Flowserve MJ Slurry User Manual
Page 23
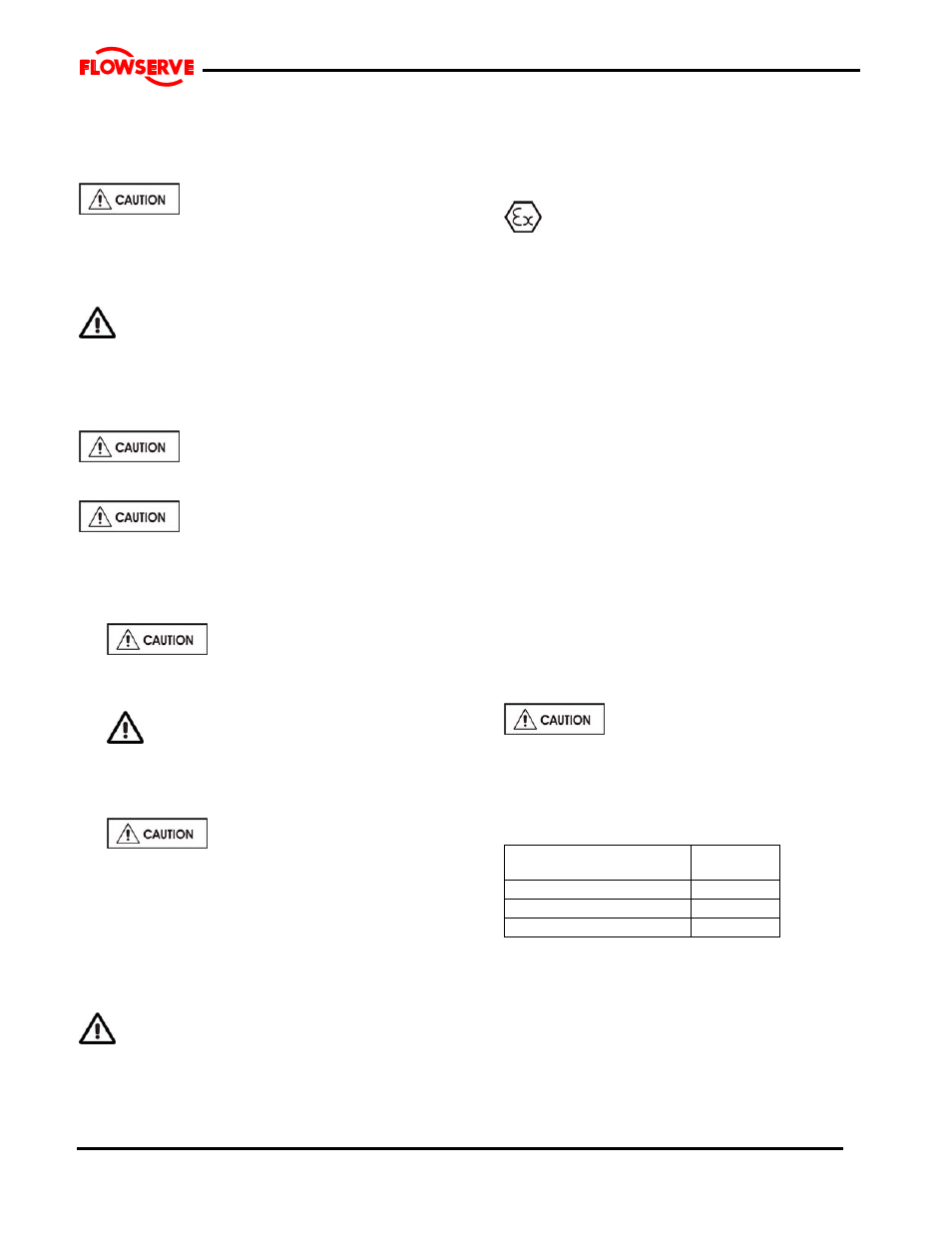
MJ SLURRY USER INSTRUCTIONS ENGLISH 71569294 - 02/08
Page 23 of 42
®
Minimum submergence is recommended to avoid
vortexing and entrainment of air. Vortexing will result
in increased vibration, loss of performance and
reduced bearing lives.
If maintenance work has been carried
out to the site's electricity supply, the direction of
rotation should be re-checked as above in case the
supply phasing has been altered.
5.4 Guarding
Guarding is supplied fitted to the pump set. If
this has been removed or disturbed ensure that all the
protective guards around the pump coupling and
exposed parts of the shaft are securely fixed.
5.5 Priming and auxiliary supplies
Ensure all electrical, hydraulic,
pneumatic, sealant and lubrication systems (as
applicable) are connected and operational.
Ensure the inlet pipe and pump
casing are completely full of liquid before starting
continuous duty operation. Pump fluid must be above
the pump casing.
5.6 Starting the pump
a)
Ensure flushing and/or cooling
liquid supplies are turned ON before starting the
pump.
b) CLOSE the outlet valve.
c)
Ensure all vent connections are closed
before starting.
d) Start motor and check outlet pressure.
e) If the pressure is satisfactory, slowly OPEN outlet
control valve.
f)
Do not run the pump with the
outlet valve closed for a period longer than 60
seconds.
g) If NO pressure, or LOW pressure, STOP the
pump. Refer to section 7, Faults; causes and
remedies
, for fault diagnosis.
5.7 Running the pump
5.7.1 Venting the pump
Vent the pump to enable all trapped air to
escape taking due care with hot or hazardous liquids.
Under normal operating conditions, after the pump
has been fully primed and vented, it should be
unnecessary to re-vent the pump.
5.7.4 Bearings
If the pumps are working in a potentially
explosive atmosphere temperature or vibration
monitoring at the bearings is recommended
If bearing temperatures are to be monitored it is
essential that a benchmark temperature is recorded
at the commissioning stage and after the bearing
temperature has stabilized. Record the bearing
temperature (t) and the ambient temperature (ta).
Estimate the likely maximum ambient temperature
(tb). Set the alarm at (t+tb-ta+5)
°C [(t+tb-ta+10)°F]
and the trip 105
°C (220 °F) for grease lubrication.
It is important, particularly with grease lubrication, to
keep a check on bearing temperatures. After start up
the temperature rise should be gradual, reaching a
maximum after approximately 1.5 to 2 hours. This
temperature rise should then remain constant or
marginally reduce with time. Refer to section 6.2.3.1
for further information.
5.7.5 Normal vibration levels, alarm and trip
For guidance, pumps generally fall under a
classification for rigid support machines within the
International rotating machinery standards and the
recommended maximum levels below are based on
those standards.
Alarm and trip values for installed
pumps should be based on the actual measurements
(N) taken on the pump in the fully commissioned as
new condition. Measuring vibration at regular
intervals will then show any deterioration in pump or
system operating conditions.
Vibration velocity – unfiltered
mm/s (in./s) r.m.s.
MJ
Normal N
≤ 7.1 (0.28)
Alarm N x 1.25
≤ 9.0 (0.35)
Shutdown trip N x 2.0
≤ 14.2 (0.56)
5.7.6 Stop/start frequency
Pump sets are normally suitable for the number of
equally spaced stop/starts per hour shown in the
table below. Check actual capability of the driver and
control/starting system before commissioning.