Floscan Pre-Installation Manual for Diesel Models User Manual
Page 10
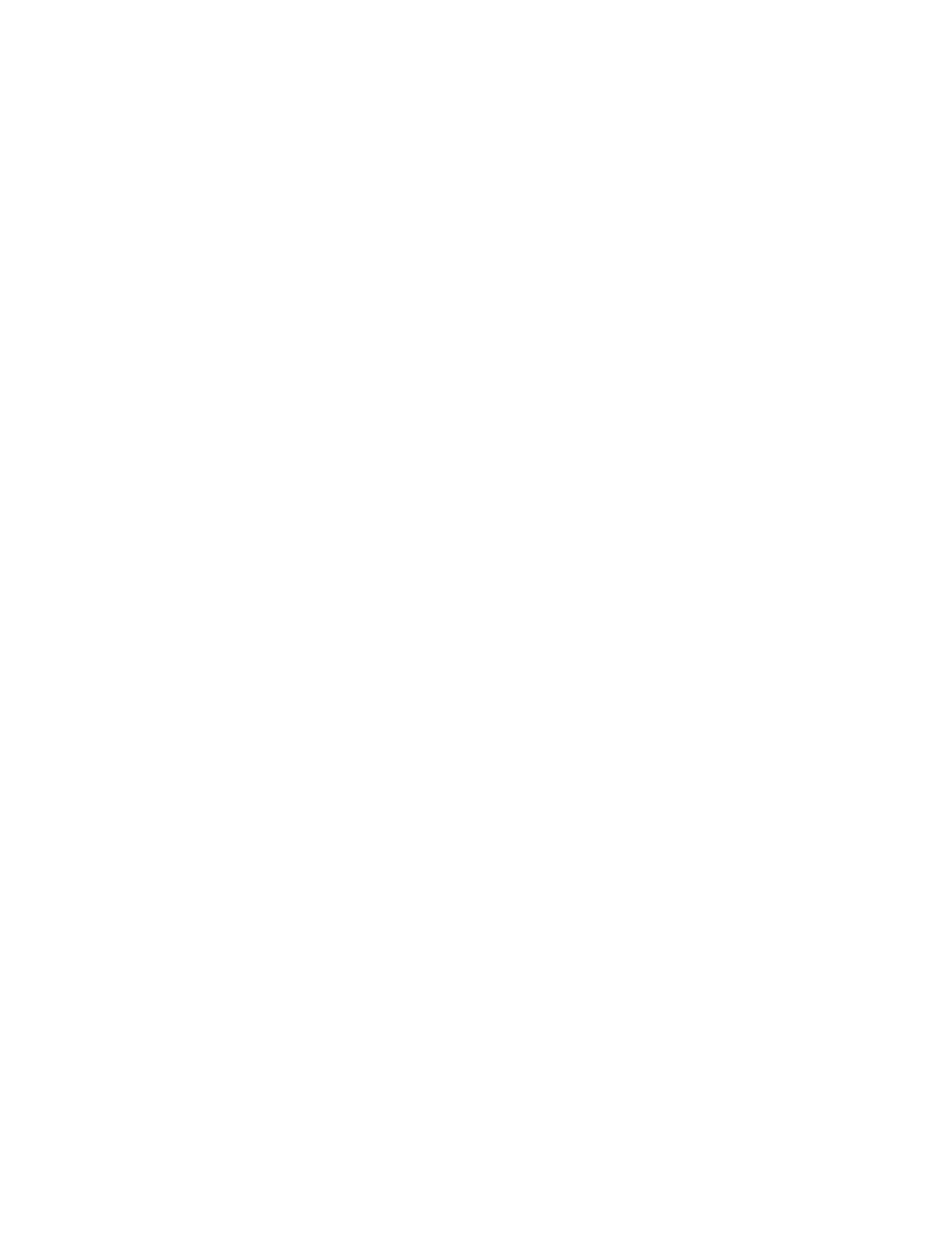
10
10
Many sins are committed in the areas of splicing, terminating and soldering. It’s generally considered poor practice to use
self insulating crimp on connectors in marine applications. Unfortunately, businesses use them almost universally because of
the higher labor costs associated with soldering.
Solder Connectors
Using only top quality, sleeveless, marine grade lugs and connectors. Strip the conductors’ insulation so that the uninsulated
conductor extends about 1/8th of an inch beyond the connector. With a crimping tool correctly sized for the wire gauge,
crimp the connector onto the conductor. If properly crimped the connectors’ mechanical connection on 18 AWG wire should
be able to withstand a tensile pull of 10 pounds. 16 AWG wire should withstand a 15-pound pull. Put your clean and properly
tinned soldering iron tip onto the connector. Heat the connector only enough to melt the solder. After soldering, while the
connector is still hot, wrap 1½ to 2 turns of electrical tape around the connector end and wire insulation, or place and shrink a
piece of Marine Grade Adhesive Heat Shrink Tubing around the connection. The tape or tubing relieves stress at the point
where the connector is crimped and soldered onto the conductor. Soldering the connector and sealing it with adhesive heat
shrink tubing creates an effective watertight barrier that prevents moisture and salt from wicking its way up the wire.
Waterproof Heat Shrink Connectors
Molex-ETC manufactures a complete line of “Perma-Seal” connectors, and Anchor Marine Grade Products manufactures
waterproof ring terminals and butt connectors for use on 10 to 22 AWG wire. The insulators on these connectors are adhesive
lined heat shrinkable nylon tubing. When the connectors are properly crimped onto a conductor and their insulator heat
shrunk, a strong watertight connection is formed. These connectors though costly, are easier to install, watertight, and meet
all requirements for strength and stress relief.
Junction Boxes
All wiring connections with the exception of connections made at the Flow Sensors, some Meter Heads, Instruments, AC
Signal Generators, Alternators, Magnetic Sensors, and Engine Instrument Senders, shall be connected inside a Junction Box,
using Terminal Blocks.
Electro Magnetic Interference-Noise
Every piece of electronic equipment and every electrically operated device produce electrical vibrations or static. The list of
electric noisemakers is endless, and include; relays, regulators, motors, tachometers, engine gauges, vessel rigging, drive
belts, antennas, shafts turning in bearings, meshing gear teeth, fluorescent lights, depth finders, radar, radios, etc. Bottling this
plethora of noise at the source isn’t practical, and usually isn’t done. Instead, noise sensitive equipment like FloScan
Instruments must be shielded and properly grounded during installation.
Static is produced whenever electrons are boiled into the atmosphere from an offending piece of equipment. The only thing
these electrons want is to get to Earth. To facilitate their journey we must create an, “Electron Superhighway” between our
instruments and Mother Earth. This is accomplished through bonding, shielding, and grounding.
Ground Plates
Ground Plates, Engine Beds and Winch Foundations serve a common purpose, they control vibrations. Beds and foundations
control mechanical vibrations, ground plates control electrical vibrations. They provide an anchoring point for electrical
equipment and an interface with Earth. Today’s modern pleasure craft seldom have external, or even internal ground plates.
There are several reasons for this, the primary consideration being economic.
Fiberglass and wood hulls lacking ground plates present definite challenges to the technician trying to eliminate electrical
noise. If the vessel doesn’t have a ground plate, an effective ground must be created through, “Bonding”.