CAMCORP Blower Package with Sutorbilt Blower User Manual
Page 45
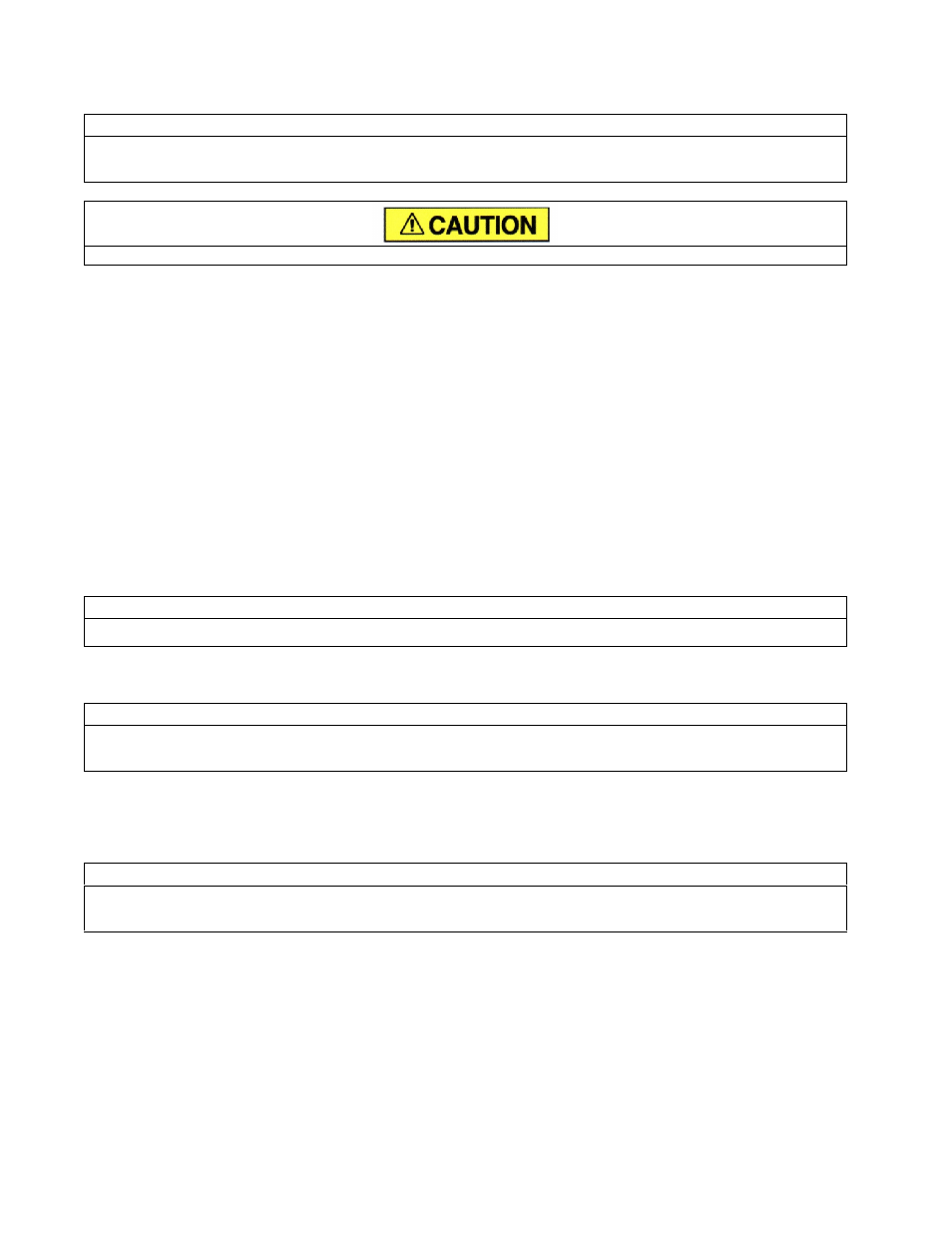
SB-7-621 Page 32
NOTICE
If gears are being replaced, taper pin holes must be drilled after the gears are correctly positioned.
Be careful not to let cuttings drop behind the gears and contaminate the bearings.
Be careful not to let cuttings drop behind the gears and contaminate the bearings.
F. Place impellers in the position shown in FIGURE 7-4, page 30. Check to be sure impellers are in correct
position as previously match marked.
G. Drive the mating gear on the other shaft within 1/2” of being flush with the end of the shaft.
H. Refer to diagram in FIGURE 7-4, page 30. Use feeler gauges to check clearances between impeller
lobes at positions A--A and C--C. Add the clearances, and divide the total clearance evenly between A--A
and C--C.
I. If the lobe clearance is not equal between A--A and C--C, the impellers require shifting relative to the
gears. Insert a feeler gauge .010 inch larger than required clearance between the impellers at the tight
spot and rotate the impellers wedging the feeler gauge between the lobes. Place the driving tool against
the gear that is not flush with the end of the shaft, and strike the driver with a quick blow. This will drive
the gear further onto the shaft, causing it to turn relative to the shaft due to the torque value set--up by the
oversized feeler gauge wedged between the impeller lobes. Adjust so that the clearance at A--A is equal
to C--C within .001 inch. Clearances must be checked on both sides of each impeller lobe over the entire
length. This procedure may require repeating several times until the impeller lobe clearance is equal on
both sides.
NOTICE
The gear used for adjustment should be flush with its mate on completion of the timing.
J. Check gear backlash four places at 90 degree intervals as described in the disassembly procedure
(Item 4).
NOTICE
If any of the four gear backlash readings are not within the specified limits, the gears must be
replaced.
14. After timing adjustments are completed, re-ream the original hole between shaft and adjustment gear if
movement between the shaft and gear are negligible. If reaming fails a new hole approximately 90 degrees
from the original hole. Apply a thin coat of Loctite 620 to the taper pin and install the taper pin in the reamed
hole between the shaft and gear.
NOTICE
Replacement gears are not drilled.
These holes must be drilled after the gears are in the proper
position and the unit retimed.
15. SETTING IMPELLER END CLEARANCES
Refer to FIGURE 7-6, page 33. The outer races of the gear end bearings are clamped against the headplate
(F) by the bearing retainer (B).
This is referred to as the “fixed end”. The interference fit between the shaft and the bearing inner race (H)
keeps the shaft from moving axially. Adjustment is by movement of the shaft through the gear end bearing
inner race (H).
A. Check the total end clearance by adding the clearance between the impellers and the drive headplate to
the clearance between the impellers and the gear headplate.