Flowserve Twin Screw Rotary User Manual
Page 12
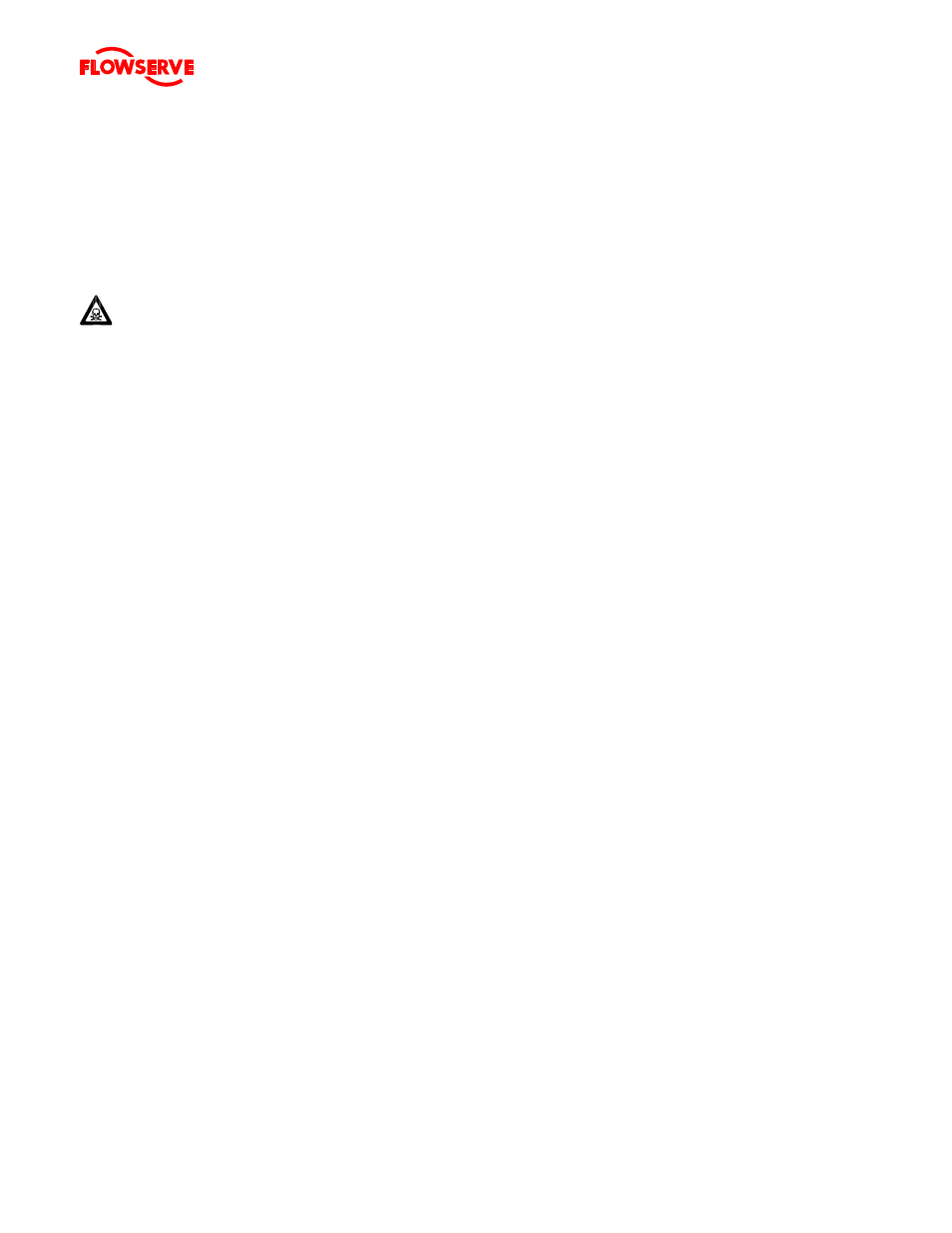
TWIN SCREW PUMPS. ORIGINAL USER INSTRUCTIONS. ENGLISH. 71569243 – 07/10
Page 9 of 53
®
2.5 Recycling and end of product life
At the end of the service life of the product or its parts,
the relevant materials and parts should be recycled or
disposed of using an environmentally acceptable
method and in accordance with local regulations. If the
product contains substances that are harmful to the
environment, these should be removed and disposed of
in accordance with current local regulations. This also
includes the liquids and/or gases that may be used in
the "seal system" or other utilities.
Make sure that hazardous substances are
disposed of safely and that the correct personal
protective equipment is used. The safety specifications
must be in accordance with the current local
regulations at all times.
3 PUMP DESCRIPTION
3.1 Configurations
Flowserve Twin Screw Pumps are single stage,
positive displacement pumps especially designed for
the petroleum industries in the transfer of oils and other
liquids of varying viscosities. The flow of liquid through
the pump is accomplished by the progressive
movement of sealed cavities formed by the
intermeshing of matched pumping screws (one right
hand, one left hand) rotating in the precision ground
bores of the pump body. To balance the hydraulic
thrust created by the pumping action, two sets of
meshed screws are used, moving the liquid from both
ends of the body to the discharge port located at the
center of the body.
The key assembly of the screw pump is the rotating
element. Each rotating element consists of a drive
shaft and a driven shaft running on parallel axes at a
fixed center distance. Each shaft holds bearings, one
timing gear and two opposing pumping screws plus the
assorted hardware (locknuts, spacers) required for
mounting. On the pinned designs, the pumping screws
are mounted on the shafts and held in place by peened
taper pins. On the integral designs, the pumping
screws and the shaft are an integral piece machined
from a single steel bar. Precise clearances are
maintained between meshing screws to limit the
internal leakage (slip) in the pump. The timing gears
maintain these clearances, prevent contact between
the pumping screws and turn the driven shaft. Heavy
duty roller bearings eliminate radial contact between
the pumping screws and the body bores and support
the loading on the shafts produced by the pumping
action. Double row ball bearings position the shafts
axially and prevent contact between the flanks (sides)
of the meshing screws. Lubrication of the bearings is
provided by the liquid being pumped on Internal Pumps
and by oil contained in housings (sumps) on External
Pumps.
The bearing configurations of both Internal and
External Pumps provide a rear pull-out feature which
permits the quick removal of the entire rotating element
without disturbing the pump body or the drive. (Refer
to Section VIII). The use of a spacer type coupling
between the pump and driver is necessary to apply this
feature.
Standard shaft sealing is provided by packing which is
factory installed with the gland requiring only minor
adjustment prior to pump start-up. Mechanical seals
are optional equipment and when provided require no
adjustment prior to or during pump operation.
All pumps are shop performance tested to ensure
mechanical reliability and compliance with the specified
conditions of service. They are carefully inspected and
prepared for shipment. All exterior machined surfaces
are coated with rust preventative and all openings are
provided with covers or plugs.
3.2 Name structure
The pump size will be engraved on the nameplate. The
following example explains how the pump name
identifies the construction features and options.
NJHP
The first two letters indicate the “nominal pump size”
while the last two are an indication of the pump
configuration, in this case an external bearing pump
with integral shafts.
3.3 Design of major parts
3.3.1 Pump casing
The pump casing is a casting with side suction and top
discharge connections, although other configurations
are available. Refer to the General Arrangement
drawing for further details It is a one piece pressure
retaining casting with gasket connections to the seal
housings and the suction and discharge flanges.