Dynaflite Original User Manual
Page 7
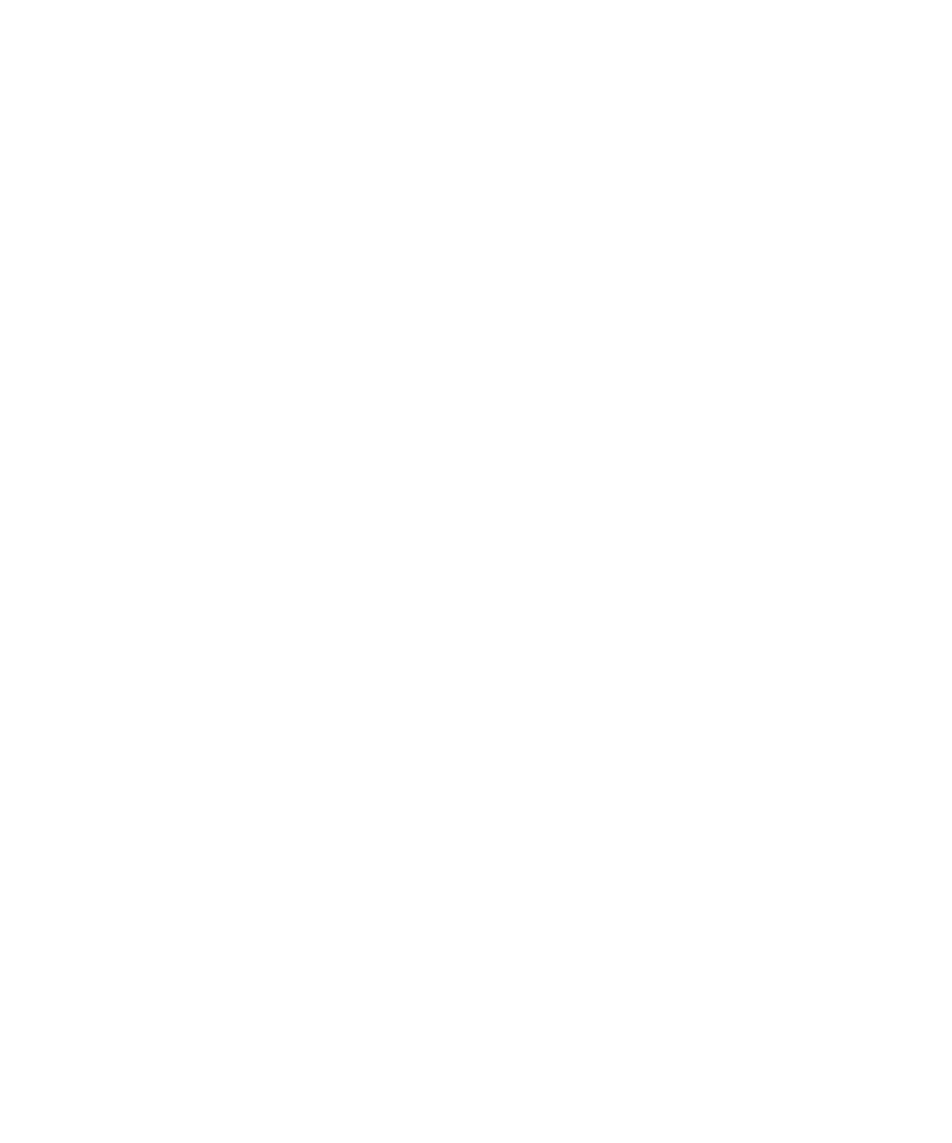
4. Use either epoxy or Titebond or white glue to fasten the noseblock
to the sides. Pin the bottom edge flat to the work surface while
drying so fuselage sides will be aligned.
5. Epoxy l/l6" plywood doublers to bulkheads 1, and 2 as shown on the
drawing. Drill 1/4" holes and epoxy the 1/4" dowel into the holes. Sand
the vee notch into the top of all three bulkheads - notch for Nyrods & antenna,
To digress a moment - most contest flyers are occasionally forced to make
those point-getting spear landings. One problem with the type wing
hold-down system used on the Bird is that sometimes during a spear, the
wing slides foreward, forcing the rubber bands, off the dowel, the wing
flies off and - zowie, no landing points.
So - if you will drill a vertical l/l6" hole about 1/8" from the end of
the dowel in bulkhead #1 and make a piano wire cotter pin to slide through
it, this will prevent the rubber bands from sliding off.
6. The bottom front fuselage block is jig-cut to the right width. This
should be installed first. Remember - the aft end is at bulkhead 2. With
the top of each bulkhead flush with the fuselage top, mark the location
of the bottom on the fuselage sides. To align the fuselage I stick a pin
in the exact center of the noseblock and run a thread from there to the
rear of the fuselage. Now, align the fuselage sides until the thread
exactly splits the fuselage all the way to the back. Pin the ends tightly
together using a 1/4" spacer to simulate the fin. Glue in the bottom
front fuselage block using epoxy. Align to the bulkhead bottom marks
and the center of bulkhead #2. Clamp tight until epoxy cures.
7. Using Titebond or white glue install the rear bottom block against
the front block and flush with the bulkhead bottom locations.
8. Sand bulkheads 1, 2, and 3 for a proper fit and epoxy into position.
If you have filed notches for an antenna tube, make sure they all line up.
9. Use Titebond or white glue to install the fin. The foreward fairing-
fin will be installed later.
10. Trim the nylon stabilizer horn leaving one hole on one leg. The
other leg may be also trimmed leaving one hole - or you can leave all
three "Just in case". Ream the bearing hole to provide a good fit for
the 1/8 tubing. Pile a notch in the 3/l6" square brass pushrod tube
to provide for attachment of the horn - as shown on the drawing. Take
a short length of 1/16" brass tubing, clamp in a vise and carefully pin the
end into a small head. Use this as a bearing to assemble the horn and
square brass pushrod as shown on the drawing. Insert the bearing tubing,
cut to length, place on vise and pin the other side into a head. Pretty
clear, eh?... Or you can just solder it in.
6.