S&S Cycle Pistons User Manual
Page 3
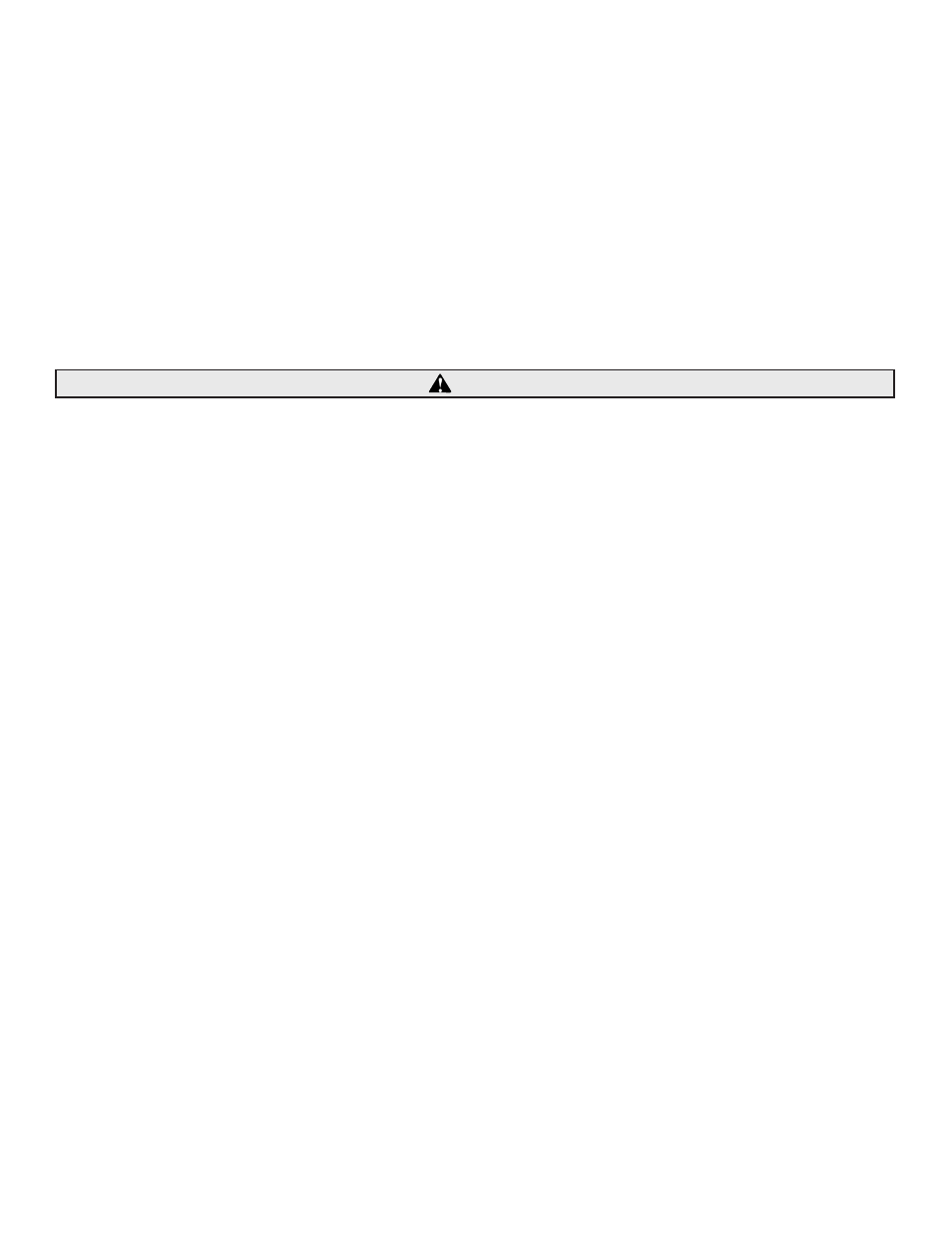
3
PISTON INSTALLATION
1- Piston Series 92-1600, 92-1620, 92-1630, 92-1640, 92-2400, 92-2420, 92-2440, 92-2460, 92-2700, 92-2720 and 92-2730 have offset wristpins
and must be installed with dimple in piston dome toward right or cam side of engine. Piston Series 92-1060, 92-1070 and 92-1080, 92-1210,
92-1550, 92-1556, 92-1560 also have offset wristpins and must be installed with symbol fiCAM toward right or cam side of engine.
2- Piston Series 92-3500, and 92-3700 have larger intake valve reliefs which must be installed toward intake valves or middle of engine.
3- Most other pistons have no special features. They can be installed as desired unless piston skirt has piston-to-piston clearance bevel on one
side. In such case, bevel must face center of engine. If only one piston has bevel, it will be for rear cylinder. See #4 immediately below.
4- Some piston sets have all piston-to-piston clearance machined into rear piston. In such cases rear piston must be installed with bevel or notch
toward front. If dimple is present, piston must be installed with dimple in correct position. The dimple in the ring should face down and be
installed in the gap above the wrist pin. This dimple keeps the support rail from rotating.
5- Check all installations for minimum of .060" clearance between pistons at closest point near bottom of stroke.
6- Check all installations for minimum of .060" clearance between pistons and flywheels at bottom of stroke. Replacement pistons may or may not
have adequate clearance. Compare replacement pistons with ones being replaced and make corrections accordingly.
NOTE: In all cases it is the engine builder's responsibility to confirm proper clearances when assembling an engine. This is especially critical with performance
components such as higher compression pistons and high lift camshafts. In addition to clearances mentioned, .060" valve-to-piston clearance must be confirmed.
Failure to establish proper clearances can result in severe engine damage not covered under warranty.
WRISTPIN RETAINER INSTALLATION
NOTE: Thoroughly clean wristpin before installation, paying particular attention to bore. Pass clean, lint-free cloth back and forth through wristpin bore
several times to insure removal of contaminants.
1- If wristpin clips are used, insure that groove in piston is free of burrs and foreign matter.
2- Round "wire" style clips identical to and interchangeable with stock Harley-Davidson® Evolution® clips require wristpins with specially chamfered
ends. Install wire clips using procedure recommended in a Harley-Davidson® service manual. End of clip must rest over notch in piston below
wristpin hole to allow removal of clip in future. Be sure clip is fully seated in groove.
NOTE: Round "wire" style clip ends must be deburred before installation.
3- "Tru-Arc" style clips should be installed with proper tool. Clips should not be used with wristpins having chamfer on end greater than 1⁄64". Install
clip with open side facing downward and sharp edge of clip to outside of wristpin hole away from wristpin. Be sure clip is fully seated in groove.
4- "Spiral-Loc" style clips are installed by slowly working clip into wristpin hole using thumb nail, small screwdriver or awl in circular turning
motion. Once entire clip is in hole, push end of clip into groove, followed by rest of clip. Be sure clip is fully seated in groove.
5- PTFE wristpin buttons must be used only in pistons where buttons are fully supported in wristpin hole. Buttons are used in place of and not
in conjunction with conventional wristpin clips. Recommended wristpin endplay is .010" to .060" and is determined by subtracting length of
wristpin with button on each end from finished cylinder bore.
To make fitting easier, S&S® buttons come in four widths. "A" buttons are thinnest and "D" buttons are thickest. Use two A buttons, Part 94-9251,
for bore sizes 37⁄16" std. to 37⁄16" +.040, two B buttons, Part 94-9252, for bore sizes 37⁄16" +.050 to 37⁄16" + .090, two C bottoms. Part #94-9258, for
bore sizes 35⁄8" std. to 35⁄8" +.030, and two D buttons, Part 94-9259, for bore sizes 35⁄8" +.040 to 35⁄8" +.070.
6- Special notched aluminum buttons are supplied with Piston Series 92-3500 and #92-3700. When installed, notch simulates oil ring groove and
helps support oil ring. Buttons should not protrude beyond ring land diameter when in place.
RING INSTALLATION
1- Ring widths on some piston series have changed from time to time. Part numbers of rings originally supplied with pistons should be recorded
for future reference in the event replacement rings are required.
2- The majority of ring kits presently supplied by S&S® contain a moly faced top ring, a cast, reverse torsion second ring, and a three piece oil ring.
This may be confirmed as follows:
A- Top compression ring has a gray finish that is relatively light in color, and may or may not have a slight bevel along the inner edge. It has no
dot or other identifying mark. The light color can best be recognized by comparing compression rings to each other beneath a good light.
Install light colored ring without dot in top groove, bevel up. If there is no bevel, ring can be installed either side up.
B- Second compression ring has a darker, charcoal gray finish and slight bevel along inner surface. This ring has a dot. See Figure 1. Install in
second or middle groove with dot up.
C- Oil rings are three piece type with two rails and one expander. Do not shorten expander for any reason! Installation is straightforward with
one rail placed above expander, other rail below expander. Rails may be shortened to correct gap, but burrs must be carefully removed.
NOTE: In some cases, same expander is used for several bore sizes. Oversize rings will not necessarily have a larger expander
CAUTION