Winco ECV2512-3 User Manual
Page 9
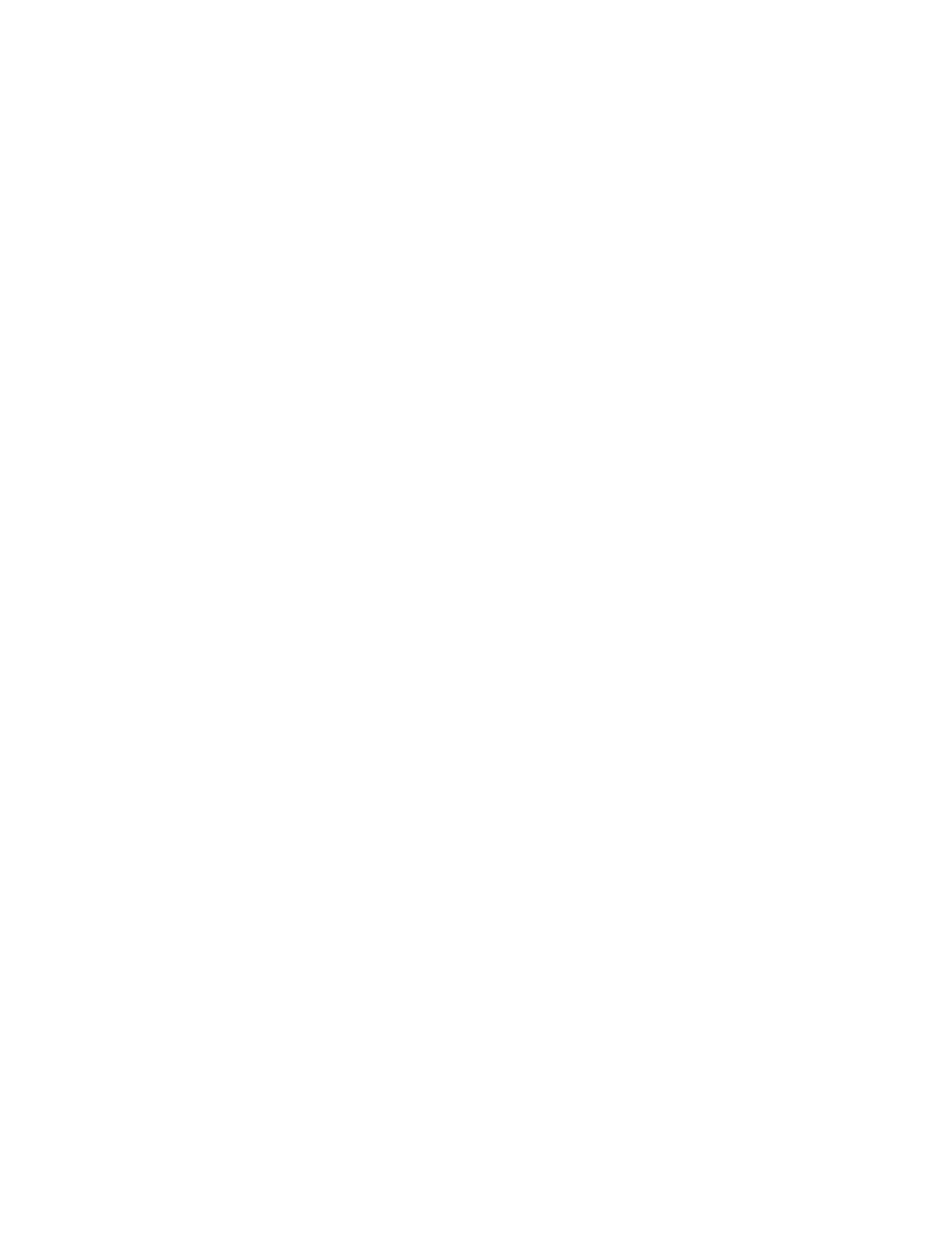
Page 7
60706-130
7150-01
4.
Reverse the meter leads, (black lead to the DC POS (+)
and red to the AC terminals, each in turn. An opposite
reading should be observed.
5.
Connect the red ohmmeter lead to the negative DC (-)
terminal.
6.
Connect the black lead to each of the AC terminals in turn.
Either a high or low resistance reading will be obtained.
7.
Reverse the meter leads, (black lead to the DC NEG (-) and
red to the AC terminals, each in turn. An opposite reading
should be observed.
8.
Check each terminal to the case. An open circuit (very high
resistance) reading should be observed. A battery pow
ered test light is used. Follow the same procedures
described above. A good diode element will allow current
to pass to the light in the test lamp when the leads are
connected in the forward direction.
9.
If the rectifier fails any of the above tests, it should be
considered defective and replaced.
Condenser Testing
Condensers are built into the generator circuit to minimize
radio interference during operation. If a condenser shorts
out, it will also short out the generator output. To determine
whether a condenser is shorted, stop the generator and
disconnect the condenser lead wire from the brush holder.
Using a multimeter on the R x 100 scale, check the resis-
tance of the condenser. Normal response is a sharp swing
of the meter towards low resistance and then a steady rise
towards high resistance (open circuit). If the capacitor is
shorted it will show as a constant low resistance.
Otherwise, restart the generator without the capacitor con-
nected to recheck the generator for output. If the generator then
provides power, the condenser was at fault and should be
replaced. (If the generator doesn't provide power, the problem
was not caused by that condenser, reconnect the lead wire).
If these tests have not located the trouble, remove the
armature and have it tested for opens, shorts, and grounds
on a growler.
4. Lubrication
The generator bearings are factory lubricated and sealed,
and require no further lubrication.
The generator input shaft should be cleaned and lubricated
with a thin film of grease before installing the drive shaft and
each time it is removed.
The drive shaft (tumbling bar) requires greasing. Keep the
universal joints in the coupling shaft free from grease and dirt
buildup.
NOTE:
Do not over lubricate the universal joints.
Check the generator gear case oil level before each use of
the generator. Maintain the oil level at oil level plug height.
(See page 3 for oil level plug location.) The generator is
shipped with lubricant in the gear case. Specifications for
gear case lubricant are:
API Service: GL-5
Grade: SAE 85W-9O-140
Amount: 1 pint
The following kinds of oil are recommended for use in the
generator gear case: Mobil SAE 85W90-140 API Service GL-
5, Sunoco/DX XL80W90-140 Kendal Three Star 85W-140,
Amoco 85W140 or equivalent.
CAUTION: Equipment Damage
Do not overfill generator gear case. Overfilling causes
overheating and oil seal failure.
Change the oil at least once every six months. Change it
more often if you use the generator in bad weather. Use the
following procedure to change generator gear case oil:
1.
Remove gear case breather. Soak breather in cleaning
solvent, then allow it to dry.
2.
Remove oil level check plug.
3.
Remove the oil drain plug, drain the oil into a clean oil
resistant container, 1 quart or larger. Check the oil for
metal. Fine metal dust in the oil does not indicate
trouble, but metal chips do. Dismantle the gear case and
look for damaged gears if you find metal chips in the oil.
4.
Replace the oil drain plug. Refill the gear case through
the breather port with new oil of the recommended type.
Fill the case up to oil level check plug height. (It will take
about 1 pint.)
5.
Replace the oil level check plug.
6.
Replace the breather.