General electricial information, Terminals, studs, lugs and connectors – Floscan Pre-Installation Manual for Diesel Models User Manual
Page 9
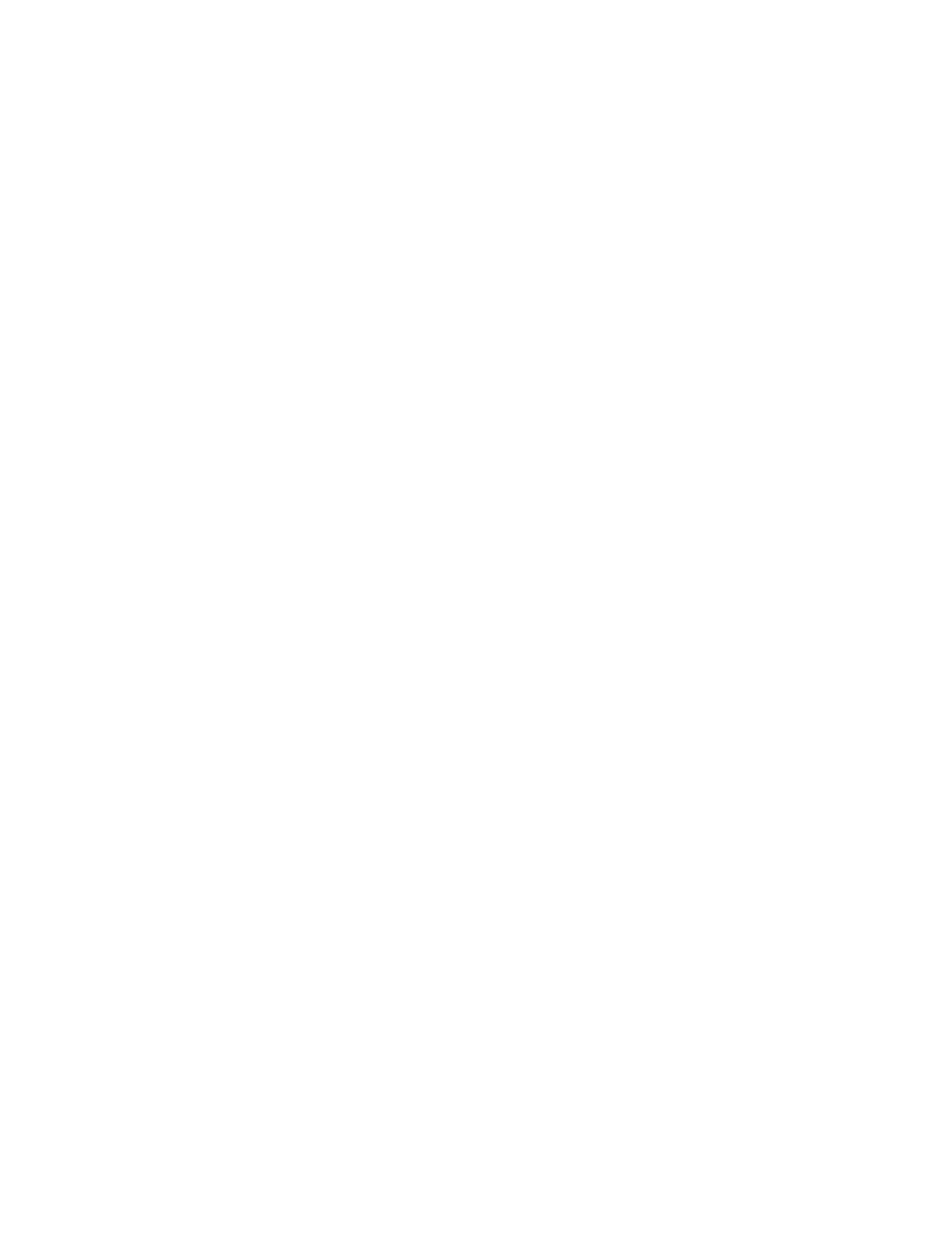
9
9
GENERAL ELECTRICIAL INFORMATION
Wiring
Good wiring practice is vital for achieving a trouble free installation. If you do this part of the job right you will
automatically eliminate many nuisance problems. The principles of good wiring are simple. Always use fuses or circuit
breakers with ampere ratings of 30 to 50% greater than the maximum load they are intended to carry. Fuses should be in
series with the hot-wire only, (Never fuse the grounded side). Fuses should be mounted as close to the power source and in as
dry a place as possible. This will protect the greatest amount of wire from short circuits. Light grease applied to fuse clips
will save them from corrosion.
Always use stranded copper wire conductors of the proper diameter, (AWG) for the installations electrical load & conductor
length. Conductors should be run in sheathed pairs, (Duplex) or in sheathed multi-conductor cables. Good wiring practice and
forthcoming USCG regulations dictate a minimum wire diameter on DC circuits of 16 AWG. 18 AWG may be used in
sheathed pairs and in multi-conductor cables. FloScan Instruments require 18 AWG shielded conductors for wire runs up to
50 feet and 16 AWG shielded conductors for runs over 50 feet.
Conductors should be run in a wire way or along parallel boards for support. Wire runs should be made along the hull side or
in the compartments overhead. It is poor practice to run conductors in the vessels’ bilge. If conductors must be run in the
bilge or in wet locations, all wiring and connections must be watertight. Conductors should be secured or clamped every 18
inches by one of the following methods:
1. Non-metallic clamps sized to hold the conductors firmly in place.
Non-metallic straps or clamps shouldn’t be used over engines, moving shafts, and machinery, or in passageways if failure
would result in a hazardous condition. The material must be resistant to oil gasoline and water and must not break or crack
within a temperature range of -30 to +250 degrees.
2. Metal straps or clamps with smooth, rounded edges, sized to hold the conductors firmly in place without damage to
conductor or insulation.
The section of conductor or cable directly under the strap or clamp shall be protected by means of loom, tape or other suitable
wrapping to prevent injury to the conductor. In machinery spaces, metal clamps should be lined with a material resistant to
the effects of oil, gasoline and water. Terminals, Studs, Lugs and Connectors.
Terminals, Studs, Lugs and Connectors
Metals used for terminal studs, nuts, and washers shall be corrosion resistant and galvanically compatible with the conductor
and terminal lug. Aluminum and unplated steel shall not be used for studs, nuts and washers. Terminal connectors shall be of
the Ring or Captive Spade type. Wire connectors shall be of the Butt type. Friction type Snap, Bullet and Blade connectors
may only be used if
the voltage drop from terminal to terminal does not exceed 50 millivolts for a 20 amp current flow. The connection must be
able to withstand a 6-pound tensile force exerted axially, for one minute.
• Twist on connectors, i.e., wire nuts must never be used.
Soldering
Proper soldering technique is vital to good wiring. Use 63% Tin, 37% Lead, rosin core electrical solder. It has the lowest
melting temperature and is the easiest to use. Don’t use acid core plumbing solder or an acid based flux. Use only enough
heat to make the solder flow freely into the crevices of the work. Use no more heat than this because excessive heat melts
plastic insulation and will travel through the wire, causing semi-conductor damage in FloScan’s Instruments and Sensors.