Flowserve Twin Screw Rotary User Manual
Page 32
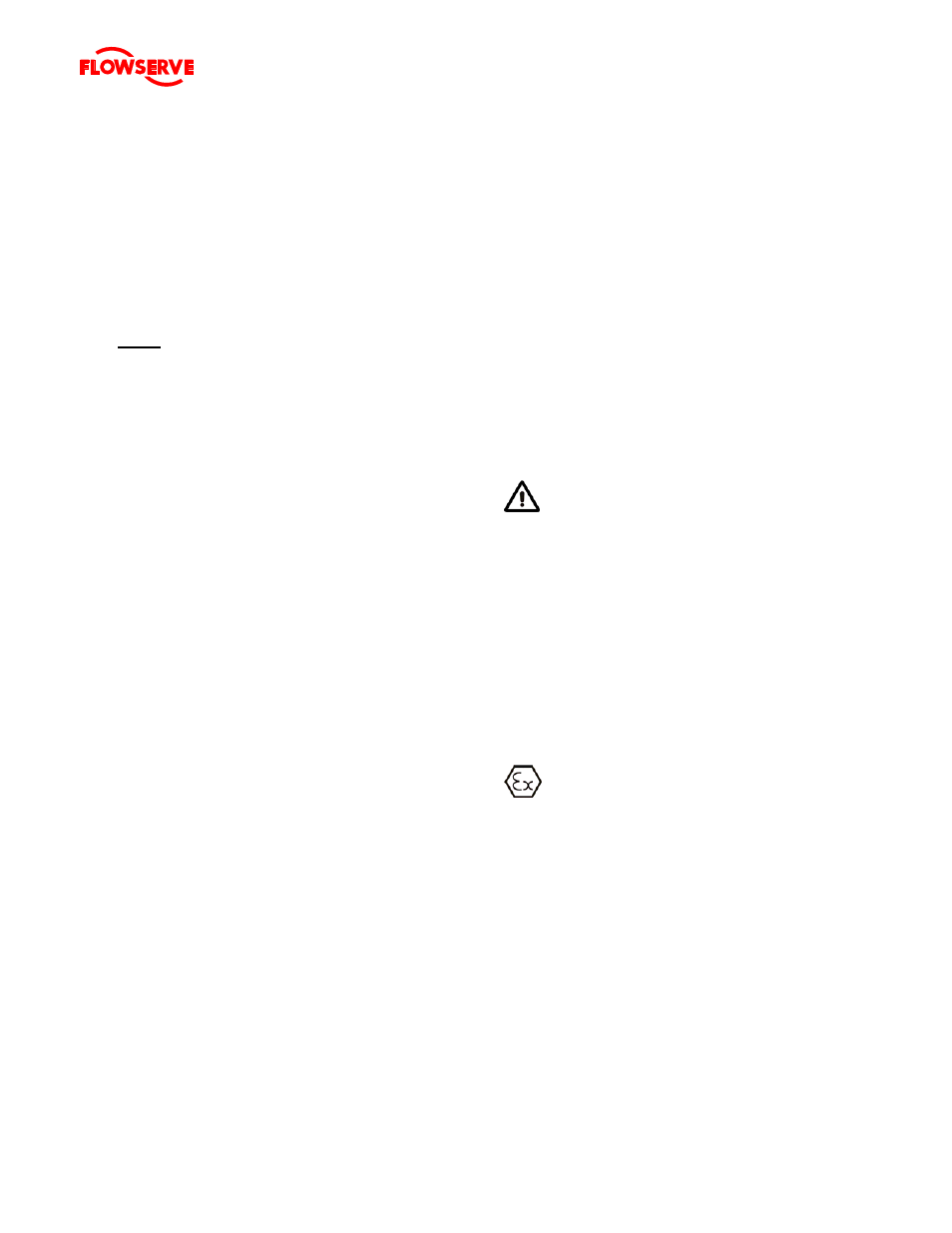
TWIN SCREW PUMPS. ORIGINAL USER INSTRUCTIONS. ENGLISH. 71569243 – 07/10
Page 29 of 53
®
h) If NO pressure, or LOW pressure, STOP the
pump. Refer to section 7 FAULTS; CAUSES
AND REMEDIES, for fault diagnosis.
5.7 High Temperature Startup
Internal bearing screw or gear pumps, whether fitted
with standard ball and roller bearings or carbide
sleeve bearings and thrust collars, are very sensitive
to proper startup techniques. It is absolutely essential
that the entire pump, including any product
recirculation piping, has had time to achieve stability
at the required operating temperature prior to startup.
If the entire pump is not stable at the required
operating temperature there may be slugs of partially
solidified product in the bearings or housings which
will prevent proper circulation of product through the
bearings or damage the bearings. The same
precaution is also true of the recirculation piping. As
well, if the pump has not achieved a uniform
temperature, distortions in the housings or body may
cause mechanical problems during startup or
operation. It is also imperative that the pump and
recirculation piping be completely covered with
securely fastened insulation.
In addition to the standard startup procedures
outlined the following steps should be followed in
high temperature applications.
1) An empty pump should first be filled with product
at ambient temperature to avoid thermal shock.
This is particularly applicable to pumps with
carbide bearings. The pump should never be
started empty or cold.
2) Steam or a heat transfer liquid should be
circulated through the housing and body jackets
as well as the recirculation piping jackets. The
heating medium should be at the operating
temperature and circulated at a rate which will
produce a maximum temperature rise of
approximately 150 degF per hour. A four hour
heat soak period prior to startup is
recommended.
3) An appropriate flow of the heat transfer medium
is required during operation to ensure the pump
is maintained at the operating temperature.
5.8 Post start-up
Once the unit has operated satisfactorily for several
days record as much information about these normal
operating conditions as possible. This data may be
helpful in identifying and correcting changes in future
performance before serious problems occur.
Typical data to be recorded is: serial number of pump
and driver, suction pressure, discharge pressure,
specific gravity, capacity, pump speed, amperage
and voltage (each phase), seal liquid pressure,
ambient temperature and pumping temperature.
After the unit has been running continuously about
one week, the coupling halves of direct driven units
should be given a final check for misalignment
caused by pipe strains or temperature strains. If the
alignment is correct, both the pump and driver should
be dowelled to the baseplate. The pump should be
dowelled with one dowel in each support foot. Refer
to the manufacturer’s manual for driver dowelling
instructions.
5.9 Running the pump
5.9.1 Venting the pump
Vent the pump to enable all trapped air to
escape taking due care with hot or hazardous liquids.
The pump can be vented by opening the plugs in the
suction chamber.
Under normal operating conditions, after the pump
has been fully primed and vented, it should be
unnecessary to re-vent the pump.
5.9.2 Pumps fitted with packed gland
If the pump has a packed gland there must be some
leakage from the gland. Gland nuts should initially
be finger-tight only. Leakage should take place soon
after the stuffing box is pressurised.
The gland must be adjusted evenly to give
visible leakage and concentric alignment of the gland
ring to avoid excess temperature. If no leakage
takes place the packing will begin to overheat. If
overheating takes place the pump should be stopped
and allowed to cool before being re-started. When
the pump is re-started, check to ensure leakage is
taking place at the packed gland.
If hot liquids are being pumped it may be necessary
to slacken the gland nuts to achieve leakage.
The pump should be run for 30 minutes with steady
leakage and the gland nuts tightened by 10 degrees
at a time until leakage is reduced to an acceptable
level, normally a minimum of 120 drops per minute is
required. Bedding in of the packing may take
another 30 minutes.