RCBS Pro 2000 Auto Index Reloading Press User Manual
Page 8
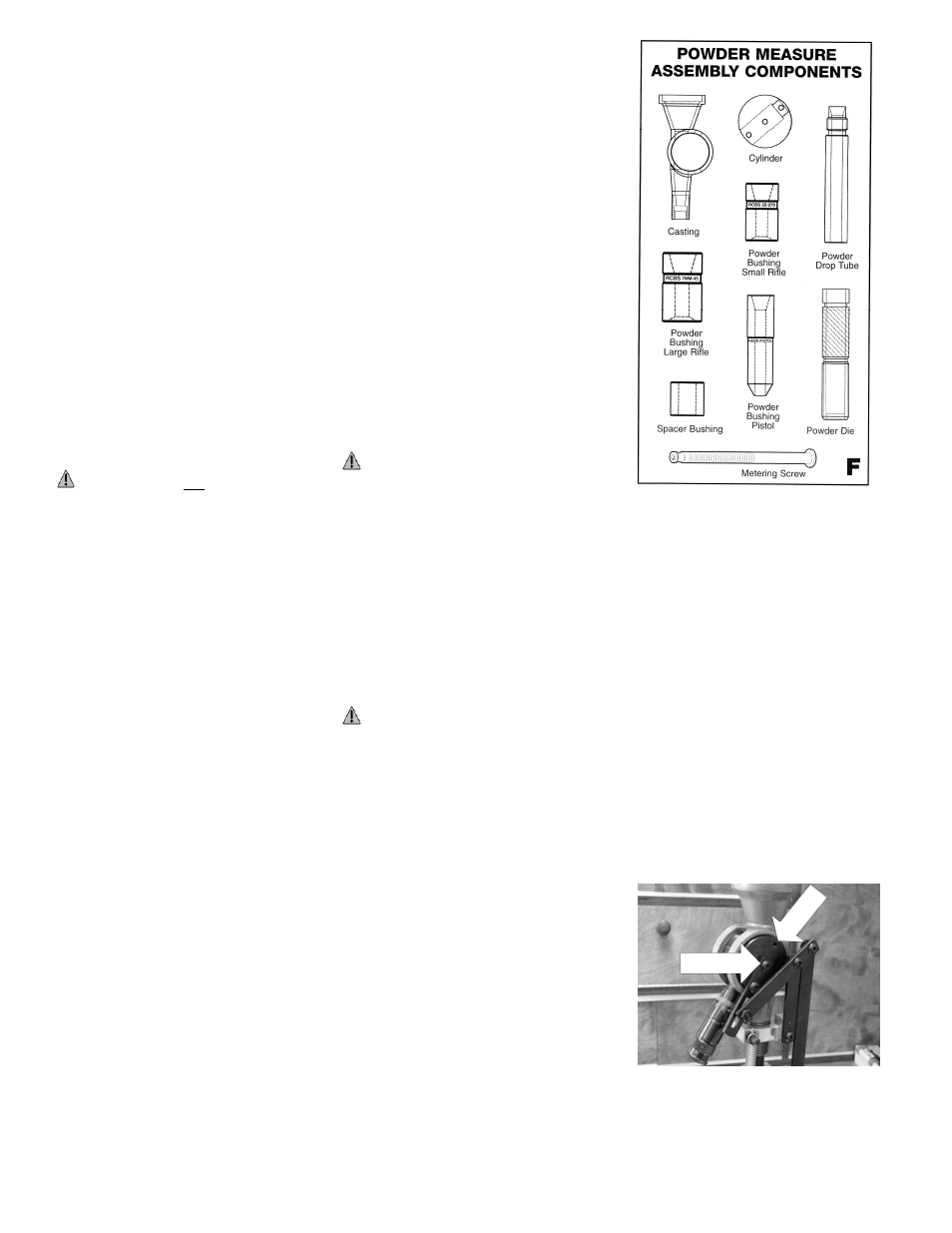
- 8 -
Lower and then raise the handle to
run the cartridge back into the Seater
Die. Check the crimp. If more crimp is
desired, repeat the preceding step by
adjusting the die downward another
1/8 of a turn. This is a “trial and error”
operation. Typically, you will not lower
the Roll Crimp Seater Die body down
more than one-half a turn for proper
crimp. After you are satisfied with the
amount of roll crimp, tighten the Die
Lock Ring.
Insert the “setup” cartridge back into
Station 5 and lower the handle. To re-
set for cartridge overall length, thread
the Bullet Seat Plug down until it
firmly touches the bullet. Tighten the
Bullet Seat Plug Lock Nut.
The Roll Crimp Seater Die is now
properly adjusted to seat the bullet
and roll crimp in one operation.
BULLET SEATING AND CRIMPING
- Taper Crimp
CAUTION: Do not adjust the
Seater Die down against the shell
plate as it will distort or crush the
case.
First, follow the instructions for
BULLET SEATING, before continuing
with this section.
We will now adjust the Taper Crimp
Seater Die to crimp the case mouth
into the bullet. Taper Crimped
cartridges are typically used in semi-
automatic firearms that headspace off
of the case mouth.
Insert the uncrimped “setup” cartridge
back into Station 5 and lower the
handle. With the uncrimped cartridge
up in the Seater Die, loosen the Bullet
Seat Plug Lock Nut and
unscrew(raise) the Bullet Seat Plug
several turns. Loosen the Die Lock
Ring and thread the Seater Die body
down. You will start to feel firm
resistance, stop here. Raise the
handle.
Check the amount of taper crimp.
Measure the case at the base of the
bullet and then measure the case at
the case mouth. The measurement at
the case mouth should be .001” to
.002” smaller than the measurement
of the case at the base of the bullet. If
more crimp is needed, repeat the
preceding step by adjusting the die
downward another 1/8 of a turn. This
is a “trial and error” operation. After
you are satisfied with the taper crimp,
tighten the Die Lock Ring.
Insert the “setup” cartridge back into
Station 5 and lower the handle. To re-
set for cartridge overall length, thread
the Bullet Seat Plug down until it
firmly touches the bullet. Tighten the
Bullet Seat Plug Lock Nut.
The Taper Crimp Seater Die is now
properly adjusted to seat the bullet
and apply taper crimp in one
operation.
POWDER MEASURE
A powder measure is basically a
device which measures powder by
volume, not weight. However, before
you start throwing a given charge with
a powder measure, the first charge
must always be weighed on a powder
scale to arrive at the desired charge.
Accurate powder measure charges
will also depend upon the size and
uniformity of the powder kernels used.
DANGER: DO NOT use the
Uniflow Powder Measure with black
powder!
Helpful Tip: The consistency of the
powder and static electricity are
causes of erratic powder charges.
Slowly roll the powder container
several times to homogenize it before
pouring it into the powder hopper.
Static electricity can be reduced by
wiping down the powder hopper with
a clothes dryer sheet.
CAUTION: All internal components
of the powder measure assembly
must be thoroughly cleaned of rust
preventatives applied at the factory.
Failure to do this will cause powder
charges to be inconsistent and
provide erratic performance of your
reloads. See Diagram F for the
following items that must be clean
and dry before use:
• Casting
• Cylinder
• Metering Screw
• Powder Die
• Powder Bushings
• Spacer Bushings
• Powder Drop Tube
POWDER MEASURE ASSEMBLY
COMPONENTS-
A dependable powder scale should
be used to set the first charges in the
powder measure. It is not necessary
to empty the powder hopper each
time you change charges unless a
different powder is required.
POWDER MEASURE ASSEMBLY
Choose the correct cylinder.
•
The large cylinder throws
charges of 5-99 grains.
•
The small cylinder throws
charges of 2 to 50 grains.
To install the cylinder, make sure the
screw holes are oriented facing
toward the Linkage Assembly before
you slide it into the Main Casting.
See Photo A.
Photo A