Slide number 4, Automatic taper, Operation and maintenance guide – TapeTech 05TT Automatic Taper User Manual
Page 4: Better – faster – every time, Maintenance
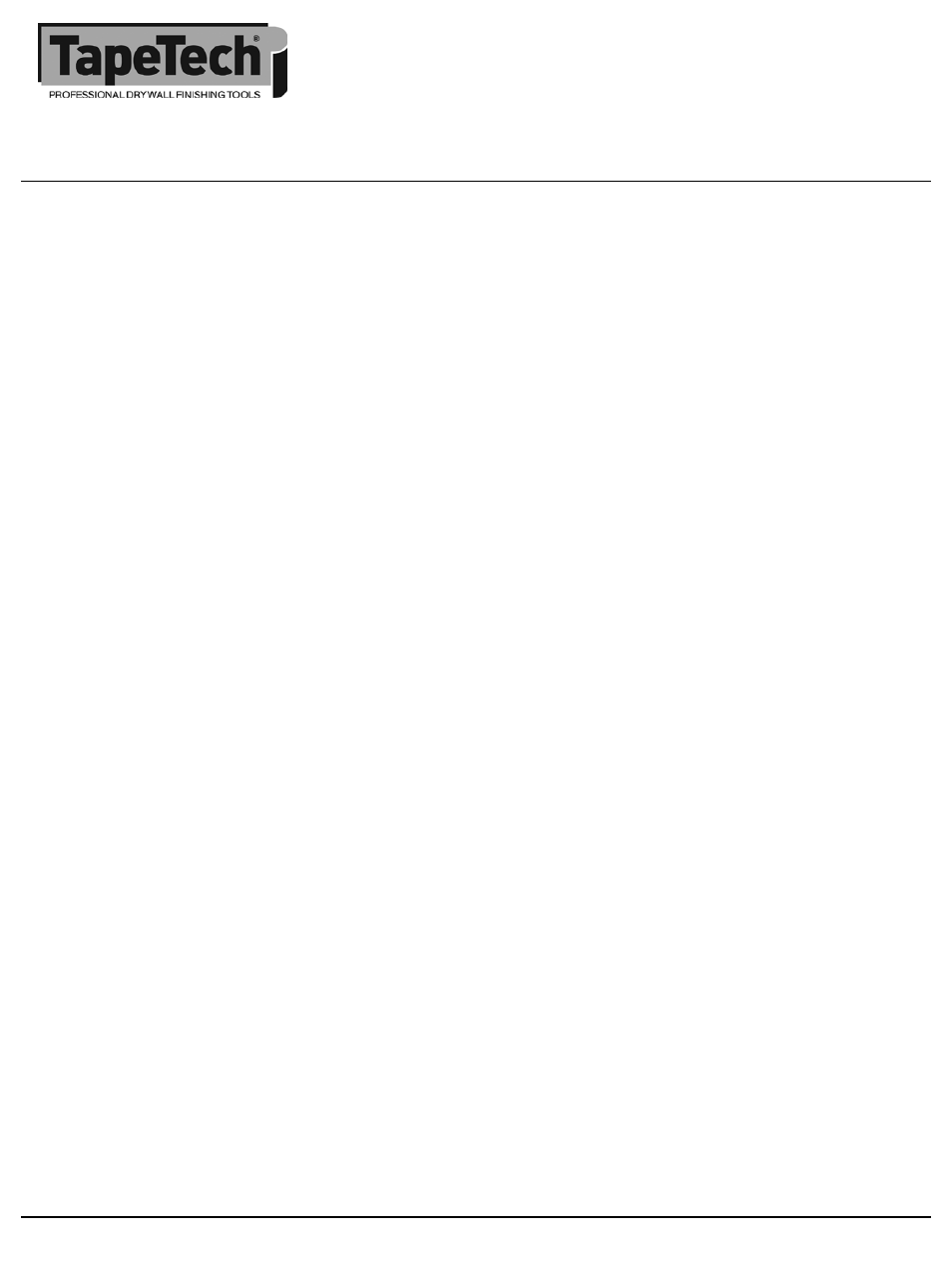
Operation and Maintenance Guide
1380 Beverage Drive, Suite W
Stone Mountain, GA 30083
1-800-426-6256 | 770-243-2323
Better – Faster – Every time
Updated 04 2012
© 2012 TapeTech Tool Co. All Rights Reserved
www.tapetech.com
To tape inside angle joints, both wheels must run in contact with the adjacent wall surfaces, bisecting the
angle with the automatic taper. Tracking must be in a straight line with the creaser wheel extended, using
the trigger located near the trailing end of the automatic taper. The extended creaser wheel secures the
tape to the angle and eases the rolling operation. Avoid twisting the taper as you move along the angle to
insure that you bisect the angle correctly. Operating the taper at a 45 degree angle to the joint, as soon
as it is practical, will aid in the prevention of the tape “creeping”.
Maintenance
This tool must be washed with a brush and water (or a water hose) after each use. Pay close attention
that all joint compound is flushed from under the cover plate and the tape advance mechanism.
Complete the clean-up by lightly oiling all wear points. Use Ames® Bazooka® Oil or any light machine oil.
Blade Replacement
1. Hold the key ring, pull down and turn key ring 90 degrees. Let the key ring slide into the cutter spring tube.
2. Pull the cutter chain until cutter block and blade are clearly in view.
3. Loosen the cutter block screw and remove the used blade.
4. Insert a new blade. Tighten the screw, making sure the blade does not protrude through the bottom of the cutter
block.
5. Pull the cutter block back into the taper head channel.
6. Pull the key ring down to the end of the spring tube. Turn it 90 degrees and lock it into the original position.
7. Pull down on the control tube to make sure the blade travels freely through the taper head channel.
Cable Replacement
1. Remove all the mud from the automatic taper.
2. Unscrew the butt ring from the bottom of the taper tube. Lightly tap tube butt ring with a screwdriver, if
necessary.
3. Remove the cover plate by taking out the top screws and loosening the side and bottom screws. Gently pull the
cover plate up and out to remove it. Close the gate valve and force the piston down with a thin piece of wood or a
flattened piece of corner bead.
4. Loosen the screw on the cable drum and remove the end of the cable from the drum.
5. Remove the cable from the piston by removing the nut from the slotted stud.
6. Clean the slotted stud of any mud, then thread the cable through the nut while holding it, and place the end of
the cable into the slot. Screw the nut onto the slotted stud and tighten, to secure the cable to the piston.
7. Drop the loose end of the cable into the tube followed by the piston. Replace the butt ring and the screws.
8. Make sure the slot in the cable drum is clean and insert the loose end of the cable and tighten the screw.
9. Wind the cable onto the cable drum by turning the drum key clockwise.
10. Replace the cover plate and tighten all screws.
Gooser Needle Replacement
Holding onto the gooser needle assembly, loosen the screw and remove the gooser needle. Slide the entire gooser
assembly to the bottom of the tape guide. Push the new gooser needle through the hole and out the bottom so
that the point of the needle protrudes 1/16 inch (1.5 mm) through the tape in the slide. Hold the support assembly
and tighten the screw. Insert tape through the tape guide and check for proper advancement of the tape.
Automatic Taper