Section ii. gas piping, Section iii. duct connections, Section iv. venting – Bryant UNIT 379H User Manual
Page 3: Section v. coil connection (180r- & 240r-379), Section vi. electrical connections
Attention! The text in this document has been recognized automatically. To view the original document, you can use the "Original mode".
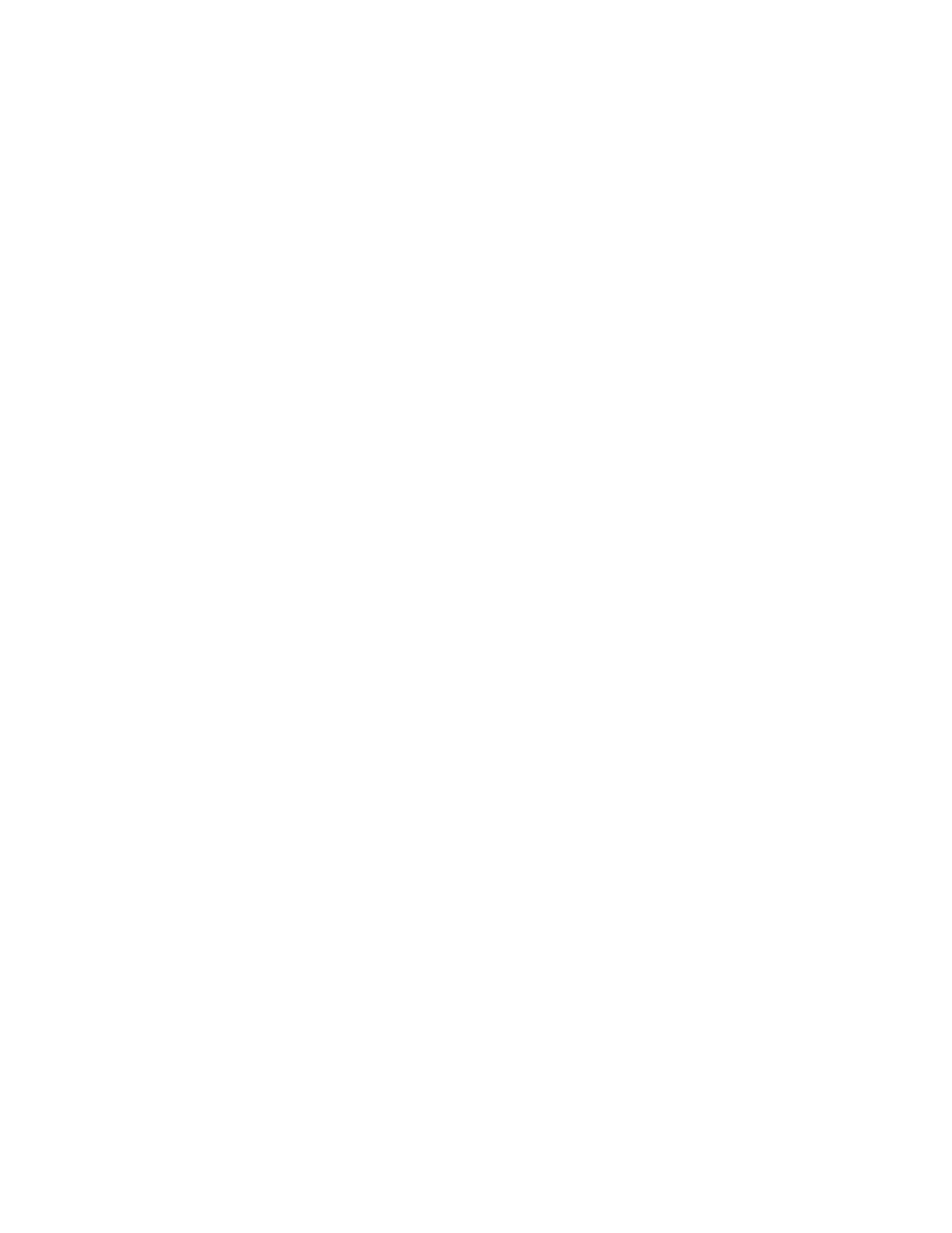
SECTION II. GAS PIPING
A separate gas supply line should be installed to run
directly from the meter to the heating section. Check
your local utility for recommendations concerning
existing lines. Choose a supply pipe large enough to
keep the pressure loss as low as practical. Never use
pipe smaller than the gas connection to the heating
section. Observe local codes for all gas pipe in
stallations.
The following are pertinent recommendations:
1. Avoid low spots in long runs of pipe. It is best to
grade all pipe 1/4 inch in every 15 feet to prevent
traps. All horizontal runs should grade downward to
risers. Risers should be used to connect to heating
section and to meter.
2. Install drip leg in riser leading to heating section.
Drip leg will function as trap for dirt and condensate.
Drip legs should be installed where condensate will
not freeze.
3. Install manual shutoff valve in gas supply pipe
near heating section, where it can be easily reached.
4. Install ground joint union close to furnace between
gas controls manifold and manual shutoff valve.
5. Support all piping with appropriate hangers, etc.
Use a minimum of one hanger every 10 feet.
6. Use joint compound (pipe dope) that is resistant to
action of propane gas.
7. After all connections are made, use soap-and-water
solution to check for leaks (or method specified by
local utility regulations).
WARNING: Never use a match or other open flame.
SECTION III. DUCT CONNECTIONS
Before ductwork can be attached to the unit, remove
the panels located over the outlet and the return air
opening. The ductwork may be screwed or bolted to
the unit flange with suitable gaskets to insure a
weathertight seal. Be sure that the sheet metal over
laps the flange on the unit.
NOTE: When using Bryant plenum package, the up
per skirt of the plenum should be placed up and under
top cover of the unit, then sealed properly. All duct
work external of the structure must be properly insu
lated and waterproofed. All openings in the structure
must be properly flashed in accordance with local
codes and good building practices. The supply and re
turn ductwork should be provided with an approved
vibration eliminator.
NOTE: The vibration eliminator must be located
within the structure.
SECTION IV. VENTING
The vent cap assemblies, including three sheet metal
angles, are packaged in the gas control compartment.
Installation of these assemblies is as follows:
1. Remove the discard cover on each of vents on roof
of unit.
2. Remove top plate from each vent cap assembly by
removing four retaining screws.
3. Use screws supplied with assemblies to fasten base
section of vent cap assembly to vent-section top cover
plate: unit top is drilled to receive these screws.
4. Reattach top cover plate removed in Step 2 above.
5. Remove three self-tapping retaining screws (located
approximately 7 inches behind each vent cap) from
unit cover. Fasten sheet metal angle from each vent
cap (use retaining screws previously removed).
SECTION V. COIL CONNECTION
(180R- & 240R-379)
1. Refer to condenser installation sheet for coil con
nections of R Models. NOTE: Coil connections are
sealed and seals should not be broken until just im
mediately before making connections to condenser
unit.
SECTION VI. ELECTRICAL CONNECTIONS
IMPORTANT: Before proceeding with the electrical
connections, check the power supply to be sure that
the voltage, frequency, and phase correspond to that
specified on the unit rating plate.
All electrical connections must be made in accordance
with the National Electrical Code and local codes
governing such wiring. The field connections must be
made in accordance with the wiring diagrams in
cluded in this instruction (see Figures 3 and 4). A
separate electrical line should be run for this installa
tion and it should contain a fused disconnect switch
placed in a convenient location. For maximum fuse
and minimum wire sizes, refer to Ratings and Capaci
ties Table. Field wiring connections are made in the
control box located in the gas control compartment of
the unit. Wiring entrances are made to the control box
through knock-outs provided in the casing. All wiring
entrances to the unit must be weatherproof and
watertight. The thermostat heating anticipator should
be set at 0.8 amperes for the first stage and 0.4 am
peres for the second stage. Use thermostat assembly
Bryant Part No. 34427D57 (782F) and sub-base
assembly Bryant Part No. 34427D59 (Q672B).
NOTE: Both thermostat and sub-base assemblies are
for heating only. For field wiring diagram, refer to
Figure 3.
■ 3-
39379D35