Warning – Bendix Commercial Vehicle Systems EverSure Spring Brake with No Touch Technology User Manual
Page 5
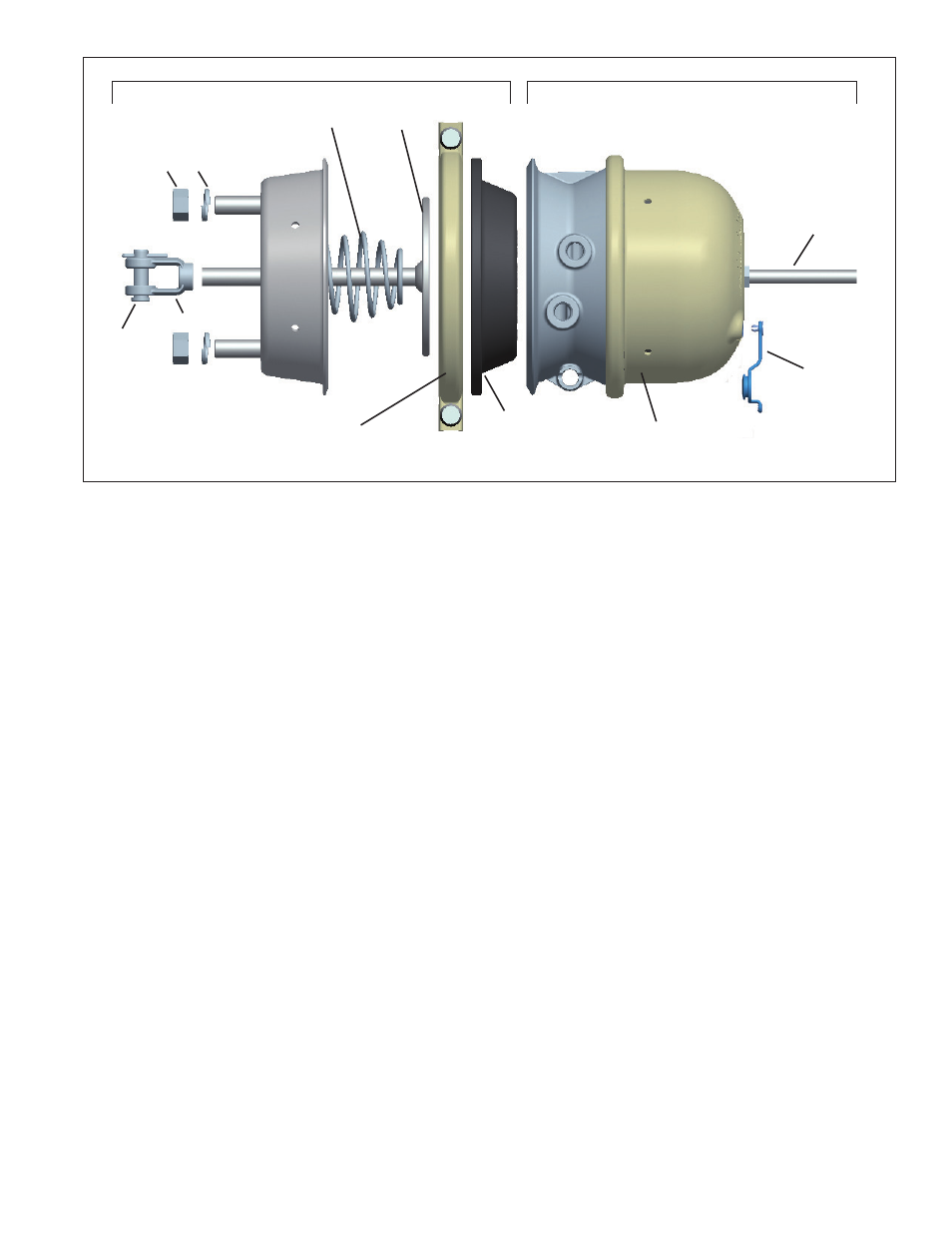
5
FIGURE 4 - EXPLODED VIEW SHOWING SERVICEABLE AND NON-SERVICEABLE PORTIONS OF THE BRAKE
SERVICEABLE SECTION
SERVICE RETURN SPRING
NON-SERVICEABLE PIGGYBACK SECTION
YOKE
PIN
NUT
PARKING/
EMERGENCY
BRAKE
SERVICE
DIAPHRAGM
RELEASE TOOL
DUST CAP
PRESSURE
PLATE
CLAMP BAND
6.0.6. Pull on the release tool to ensure the T-section is
properly seated in the power spring piston plate.
6.0.7. Assemble the release tool washer and nut onto the
release bolt and finger tighten only. If caging is being done
manually, it is recommended that some type of lubrication
be applied to the release bolt threads prior to tightening to
prevent galling or stripping.
6.0.8. To manually cage the spring brake, turn the release
tool nut clockwise with a hand wrench. The maximum
releasing torque should not exceed 50 lb-ft (67.8 Nm). If
the spring has not previously been compressed by the use
of air (6.0.1, above), verify that the service side push rod
is retracting during the process and that the release bolt
is extending from inside the spring brake housing. (DO
NOT USE A HIGH SPEED AND/OR POWER DRIVEN
IMPACT WRENCH)
6.0.9. Rotate the release bolt nut clockwise until an
increased resistance is encountered. This should indicate
that proper caging is complete. The release bolt should be
extended all the way back, as shown in Figure 4. (DO NOT
OVER TORQUE RELEASE BOLT. OVER TORQUING
CAN CAUSE SPRING BRAKE DAMAGE.)
6.0.10. Release the air pressure from the emergency/
parking port (port “12”) after caging and prior to any
disassembly or removal from the vehicle.
IMPORTANT: To ensure the power spring is fully caged,
the extended release tool length should be fully backed
out as shown in Figure 4.
WARNING!
Do not use an impact wrench. An impact wrench may
over torque the release tool and cause damage to the
pressure plate.
6.1 SPRING BRAKE CHAMBER REMOVAL
6.1.1. With the spring brake chamber caged and all air
pressure drained from the air brake system, disconnect
the air hoses from the spring brake chamber.
6.1.2. Remove the cotter pin from the yoke. Remove the
yoke pin.
6.1.3. While supporting the spring brake chamber in
position, remove and discard brake chamber mounting
nuts and washers (see Figure 3). Nuts and washers must
not be re-used. Remove the spring brake.
7. CLOCKING (ROTATING) THE
BENDIX SERVICE REPLACEMENT
SPRING BRAKE CHAMBER
NOTE: For proper installation, the service replacement
spring brake chamber may need to be clocked (rotated)
to properly position the ports or clamp band hardware.
To do so, follow the clocking procedure. Additionally,
the push rod may need to be cut to the proper length
for the application. Refer to the Bendix
®
ASA-5
®
slack
adjuster service data sheet SD-05-1269 or the Bendix
®
Versajust
™
slack adjuster service data sheet SD-05-
4630 as applicable, or see guidelines on proper push rod
lengths for use with these slack adjusters.
YOKE
WASHER