S&S Cycle Big Bore Kits 97 & 106 for 1999–06 & 2007–Up Big Twins User Manual
Page 4
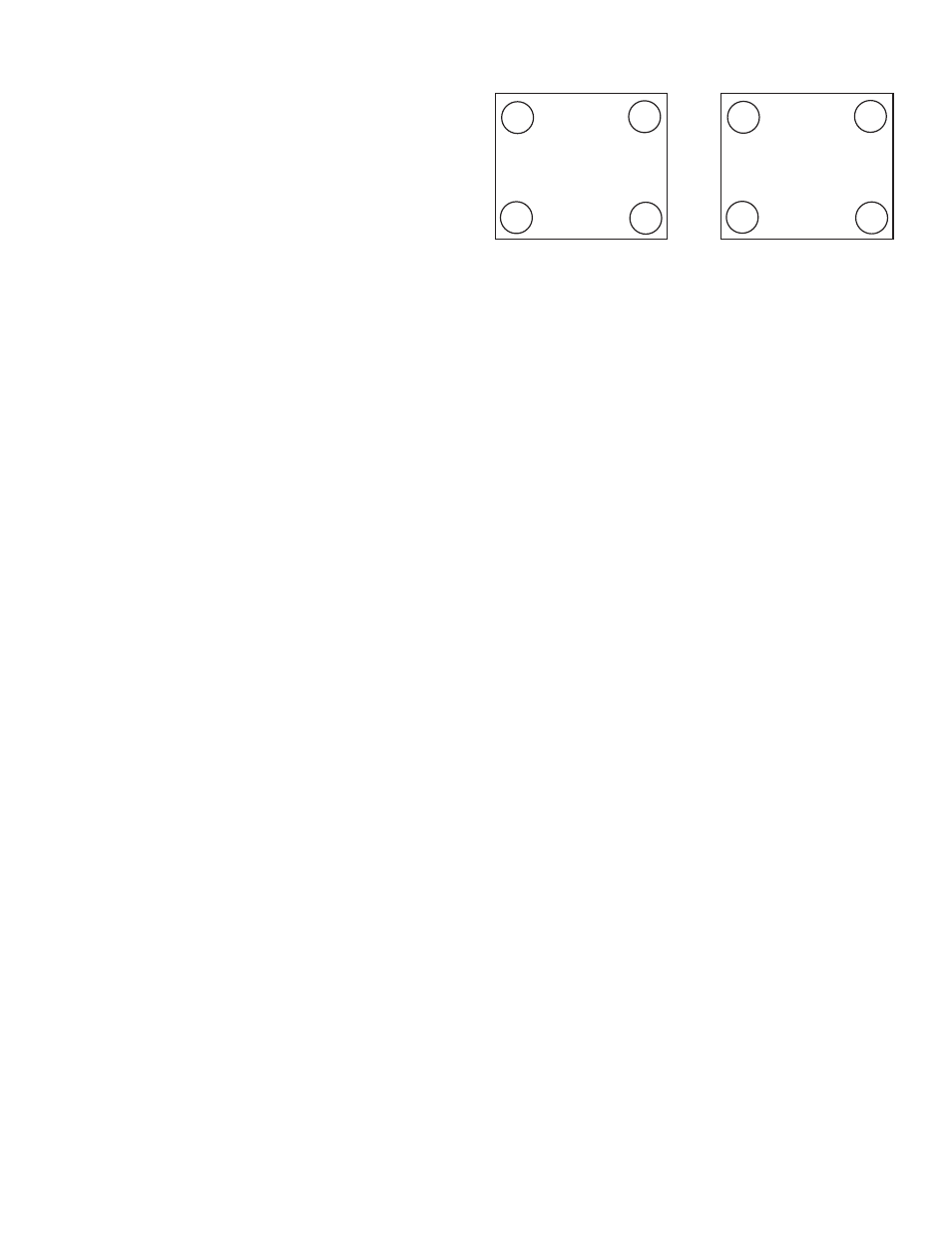
4
5- Hold the piston over the connecting rod with the piston facing the
correct direction and the piston pin bore and upper bushing bores
lined up.
6- Install the piston pin through the piston pin bore and through the
connecting rod bushing until the pin contacts the clip.
7- Install the other piston clip with the opening facing up. Ensure
that both clips are fully seated.
8- Repeat procedure for the rear piston.
D- Cylinder Installation
2- Bring the front cylinder to TDC.
3- Apply a light coating of oil to the piston and rings.
4- Install the cylinder base o-ring on the cylinder.
5- Lightly oil the new o-rings for the lower cylinder deck alignment
dowels and install.
6- Verify that the ring gaps are orientated correctly, refer to Picture
5a, page 3.
7- Remove the rubber tubing from the cylinder studs.
8- Compress ring pack by using a suitable ring compressor. If
possible, position the ring compressor so that you can see the oil
expander gap during installation. Picture 5b, page 3.
9- Install cylinder on piston, making sure not to overlap oil ring
expander.
10- Remove ring compressor.
11- Remove plastic sheeting covering crankcase.
12- Slide the cylinder down until it seats against the crankcase.
13- Rotate the engine until the rear cylinder is at TDC.
14- Repeat procedure for the rear cylinder.
E- Cylinder Head Installation
Head Gasket Tightening Torque Specifications
Multi layer steel (MLS) head gasket, PN 106-3714, 3.927" bore.
1- Check surfaces for flatness and imperfections, an excessively
rough finish may cause gasket failure.
2- Check all hardware for defects. Clean all threads and lubricate
with clean oil. Lubricate the underside flange of the head bolts
with clean oil (wipe away excess).
3- The head bolts are two different lengths. The short ones go on
the spark plug side; the long ones go on the pushrod side.
4- Place the head gasket on the cylinder and locate the gasket
using the cylinder head alignment dowels. Either face of the
gasket can be up, there is not a specific top or bottom to the
gasket.
NOTE: Do not use the cylinder head alignment dowel O-rings with MLS
head gasket.
5- Once the gasket is in place, make sure that it fits the bore. The
gasket should not hang into the bore or combustion chamber
area.
6- If using cylinder heads other than stock, check the brass rivets
of the MLS gaskets to ensure the rivets do not interfere with the
sealing surface in any way.
7- Important! In order to properly seal the head gasket, the head
bolts must be torqued in the sequence shown in the next step,
fully loosened, then torqued again a 2nd time. Follow the head
tightening sequence in the next step then fully loosing the head
bolts ¼ turn at a time in the sequence shown in Picture 6 until
fully loose. Repeat the tightening sequence in step 8 a second
time.
8- Tighten the head bolts according to the following procedure,
start with the front head then the rear head.
a- Tighten each bolt finger tight using the sequence in Picture
6, top right.
b- Tighten each bolt to 10-12 ft-lbs using the sequence.
c- Tighten to 15-17 ft-lbs using the sequence.
d- Finally, tighten the bolts an additional ¼ turn (90 degrees).
F- Final Assembly
Assemble the remaining items according to the Harley-Davidson
service manual specific for your motorcycle.
G- Tuning
S&S big bore kits increase the displacement and compression ratio of
your engine. The fuel and ignition systems must be calibrated for these
changes before the engine is driven and break-in is attempted. It is
recommended that a performance carburetor such as the S&S Super E
or G be used with the correct jetting for the engine size for carbureted
models. Fuel injected engines must be tuned using a replacement
ECU such as the S&S VFI module, or an aftermarket tuner such as the
DynoJet® Power Vision® tuner.
NOTE: The S&S VFI module is not compatible with 2008–up Touring
models with electronic throttle control. S&S recommends the Dynojet®
Power Vision® tuner for these applications.
BREAK-IN PROCEDURE
NOTES:
•
S&S engines and parts are designed for high performance and are not
as tolerant of inadequate break-in. Correct break-in will assure longer
engine life and will prevent unnecessary engine damage. Engine damage
caused by improper break-in is not covered under the S&S Warranty.
•
Proper engine tuning will be required in order for your engine to run
correctly and to prevent damage. Carbureted engines must be rejetted,
and a larger carburetor is recommended. EFI calibration can be changed
with the use of an S&S VFI module or other aftermarket tuner. It is
recommended to start by adding 10% fuel across the map if you do not
have a tune file for the set-up you are running. Check the S&S website for
Power Vision calibration files.
1- Initial start up. Run the engine approximately one minute at
1250-1750rpm. DO NOT crack the throttle or subject to any loads
during this period as head gaskets are susceptible to failure at
this time. During this time, check to see that oil pressure is
normal, oil is returning to the oil tank and no leaks exist.
2- Shut off engine and inspect for leaks. Allow engine to cool to the
touch.
3- Start up engine again and allow the engine to warm up for 3 to 4
minutes. Again, do not crack the throttle or subject the engine to
any type of load. Shut down the engine and allow to cool. Repeat
this procedure at least 3 more times.
4- After the engine has cooled to room temperature, you are ready
to start the 500 mile engine break-in process.
5- The first 50 miles are the most critical for new rings and piston
break-in. Engine damage is most likely to occur during this
period. Keep heat down by not exceeding 2500rpm. Avoid
lugging the engine, riding in hot weather or in traffic. Vary the
engine speed. We recommend changing the oil after the first 50
miles.
6- The next 500 miles should be spent running no faster than
3500rpm or 60mph. Avoid running continuous steady speeds,
and do not lug the engine, Vary the rpm. We recommend
changing the oil again at 500 miles.
3
4
1
2
4
3
2
1
Cam Side
Drive Side
Picture 6
REAR CYLINDER
FRONT CYLINDER
Head Bolt Tightening Sequence