Just Better Deep Vacuum Principles and Applications User Manual
Page 2
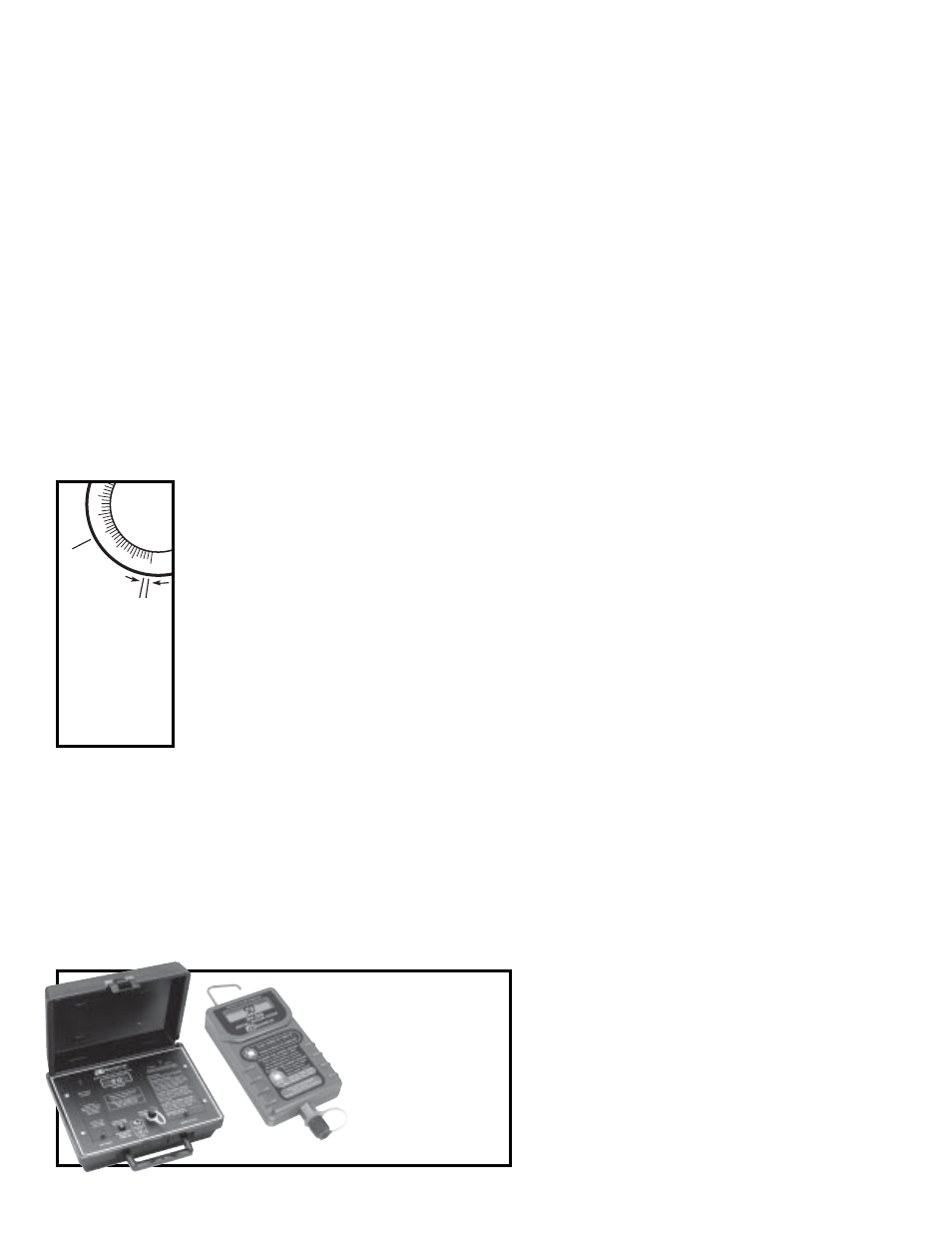
10
0
10
20
30
Last Inch
Of Pressure
ATM
The electronic vacuum gauge
is the least purchased deep
vacuum tool. Yet, without
this instrument you might
just as well forget about
deep vacuum
altogether.
dry ambient air is admitted to help prevent the moisture
vapor from condensing in the oil.
So far, we have defined our pump requirement as
follows: 2-stage, rotary vane; blankoff valve; gas ballast
valve; 1-1/2 to 10 CFM. A system is evacuated to
between 300 and 400 microns so obviously these
pumps should be able to produce vacuum in the low
micron range with a safety factor of at least 25 microns
total absolute. Thus, the pump should be able to achieve
vacuum readings of at least 25 microns total absolute.
We should also look for light weight and rugged con-
struction because we all know the vacuum pump will be
at our side as we climb those ladders to the roof top.
Finally, when checking out pumps, look at safety.
Belt driven units should never be used without belt
guards—if you don’t give a darn about your own fingers,
etc., give children and others exposed a chance.
Hospitals and court rooms around the world are full
because of this negligence.
The Electronic Vacuum Gauge
Coupled with good procedures which we will get
into later, the electronic gauge tells
us positively that we have a
noncondensable and a leak free
system. In general these gauges are
heat sensing devices, in that the
sensing element which is mechani-
cally connected to the system being
evacuated generates heat. The rate
at which this heat is carried off
changes as the surrounding gases
and vapors are removed. Thus, the
output of the sensing element (either
thermocouple or thermistor)
changes as the heat dissipation rate
changes. This change in output is
indicated on a meter which is
calibrated in microns of mercury.
Evacuation is complete when a system holds at 500
microns. The compound gauge only indicates that a
vacuum is being produced. The vacuum gauge on the
other hand, is the only tool for accurately reading that
low pressure.
Vacuum Gauge Selection And Accuracy
The most important feature of all is range. If the
micron gauge only indicates from 50 to 1,000 microns,
you will not be able to determine whether you are
pumping against a leak or against moisture. Look for an
instrument that reads from 50 microns to at least
9,000 microns.
A digital display with easily read numbers gives you
instant and continuous readout, whereas a gauge with
color-coded lights, displays the reading “within a range”
of microns. You have a “wait” period to see whether the
system is going up or down in microns.
Portable micron gauges typically operate from
battery power and should have a low battery sensor.
Some models have AC adaptor capability so you won’t
run out of power on the job.
Another feature to look for is a sturdy case to
protect the instrument. Finally, when you buy instru-
ments of this type, remember that you are really only
buying answers, and the instrument should give you
these answers quickly and accurately. You get paid for
adjusting refrigeration systems, not your tools.
As already noted, we are talking about accuracy
when we talk about micron type gauges. Gauge accu-
racy is affected by two factors. Extreme temperatures
especially with exposure to the summer sun on a hot
roof top or pavement and sensor contamination.
The vacuum sensor is factory calibrated on air. If
refrigerant gas or oil is drawn into the vacuum sensor of
a remote reading unit or unit connected to the pump
during the system evacuation, the gas will cause an
erroneous reading. Any oil entering into the vacuum
sensor via hose will also affect gauge accuracy. Im-
proper shut down of pump after evacuation and loss of
power will suck back oil and contaminate the hose and
micron gauge.
A hose used for charging or testing will contain
droplets of system oil spurted into the hose when the
schrader valve is opened. If this same hose is used on
the hookup to the gauge, oil will collect in the gauge
sensor. This can be prevented by using a dedicated
hose, preferably O-Ring type, for evacuation.
Evacuate Through The Gauge Manifold
Evacuate through the gauge manifold if, and only if,
it is O-ring sealed, piston construction. Other types leak
under vacuum. Next look at the design of the center
port. In order to handle the full capacity of both the high
and low side, the center intake should have double size
flow path throughout its length. All J/B 1/4" manifolds
have this feature. We suggest the fitting be replaced with
a 3/8mf x 1/8mp. You will now have a fulll flow
3/8" to the vacuum pump. You also have the
option of using the M4-Series manifold which is
designed to evacuate, charge or test a system
without disconnecting hoses and features
a 3/8" fitting.
Leak-Proof Hook-up
Deep vacuum has it own unique properties
which requires leak-proof design not only in the
manifold but in all components. The only con-
necting lines that are absolutely vacuum tight are
soft copper tubing or flexible metal hose. Charg-
The last inch of
pressure, as
indicated on the
compound
gauge is 25,400
microns.
Battery
Battery/Electeric