Flowserve HED Worthington User Manual
Page 8
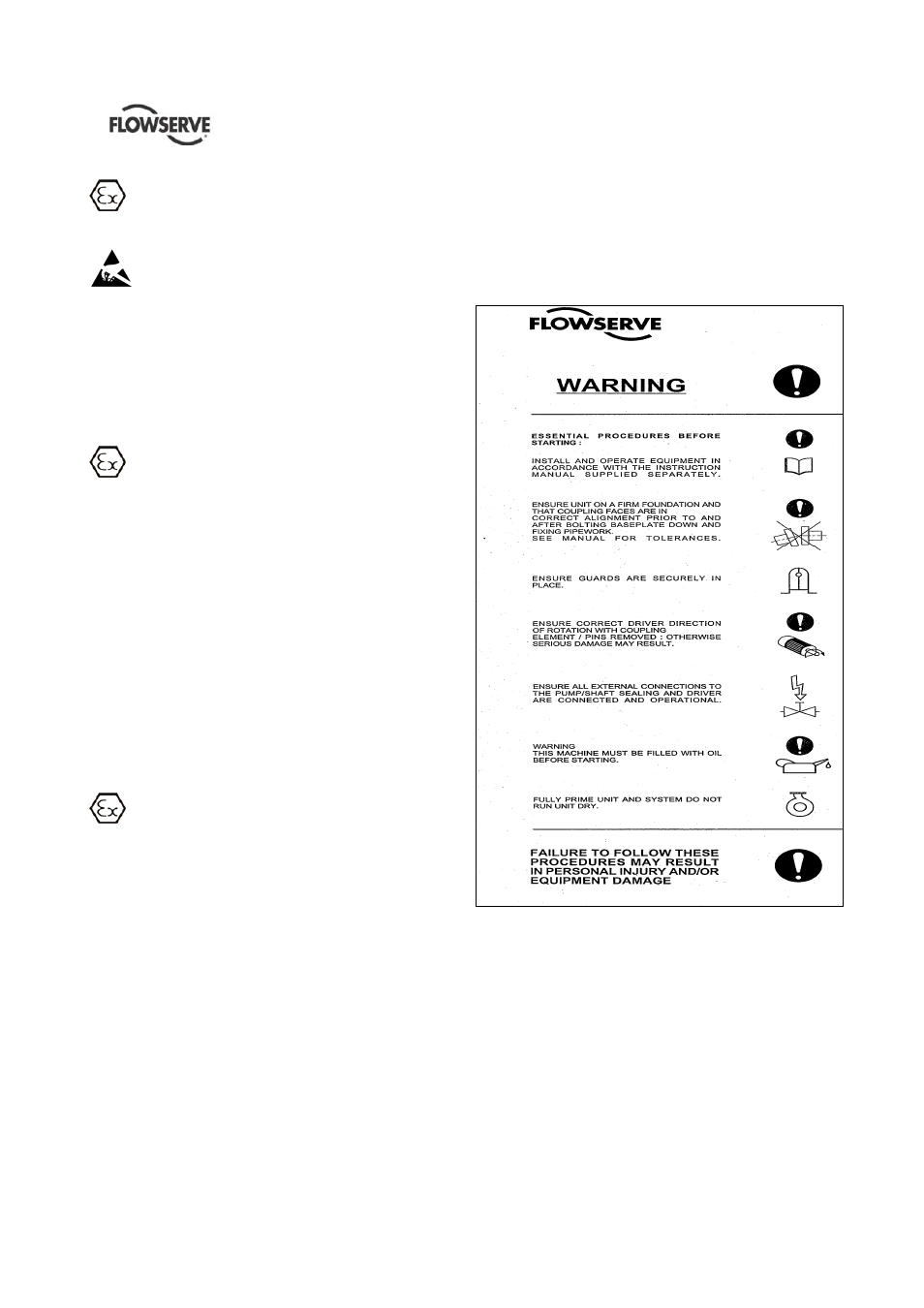
HED/HED-DS USER INSTRUCTIONS ENGLISH 85392695 – 06/14
Page 8 of 64
1.6.4.5 Preventing sparks
To prevent a potential hazard from mechanical
contact, the coupling guard must be non-sparking
and anti-static for Category 2.
To avoid the potential hazard from random
induced current generating a spark, the earth contact
on the base plate must be used.
Avoid electrostatic charge: do not rub non-metallic
surfaces with a dry cloth ensure cloth is damp.
The coupling must be selected to comply with
2006/42/EC and correct alignment must be
maintained.
1.6.4.6 Preventing leakage
The pump must only be used to handle liquids
for which it has been approved to have the correct
corrosion resistance.
Avoid entrapment of liquid in the pump and associated
piping due to closing of suction and discharge valves,
which could cause dangerous excessive pressures to
occur if there is heat input to the liquid. This can occur if
the pump is stationary or running.
Bursting of liquid containing parts due to freezing
must be avoided by draining or protecting the pump
and ancillary systems.
Where there is the potential hazard of a loss of a seal
barrier fluid or external flush, the fluid must be
monitored.
If leakage of liquid to atmosphere can result in a
hazard, the installation of a liquid detection device is
recommended.
1.6.4.7 Maintenance to avoid the hazard
CORRECT MAINTENANCE IS REQUIRED TO
AVOID POTENTIAL HAZARDS WHICH GIVE A
RISK OF EXPLOSION
The responsibility for compliance with maintenance
instructions is with the plant operator.
To avoid potential explosion hazards during
maintenance, the tools, cleaning and painting
materials used must not give rise to sparking or
adversely affect the ambient conditions. Where there
is a risk from such tools or materials; maintenance
must be conducted in a safe area.
It is recommended that a maintenance plan and
schedule is adopted. (See section 6, Maintenance.)
1.7 Nameplate and safety labels
1.7.1 Nameplate
For details of nameplate, see the Declaration of
Conformity, or separate documentation included with
these User Instructions.
1.7.2 Safety labels
1.8 Specific machine performance
For performance parameters see section 1.5, Duty
conditions. Pump performance data are summarised
on pump data sheet which is included in proper
section of “Job User’s Instruction”.
1.9 Noise level
When pump noise level exceeds 85 dBA attention
must be given to prevailing Health and Safety
Legislation, to limit the exposure of plant operating
personnel to the noise. The usual approach is to
control exposure time to the noise or to enclose the