Maintenance and lubrication, Replacing tiller gear case oil seals – MTD 216-100A User Manual
Page 4
Attention! The text in this document has been recognized automatically. To view the original document, you can use the "Original mode".
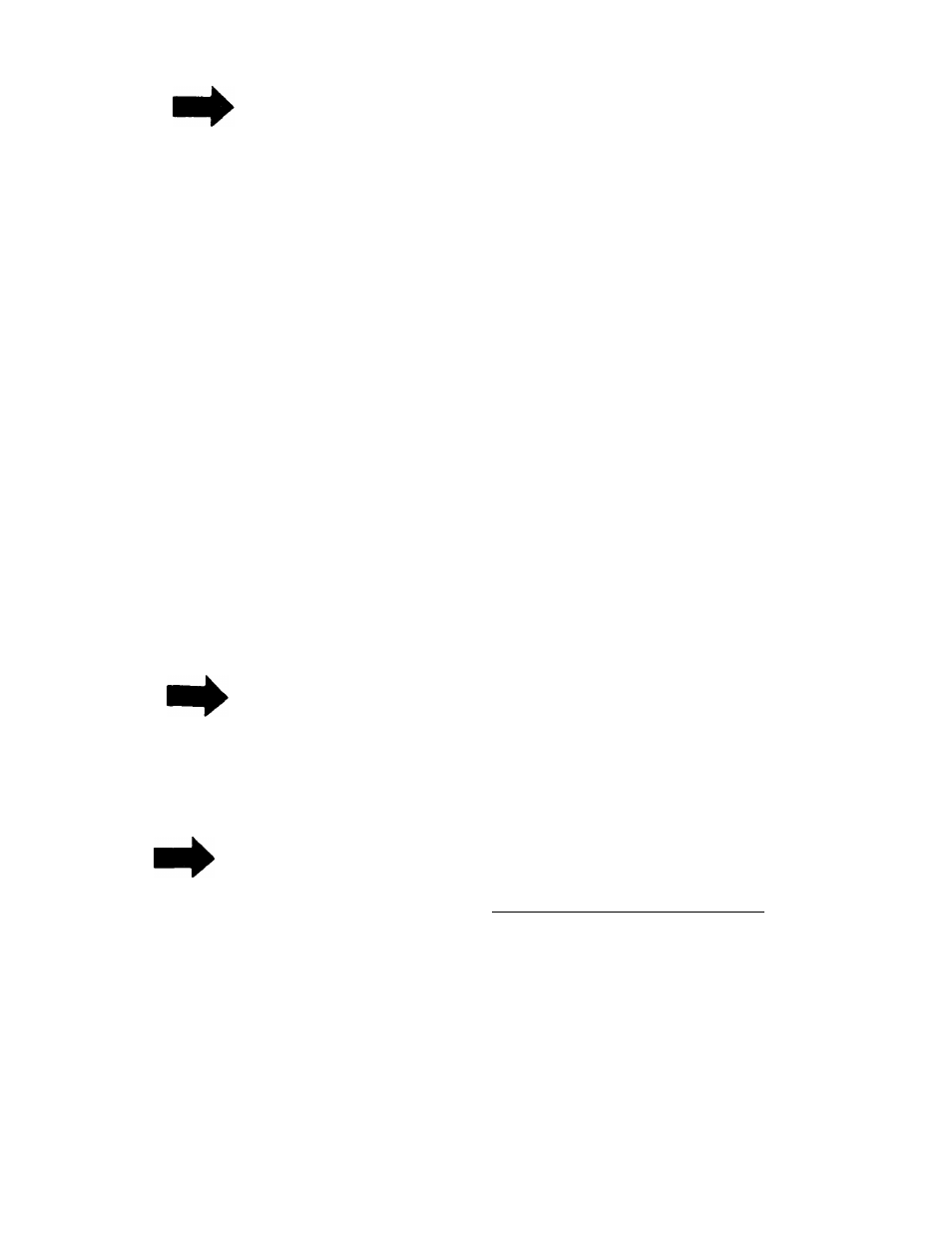
NOTE
Belt and clutch adjustments can be made by moving
the engine bed. Loosen the four bolts which secure it
and move the engine bed forward or backward as re
quired. Adjusting the control rod will also effect the
belt and clutch adjustment. These adjustments may be
necessary if handle position is changed.
Handle—The position of the handle may be adjusted by
removing and moving carriage bolts to the desired
mounting holes. Adjustment should be made for the
most convenient operating height.
Wheels—
Wheel positions may be varied to give fur
ther adjustment of handle height. Various wheel po
sitions also give variations of the leverage and weight
distribution over the tines. Wheels should be set to
suit the local soil conditions and the operator's con
venience.
Tines—
The standard width of cut is 26". Because of the
various types of work to which the tiller may be put,
variation in the tilling widths may be necessary. This
can be accomplished in a number of ways.
1. Standard tine arrangement________________ 26"
2. Remove tines that point outward from
outer tine assemblies. Tines may be
interchanged with opposite sides--------------------- 20"
3. Add tine extensions to standard
arrangement (See page 5.)_______________ __
40"
NOTE
When adjusting tines, be sure the cut
ting edges enter the soil first.
MAINTENANCE AND LUBRICATION
1. Remove four cap screws which secure engine bed
to mounting plate assembly. Remove engine bed
with engine attached.
2.
Remove hex screw, lockwasher and flatwasher in
4V4" pulley. Remove pulley and "V" belt. The belt
clip on idler must be loosened to remove belt, mark
correct location of belt clip in relation to idler before
loosening. This can be done by scribing the belt
clip and the end of the weld bolt in idler with a
file. It is most important that this clip be reassem
bled in the right position.
3. Position new belt on
4V2"
pulley and reinstall on
gear case shaft. Pulley must be mounted in position
so that it will line up with engine pulley when as
sembly is completed. The correct position is that
point at which the center of the pulley is 114" above
the mounting plate assembly. Tighten hex screw,
lockwasher and flat washer securely.
4.
Line up the belt clip in original position and tighten
securely. Make sure belt is inside belt guards. While
holding the belt taut (grasp at extreme rear posi
tion), move clutch belt lever to FORWARD and NEU
TRAL position. If belt clip touches belt with lever in
either position, readjust position of clip.
5.
Move clutch lever to NEUTRAL position. Remove
inspection plate from engine bed.
6.
Replace engine bed on mounting plate assembly.
Move engine bed and engine as far forward as pos
sible.
7. Remove inspection plate (See page 8.) from engine
bed and reach through inspection hole and guide
belt into position on engine pulley.
8. Check visually through inspection hole to make sure
belt is inside all belt guards and that pulleys are in
proper alignment. A flashlight will help you make
this check quickly and easily.
Engine—Service engine in accordance with the engine
manufacturer's owner's guide.
NOTE
To drain oil, remove oil filler plug and
tip tiller on its side. Drain oil while the
engine is warm. See engine manual for
filling instructions.
Geaf Case—
Proper lubricant level should be up to the
front pipe plug. Check with tiller on a level surface.
Add enough to bring level up to front pipe plug hole.
Use Mobilube SAE 140 Gear Oil or equivalent. Gear
case should be maintained with five (5) ounces of lu
bricant.
Beh
— Access to V belt and pulley assemblies is accom
plished by removing the engine and engine bed as
described below.
9.
Line up mounting ho'es of engine bed and mount
ing plate then replace cap screws.-' Do not tighten
cap screws until all four screws are in place. Re
place inspection plate.
REPLACING TILLER GEAR CASE OIL SEALS
1. Drain lubricant.
2. Remove tine assemblies.
3. Remove bearing cap. (See reference 16 on page
10.)
4. Remove bearings, worm wheel and tine shaft. Do
not remove bearing races.
5. Remove oil seals from gear case and bearing cap.
6. Remove all burrs from holes in tine shaft.