Introduction, Functional description, Introduction 13 – MTS Series 201 Actuators User Manual
Page 13: Functional description 13
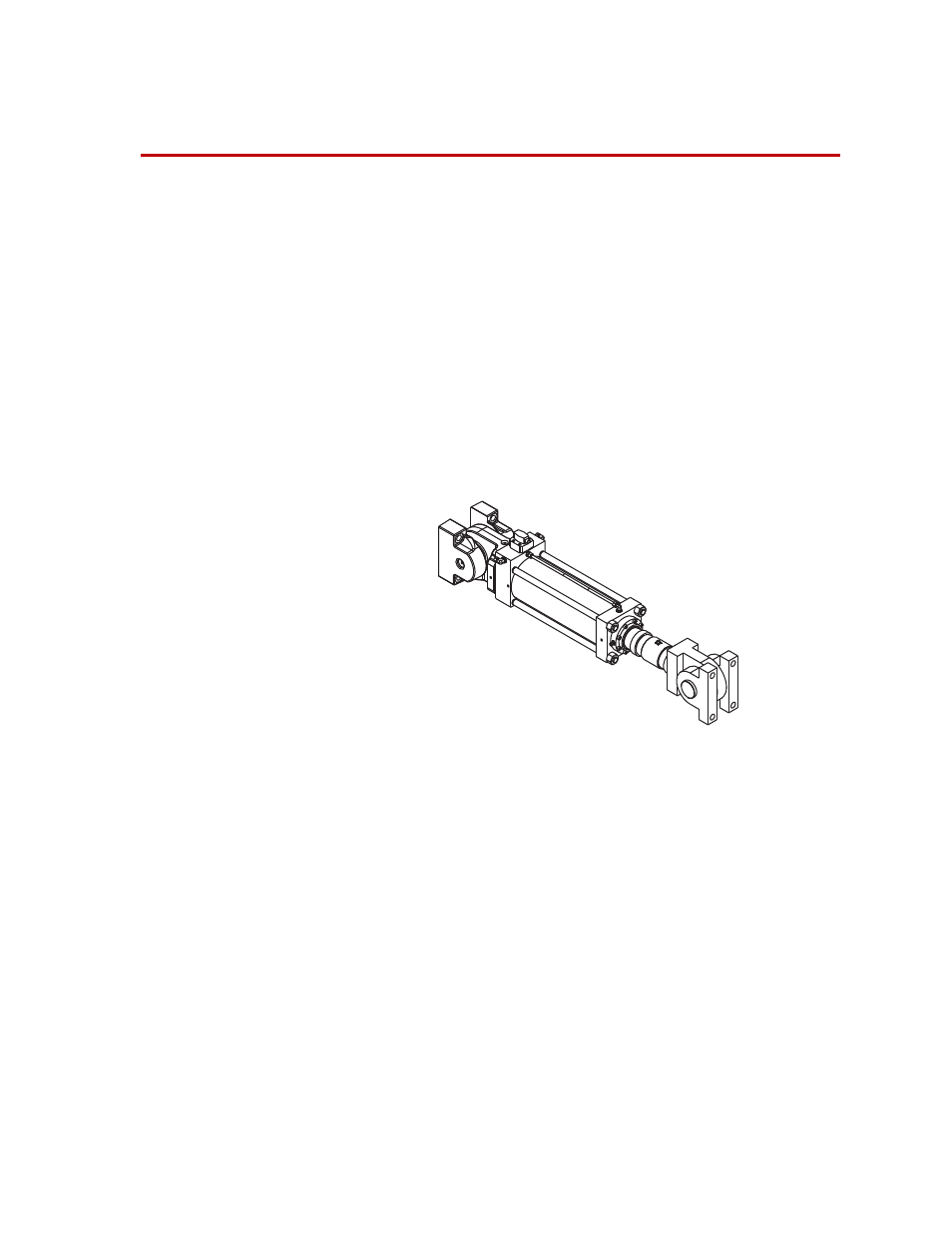
Functional Description
Series 201 Actuator Product Information
13
Introduction
This section contains the functional description of the MTS Series 201 Hydraulic
Actuator and a description of the actuator components. It also contains the
actuator specifications such as model numbers, force ratings, dimensions,and
weights.
Functional Description
The Series 201 Hydraulic Actuators are heavy duty, fatigue-rated force
generation components. Designed for service to a maximum operating pressure
of 21 MPa (3000 psi), this actuator series is available in 11 different force ratings
from 7 to 400 kip tension (32 to 1770 kN). They are single-ended, heavy-duty
actuators that operate under precision servovalve control in MTS closed-loop
servohydraulic systems. When equipped with the appropriate options and
accessories, the actuators can be configured for precision testing of materials,
structures, and components.
Series 201 Hydraulic Actuators are designed to accept a wide variety of options
and accessories including force and displacement transducers, swivel rod ends,
and swivel bases. Series 201 Hydraulic Actuators are specifically designed and
manufactured to meet the needs of precision static and low frequency dynamic
testing applications.
Actuator mounting
The actuator can be mounted to a wide variety of fixtures and assemblies.
Component test systems usually have one end of the actuator connected to a
custom test frame base and the other end connected to the test specimen.
Either end of the actuator can use mounting fixtures (such as swivels) to
attach it to the specimen or base.
Actuator operation
Actuator piston rod movement is accomplished by supplying high-pressure
hydraulic fluid to one side of the actuator piston and opening the other side to a
return line. High-pressure hydraulic fluid is ported into the cylinder through the
retraction port or the extension port. The differential pressure across the piston
forces the piston rod to move. The amount of hydraulic fluid and the speed and
direction of piston rod movement is controlled by a servovalve.