Bendix Commercial Vehicle Systems TU-FLO 750 COMPRESSOR 6/08 User Manual
Page 6
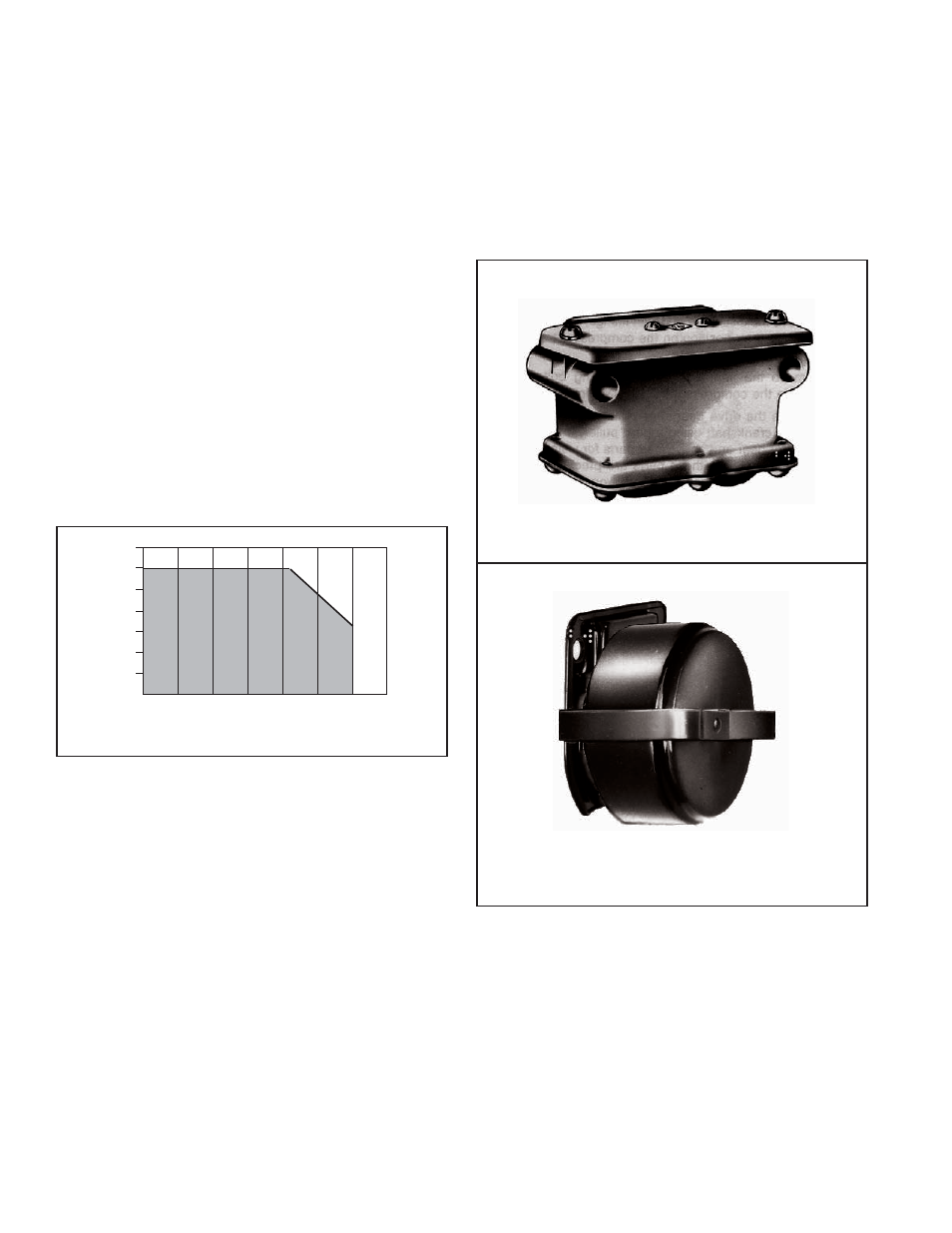
6
If a previously unturbocharged compressor is being
turbocharged, it is recommended that the inlet cavity screen
(238948) be installed with an inlet gasket (291909) on both
sides of the screen.
COMPRESSOR TURBOCHARGING PARAMETERS
Air entering the compressor inlet during the loaded cycle
must not exceed 250 degrees Fahrenheit (121 degrees
Celsius). A metal inlet line is suggested to help meet this
parameter.
The following compressor crankshaft rotative speed and
inlet pressure relationships may not be exceeded.
Crankshaft
Maximum Compressor
R.P.M.
Inlet Pressure
1900 RPM
30.0 psi (207 kPa)
2000 RPM
27.5 psi (190 kPa)
2100 RPM
24.0 psi (165 kPa)
2200 RPM
21.0 psi (145 kPa)
2300 RPM
19.0 psi (131 kPa)
2400 RPM
16.0 psi (110 kPa)
AIR INDUCTION
One of the single most important aspects of compressor
preventive maintenance is the induction of clean air.
The type and interval of maintenance required will vary
depending upon the air induction system used.
The intervals listed under the headings below pertain
to typical highway and street operation. More frequent
maintenance will be required for operation in dusty or dirty
environments.
0
20
25
15
35
5
30
900
600
10
Compressor Speed (RPM)
Inlet Pressure (PSIG)
Turbo Limits
FIGURE 9 - TURBO LIMITS CURVE
PREVENTATIVE MAINTENANCE
Regularly scheduled maintenance is the single most
important factor in maintaining the air brake charging
system. Refer to Table A in the Troubleshooting section for
a guide to various considerations that must be given to the
maintenance of the compressor and other related charging
system components.
Important Note: Review the warranty policy before
performing any intrusive maintenance procedures. An
extended warranty may be voided if intrusive maintenance
is performed during this period.
PAPER AIR STRAINER DRY ELEMENT-PLEATED
POLYURETHANE SPONGE STRAINER
FIGURE 10 - STRAINERS
POLYURETHANE SPONGE STRAINER
Every month, 150 operating hours or 5,000 miles,
whichever occurs fi rst, remove and wash all of the parts.
The strainer element should be cleaned or replaced. If the
element is cleaned, it should be washed in a commercial
solvent or a detergent and water solution. The element
should be saturated in clean engine oil, then squeezed
dry before replacing it in the strainer. Be sure to replace
the air strainer gasket if the entire strainer is removed from
the compressor intake.