2 lubricants – Flowserve MP1 Sier-Bath User Manual
Page 21
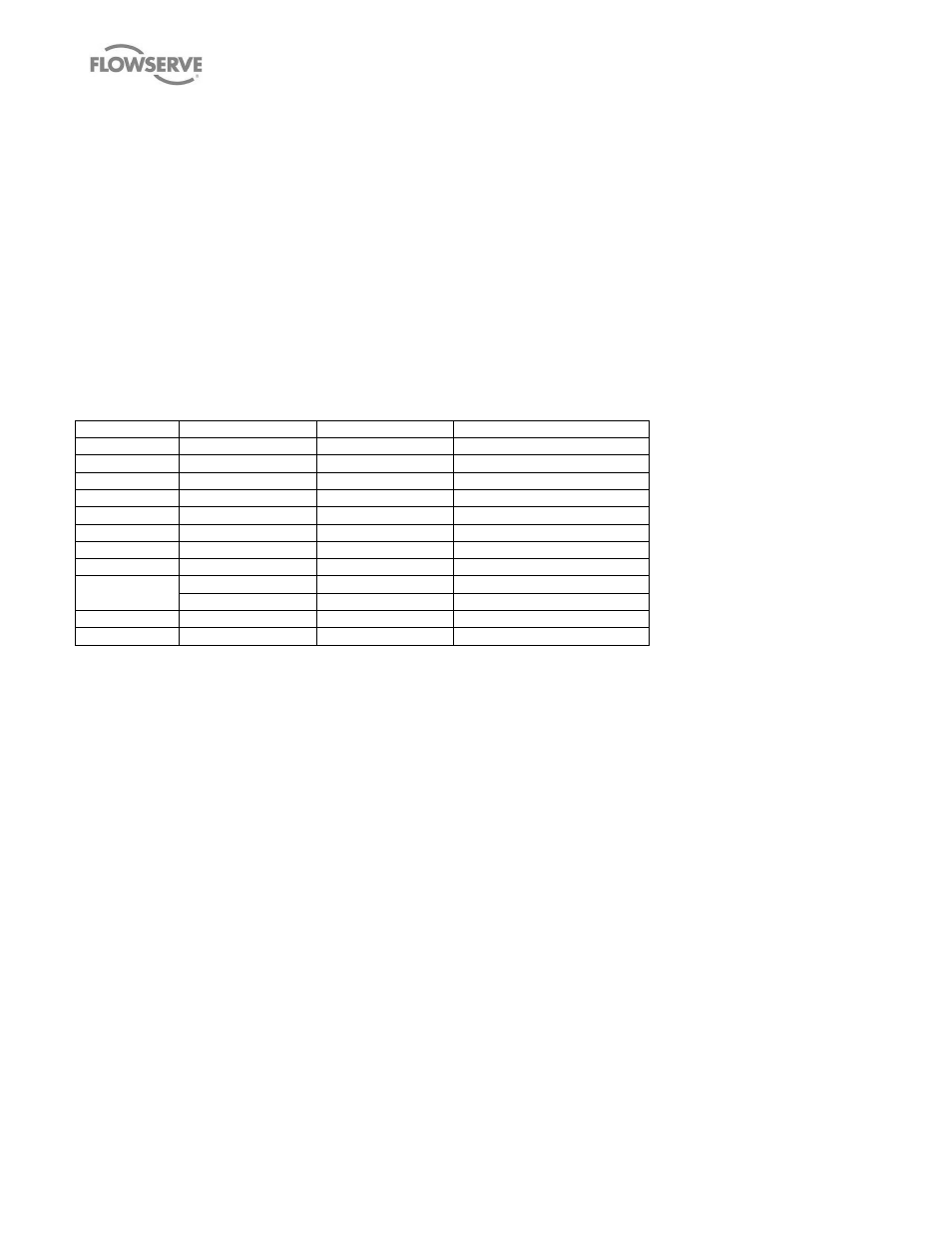
MP1 USER INSTRUCTIONS ENGLISH 26999958
– 10-12
Page 21 of 48
flowserve.com
or
constant level oiler bottle or the level mentioned on
sectional drawing.
When fitted with a constant level oiler, the bearing
housing should be filled by unscrewing or hinging back
the transparent bottle and filling the bottle with oil.
Where an adjustable body Trico oiler is fitted this
should be set to the proper height.
The oil filled bottle should then be refitted so as to
return it to the upright position. Filling should be
repeated until oil remains visible within the bottle.
Other drivers and gearboxes, if appropriate, should be
lubricated in accordance with their manuals.
In case of separate shaft mounted lube oil circulating
pump, refer to general arrangement drawing for
instructions
5.2 Lubricants
5.2.1 Typical oils
Table 4
– Typical lubricating oils
Company
Column “A”
Column “B”
Column “C”
Mobil
Mobil DTE Oil BB
MOBILGEAR 626
Mobil DTE Oil HH
Shell
OMALA Oil 220
OMALA Oil 68
OMALA Oil 460
Sunoco
SUNVIS 790 (220)
SUNVIS 747 (46)
SUNVIS 7150
Amoco
RYKON Oil No. 220
AMOGEAR No. 68
American Industrial Oil No. 460
Texaco
REGAL R&O 220
MEROPA 150
REGAL R&O 460
Arco
PENNANT NL 220
PENNANT NL 68
RUBILENE 460
Chevron
AW Machine Oil 220
EP Industrial Oil 46x
NL Gear Compound 460
Exxon
TERESSTIC N220
SPARTAN EP 68
TERESSTIC 460
*Esso
TERESSO N220
SPARTAN EP 68
CYLESSO TK 460
TERESSO 100
-
-
BP
ENERGOL HL 100
-
-
Petro Canada
GIREX 220
GIREX 68
GIREX 320
*Imperial Oil Limited (Canada)
5.2.2 Lubrication schedule
5.2.2.1 Requirements for oil lubricated bearings
Normal oil change intervals are 2500 operating hours or
at least every 6 months whichever occurs first,
depending on the temperature of the service, the
service conditions, and quality of the lubricant regarding
oxidation stability capability. For pumps on hot service
or in severely damp or corrosive atmosphere, the oil will
require changing more frequently. Lubricant analysis
(change in appearance, odour, viscosity, oxidation,
water/contaminants concentration, etc.), as well as
bearing temperature analysis, can be useful in
optimizing lubricant change intervals.
The lubricating oil should be a high quality mineral oil
having foam inhibitors. Synthetic oils may also be used
if checks show that the rubber oil seals will not be
adversely affected.
The bearing temperature may be allowed to rise to
50 ºC (90 ºF) above ambient, but should not exceed
82 ºC (180 ºF). An abrupt or continuously rising
temperature may be indicating a fault.
Oils used in the bearing housing should meet the
following requirements:
1. Oxidation Stability Specification per AGMA
Standard 250.04 table 1, page 9.
2. Foam Suppression Specification per AGMA
Standard 250.04 table 1, page 9.
At initial start-up, oil must be drained completely and
replaced after one week or 100 hours running time
(except for temperatures above 121
C (250
F)), or
even earlier, after 50 hours running time.
An analysis of the expected operating temperatures
should be conducted to determine the proper oil that
should be used in the pump. It should be noted in the
case of a large swing in ambient temperatures, it may
require different types of oils are used for summer and
winter. Unless otherwise noted by Flowserve
engineering, the following information should be used
to determine the proper oil to use in the pump and
whether more than one type of oil may be required
during yearly operation.