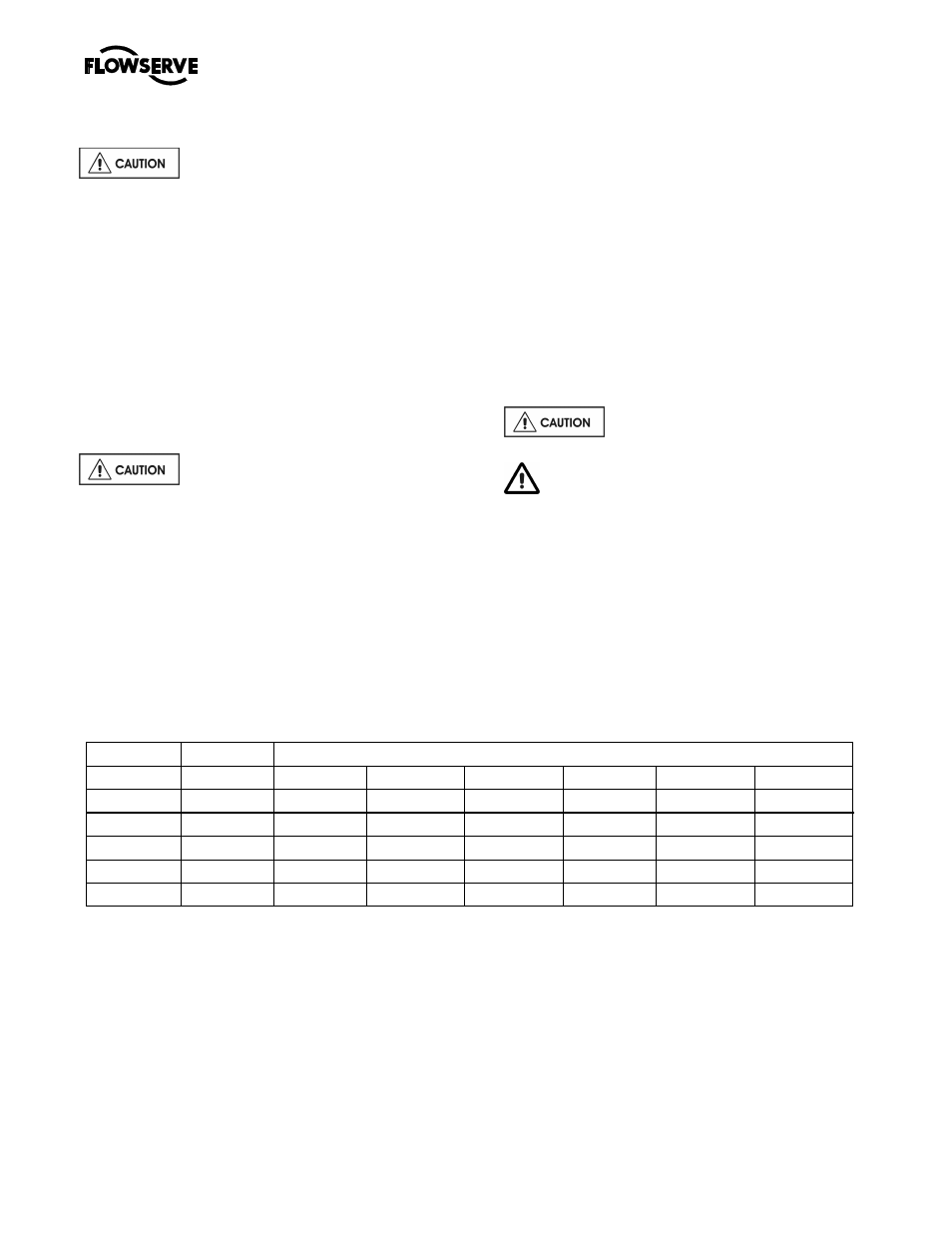
MARK 3 GROUP 4 USER INSTRUCTIONS ENGLISH 71569286 08-12
Page 23 of
48
flowserve.com
®
4.7 Piping
Protective covers are fitted to the pipe
connections to prevent foreign bodies entering during
transportation and installation. Ensure that these
covers are removed from the pump before
connecting any pipes.
4.7.1
Suction and discharge pipework
In order to minimize friction losses and hydraulic
noise in the pipework it is good practice to choose
pipework that is one or two sizes larger than the
pump suction and discharge. Typically main
pipework velocities should not exceed 2 m/s (6 ft/sec)
suction and 3 m/s (9 ft/sec) on the discharge.
Take into account the available NPSH that must be
higher than the required NPSH of the pump.
Never use the pump as a support for
piping.
Maximum forces and moments allowed on the pump
flanges vary with the pump size and type. To
minimize these forces and moments that may, if
excessive, cause misalignment, hot bearings, worn
couplings, vibration and the possible failure of the
pump casing, the following points should be strictly
followed:
•
Prevent excessive external pipe load
•
Never draw piping into place by applying force to
pump flange connections
•
Do not mount expansion joints so that their force,
due to internal pressure, acts on the pump flange
The table in 4.7.2 summarizes the maximum forces
and moments allowed on MARK 3 Group 4 pump
casings. Refer to Flowserve for other configurations.
Ensure piping and fittings are flushed
before use.
Ensure piping for hazardous liquids is arranged
to allow pump flushing before removal of the pump.
4.7.2
Maximum forces and moments allowed on MARK 3, Group 4 pump flanges
Introduction:
Flowserve Mark 3, Group 4 pumps are larger than those contained in ANSI/HI 9.6.2 and have been
designed around the FRBH process pump. API 610 has been used as a reference for these pumps to establish the
allowable forces and moments. Typically values are 2X API. The values shown in the table 4.7.2.2 are based on
pumps mounted on grouted baseplates. These values should be factored based on material of construction and
temperature. The table 4.7.2.1 has been adopted from Mark 3 manual (PCN 71569102) that uses data from
ANSI/HI 9.6.2.6.
Table 4.7.2.1: Casing Material Correction Factors
Material Group No.
1.0
2.2
2.8
3.8
3.17
Ti
Temp. °C
Temp °F
CI/DI
316/317L
CD4MCU
Hast. C
Wort h/A20
Titanium
-29
-20
0.89
1.00
1.00
1.00
0.83
0.89
38
100
0.89
1.00
1.00
1.00
0.83
0.89
93
200
0.78
0.86
1.00
1.00
0.72
0.86
150
300
0.73
0.78
0.92
1.00
0.65
0.81