FloAire STEAM COIL User Manual
Page 6
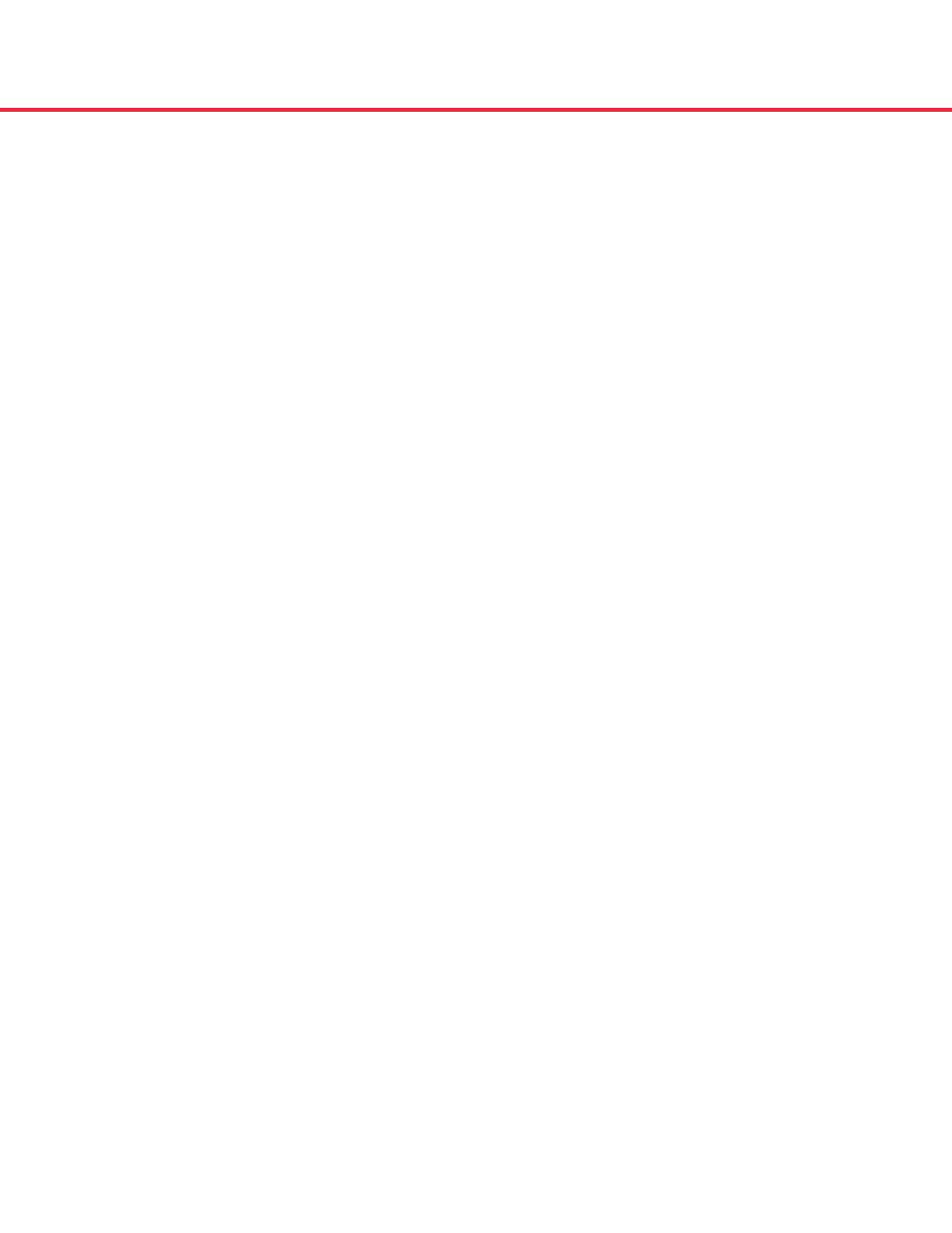
STEAM IOM
4
3. Mount coil properly to insure positive condensate drainage. Refer to Mounting instruc-
tions Page 2.
4. Proper clearance should be maintained between the coil and other structures such as the
fan, filter racks, transition areas, etc.
5. Utilize vacuum breakers on each coil. Steam traps require a positive pressure differential
to force the condensate through the valve seat. If the coil’s pressure drops below atmo-
spheric, the pressure differential across the valve will be negative and the condensate will
not drain. This condition can lead to serious damage or failure of the coil due to freez-
ing, water hammer and corrosion. Refer to piping diagram for recommended placement.
See Note 1 in Figure 3 - Steam Coil Piping Diagram on Page 3.
6. Trap each coil separately. Differences in pressure from coil to coil can result in the
backing-up of condensate which will result in poor coil performance and possible dam-
age.
7. Provide an air vent for each coil at its highest location. Heatcraft provides a ½” threaded
vent connection on the return manifold as a standard on all steam coils. Non-condens-
able gasses present in the steam will collect in a coil and reduce its capacity. Therefore,
it is necessary to provide a means for the removal of these gasses. Also, these gasses can
diffuse into the condensate forming byproducts, which can lead to severe corrosion. See
Note 1 in Figure 3 - Steam Coil Piping Diagram on Page 3.
8. Steam supply lines need to be drained of condensate. This can be accomplished by the
use of drip legs. This ensures that high quality steam enters the coil.
9. Condensate return piping should be the same size as the coil’s return connection from the
coil outlet to the steam trap.
10. Once installed, the coil should be pressurized to 100 psig with dry nitrogen or other
suitable gas. The coil should be left pressurized for a minimum of 10 minutes. If the coil
holds the pressure, the hook-up can be considered leak free. If the pressure drops by 5
psig or less, re-pressurize the coil and wait another 10 minutes. If the pressure drops
again, there are more than likely one or more small leaks, which should be located and
repaired. Pressure losses greater than 5 psig would indicate a larger leak, which should
be isolated and repaired. Be sure to check valves and fittings as potential sites for leak-
age or bleed. If the coil itself is found to be leaking, contact your local Heatcraft repre-
sentative. Unauthorized repair to the coil may void the coil’s warranty (see Heatcraft’s
warranty policy on back cover).
11. All field brazing and welding should be performed using high quality materials and an
inert gas purge (such as nitrogen) to reduce oxidation of the internal surface of the coil.
12. All field piping must be self supporting. System piping should be flexible enough to
allow for thermal expansion and contraction of the coil. The use of flexible connections
and/or swing joints is recommended.