Dynaflite Original User Manual
Page 4
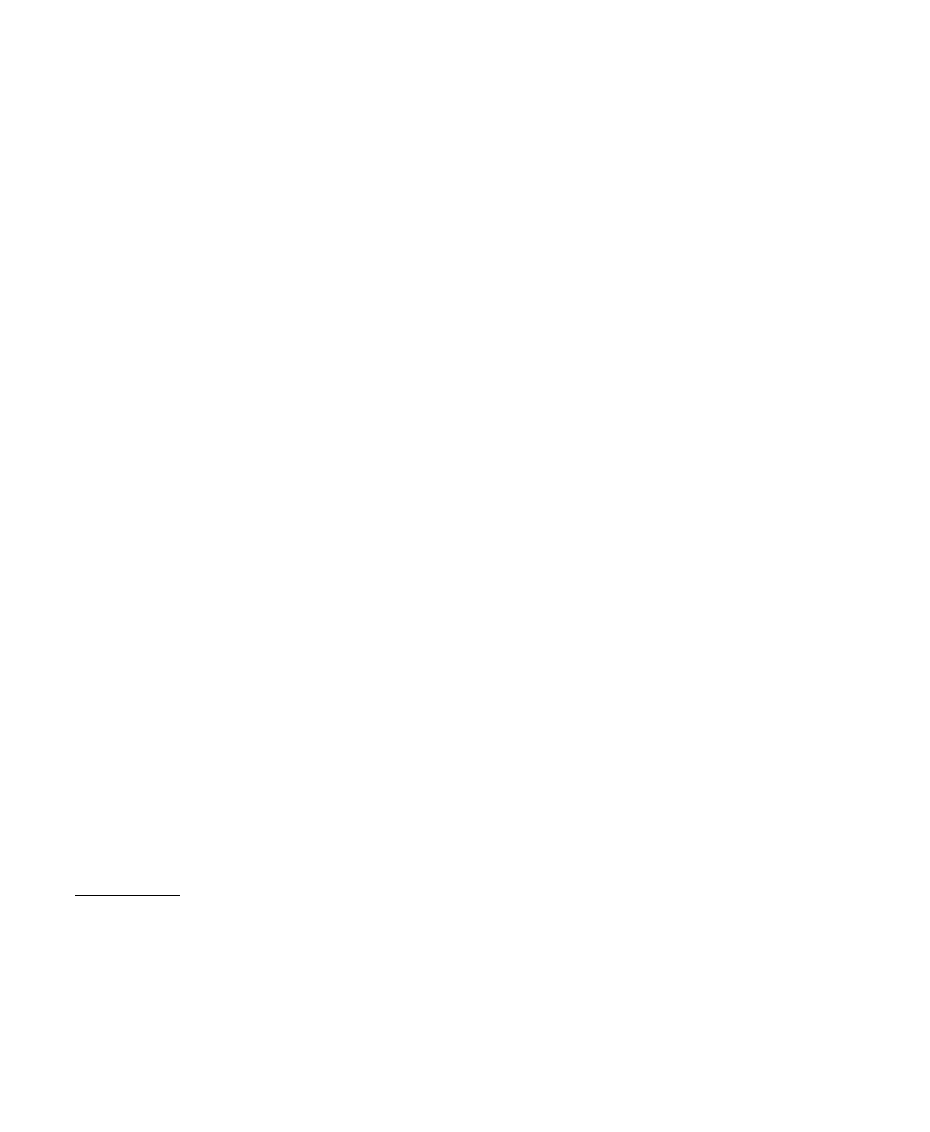
18. Unpin the Inboard panel from the building board. Block It up,
laying the outboard panel flat on the building board and pin it tightly.
Trim and splice another l/l6" X 3" X 36" balsa sheet for the top
leading edge sheeting.This sheeting may extend to the end of the tip,
if you wish. Glue in place again being careful that the sheeting is snug
against the ribs. Glue and pin the l/l6" X 1/4" cap strips in place.
When dry remove from the building board.
19. Sand the leading edge of both panels perfectly flat using a two or
three foot sanding block as Dave describes in his instructions. Cut 1/8"
from the A rib at the polyhedral joint. Carefully glue the 1/8" plywood
leading edge brace into place, flush with the sheeting. Trim the leading
edges for a good fit at the polyhedral joint and glue into place, holding
firm with strips of masking tape. Sand the root of the inner panel flat
and glue the plywood root rib in place.
20. Cut the leading edge template from Dave's instruction sheet and rubber
cement it to a piece of scrap plywood. Carefully saw and sand the pattern
to shape. Carve and sand the wing panel using the leading edge template
as a guide. Take as much time as your patience will allow in shaping
the leading edge. The more true the leading edge airfoil, the better
the Bird will fly. Of course there is a point of diminishing return.
21. Before building the right hand wing, finish the left hand panel at
least to the point of having the plywood root rib in place. The right
wing is built exactly like the left with one exception: the fitting and
epoxying of the brass wing-rod tube is done with the left hand panel
blocked in place to the proper height and the panels connected with the
wing rod. This procedure not only establishes the correct dihedral but
aligns the root ribs for a clean joint. Also, when epoxying the right
hand plywood root rib in place, do it with the wing rod in place and
both halves pressed together. Don't let them get stuck though, a ten
foot wing is hard to get into a Volkswagen.
22. You have probably noticed that the wing rod is shorter than the length
of both tubes. Left to it's own devices, the rod will slide to one side
and you will have two and one-half inches in one wing and five and one-
half inches in the other. So - push a snug-fitting short length of 1/4"
dowel to the bottom of both brass tubes. Or - before assembling the wing,
center the wing rod in the two tubes and, using a center punch, dimple
the tubes a little beyond the ends of the rod. This of course can't be
done after the wing is built. So - if you didn't read the instructions
through first, like you're supposed to, it's too late.
After a thorough sanding your wing is now ready to cover.
STABILIZER
1. Using scrap balsa sheet cut a half-dozen each of 3/32" by about an
inch square and l/l6" by half an inch square. These will be used as shims.
Cyanoacrylate the die-cut 1/8" balsa trailing edge and tip together. Cut
the 3/l6" leading edge to length. Cyanoacrylate the 1/8" triangular die-
cut brace to the leading edge, centering it top to bottom.
3.