Floscan Pre-Installation Manual for Diesel Models User Manual
Page 5
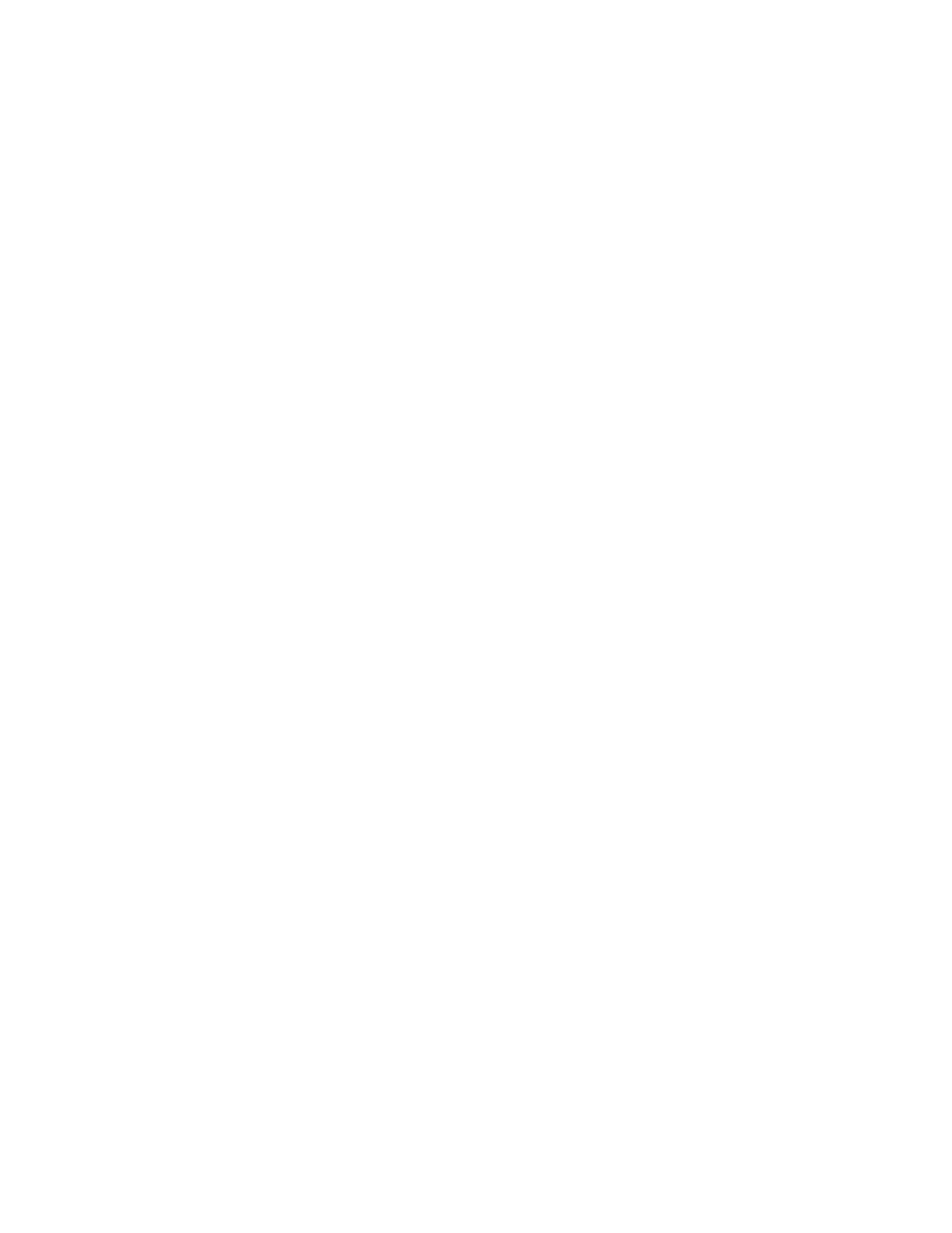
5
5
Sealing Tapered Thread
Many sealants are available for sealing pipe threads. A Fuel Proof, Thread Sealant-Lubricant must be used when installing
pipe thread fittings into FloScan’s Zinc and die-cast Aluminum Fuel Flow Sensors, and Pulsation Dampers. Use caution
when tightening pipe thread fittings as the lubricant all but eliminates, “Mechanics feel”. Over tightening can crack or distort
sensors and pulsation damper castings.
TFE-fluorocarbon, (Teflon) tape must never be used with FloScan system components for the following reasons:
• Teflon only lubricates. It won’t seal any machining imperfections.
• Threads cut into brittle materials such as zinc and aluminum lack, “Spring-back” a property found in ductile materials
like brass and low carbon steel. Spring-back increases the sealing efficiency of pipe threads. Its absence requires that an
actual thread sealant be used.
• Teflon is solid and won’t compress. As the fitting is turned, the Teflon shreds, and is extruded from the threads. These
shreds are capable of jamming the sensor turbine and will cause it to fail.
• Solid Teflon adds to the wedge effect when tightening a fitting, making it easier to crack the sensor or damper casting.
Flexible Fuel Hose
Vertical and horizontal fuel lines must be adequately supported, and securely clamped to those supports.
Diesel fuel system components installed after 31 July 1999 must meet the following standards:
• Flexible hose shall comply with the requirements of UL 1114, Marine (USCG Type A) Flexible Fuel-Line Hose, or SAE
J1527, Marine Fuel Hoses.
• SAE J1527 does not pertain to totally metallic flexible hose.
• Hose capable of passing the 2 ½ minute fire test shall be marked, USCG Type A1 or Type A2.
• Flexible hose shall be equipped with permanently installed end fittings such as swaged sleeve or a sleeve and threaded
insert, or may be secured with corrosion resistant metallic clamps.
• Clips or straps used for securing fuel lines shall be of corrosion resistant materials and of a design that eliminates the
cutting or abrading action where it contacts the fuel line.
Diesel Fuel Systems-Plumbing
Diesel engines usually have two fuel pumps. The, “Lift or Transfer” pump delivers fuel to the, “Injection” pump, and the
injection pump sends it to the injectors. Fuel not used in combustion is returned to tank through the return line. There are 4
types of lift pumps in general use, (Diaphragm, gear, piston and vane). Diaphragm and gear pumps are usually bolted to the
engine. Vane and piston pumps are usually incorporated in the injection pump. Lift pumps create a partial vacuum in the
forward fuel line, allowing the atmosphere to push fuel through it. The theoretical maximum vacuum a pump can generate is
14.692 pounds per square inch, or 29.910 inches of mercury. By convention, vacuum is usually measured in inches of
mercury, (1” Hg = 0.4912 PSI).
Vane and piston pumps, though more efficient than diaphragm pumps, are still limited in their ability to draw or lift fuel from
the tank. Most engine manufacturers want fuel pump inlet vacuum kept to 10” Hg.
Every component plumbed into a fuel system contributes to that systems total pressure drop. At maximum flow, FloScan’s
forward sensors produce pressure drops of 1.1 to 1.63” Hg, depending on sensor and application. Other contributing factors
are; fuel line length, inside diameter, numbers and types of fittings, height of the pulsation damper above fuel level, and
micron rating of fuel filters.