Quick setup guide for intelliag model cta – Great Plains CTA4000 Quick Start User Manual
Page 4
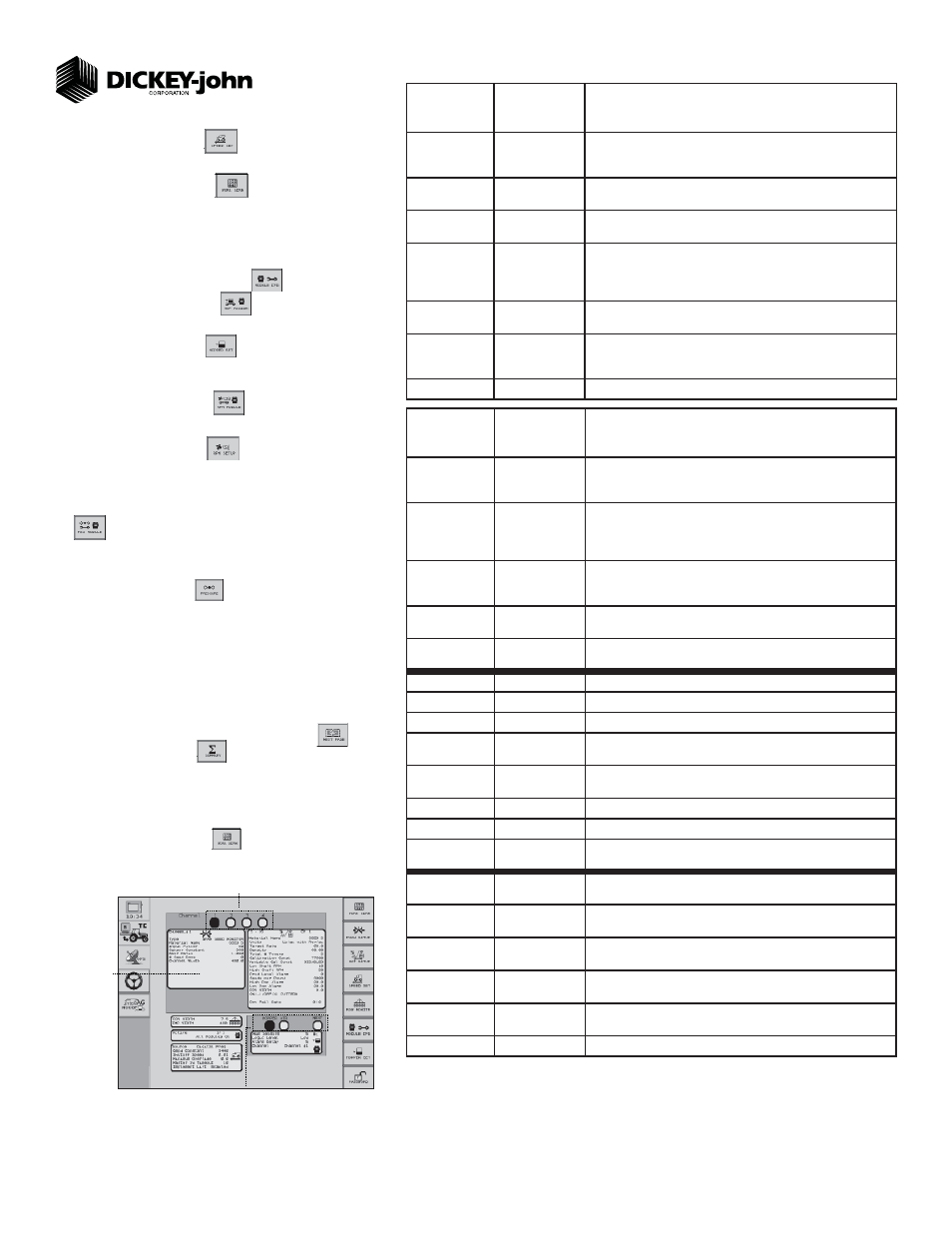
Quick Setup Guide for IntelliAg Model CTA
11001-1459C-201107
©2011 DICKEY-john Corporation
Specifi cations subject to change without notice.
STEP 8: Accessory Sensor Setup
Hopper Setup
Press the Module Confi guration button
.
Press the Hopper Assign button
.
Verify # of hoppers is correct or enter # of hoppers assigned.
Press the Hopper Set button
.
Enter desired values using Table I as reference.
RPM Sensor Setup
Press the RPM Module button
.
Enter # of RPM sensors, if required.
Press the RPM Setup button
.
Enter desired values using Table I as reference.
Pressure Sensor Setup
At the Module Confi guration screen, press the PSI Module button
.
Verify # of pressure sensors or enter the # of pressure sensors as-
signed.
Press the Pressure button
.
Enter desired values using Table I as reference.
For additional information regarding hopper level, RPM, and pressure
sensor setup, reference the Operator’s manual.
1.
2.
3.
4.
5.
6.
7.
8.
9.
9.
10.
11.
12.
TABLE I:
Accessory
Setup
Default Value or
Value to Enter
Instructions/Defi nitions
# of Hoppers
2
# of hopper sensors connected to each module. # of hopper data items
for each listed module and the Hopp #’s value will automatically populate if
Auto Confi g is used to confi gure installed sensors.
Hopper Logic
Level
Active Lo
Sets the active state to low signifying that an alarm is generated if the
sensor’s output is in a low state. Use this setting if the connected sensor
outputs a low condition when empty similar to the DICKEY-john hopper
sensor.
Hopper Alarm
Delay
5 sec
Controls the delay time between the detection of a high/low hopper alarm
condition and the generation of the resulting alarm. The value is entered
in seconds.
Channel
(Hopper #1)
1
Assigns hopper sensor 1 to channel 1.
Channel
(Hopper #2)
2
Assigns hopper sensor 2 to channel 2.
# of RPMs
1
Number of RPM sensors connected to each module to monitor a shaft/fan.
High Alarm
4100 RPM
Sets the RPM value at which a high RPM warning error is generated.
Low Alarm
2500 RPM
Sets the RPM value at which a low RPM warning error is generated.
High Alarm Delay
5 sec
Establishes the delay between the detection of a high RPM alarm condition
and the resulting alarm display (entered in seconds).
Low Alarm Delay
5 sec
Establishes the delay between the detection of a low RPM alarm condition
and the resulting alarm display (entered in seconds).
RPM Constant
3 pul
Number of pulses per sensor revolution.
RPM Filter
50%
Filters the signal out of the RPM sensor.
Disable Control on
Low Alarm
Disabled
Allows for disabling of all control channels if the RPM value of the selected
sensor falls below the low alarm level setting.
# of Pressure
Sensors
2
Number of pressure sensors connected to each module to monitor pres-
sure.
High Alarm
20 oz/in
2
Sets the pressure value at which a high pressure warning error is gener-
ated (oz/in
2
).
Low Alarm
4 oz/in
2
Sets the pressure value at which a low pressure warning error is generated
(oz/in
2
).
High Alarm Delay
5 sec
Establishes the delay between the detection of a high pressure alarm
condition and the resulting alarm display (entered in seconds).
Low Alarm Delay
5 sec
Establishes the delay between the detection of a low pressure alarm condi-
tion and the resulting alarm display (entered in seconds).
Pressure Filter
50
Filters the signal out of the pressure sensor.
Press in
highlighted
box to open
Channel Selection
Accessory Selection
Summary Screen
4
STEP 7: Ground Speed Calibration Setup
Press the Speed Set button
.
Enter desired values using Table H as reference.
Press the Work Screen button
when Ground Speed Calibration
confi gurations are complete to return to the Main Work screen.
1.
2.
3.
TABLE H:
Ground Speed
Setup
Default Value or
Value to Enter
Instructions/Defi nitions
Source
Digital Frequency
Select CAN Ground if radar is connected to ISO tractor cab harness. Select
Digital Frequency if radar or hall-effect is connected to WSMT actuator
harness.
Gspd Constant
3440 Pul/400 ft
Input based on pulse count produced by the ground speed sensor over 400’
distance. See Operator’s manual for calibration instructions.
Shutoff Speed
0.01 mph
0.02 kph
Indicates the minium ground speed allowed before the system shuts off all
control channels.
Min Override
0.0 mph
0.0 kph
Minimum Override takes over when actual ground speed is below the
designated value. The control operates at this speed until actual ground
speed rises above the minimum override speed or the actual speed drops
below the shutoff speed.
Master Switch
Timeout
5 sec
Determines the length of time before the system disables the operate func-
tion after ground speed is 0 if the master switch remains in the ON position.
Ground Speed
Failure Alarm
Delay
5 sec
Set to desired number of seconds alarm sounds after the ground speed is
zero and seed fl ow continues. (monitor only)
Implement Lift
Enabled
Implement lift switch must be in the down position to operate.
STEP 9: Summary Screen
The Summary screen provides an overview of setup constants for active
control channels.
At the Main Work screen, press the Next Page button
.
Press the Summary button
To view specifi c control channel confi gurations, press the respective
control channel box 1-4.
Press inside a yellow highlighted box to open a specifi c screen for
editing.
Press the Work Screen button
to return to the Main Work screen.
1.
2.
3.
4.
5.