Burnham FCM120 User Manual
Page 41
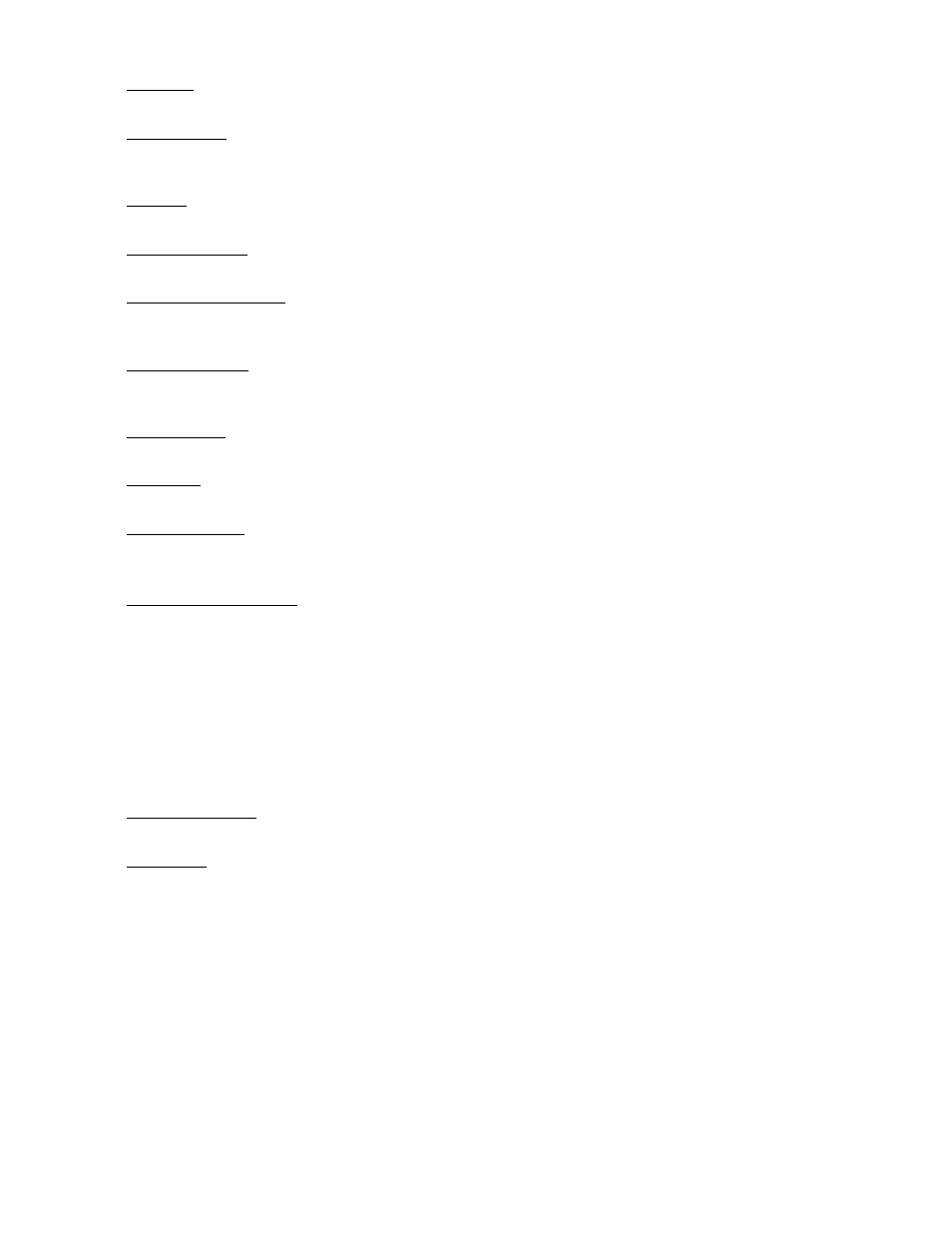
41
2) Circulator (Required) - Usually at least two circulators will be required to properly install a FCM Series boiler. See the
previous section for information on sizing the circulators.
3) Expansion Tank (Required) - If this boiler is replacing an existing boiler with no other changes in the system, the
old expansion tank can generally be reused. If the expansion tank must be replaced, consult the expansion tank
manufacturer’s literature for proper sizing.
4) Fill Valve (Required) - Either a manual or automatic fi ll valve may be used. The ideal location for the fi ll is at the
expansion tank.
5) Automatic Air Vent (Required) - At least one automatic air vent is required. Manual vents will usually be required in
other parts of the system to remove air during initial fi ll.
6) Manual Reset High Limit (Required by some codes) - This control is required by ASME CSD-1 and some other codes.
Install the high limit in the boiler supply piping just above the boiler with no intervening valves. Set the manual reset
high limit to 200°F. Wire the limit per Figures 10.1 & 10.2 in the Wiring section.
7) Flow Control Valve (Required) - The fl ow control valve prevents fl ow through the system unless the circulator is
operating. Flow control valves are used to prevent gravity circulation or “ghost fl ows” in circulator zone systems
through zones that are not calling for heat.
8) Isolation Valves (Recommended) - Isolation valves are useful when the boiler must be drained, as they will eliminate
having to drain and refi ll the entire system.
9) Drain Valve (Required) - The drain valve is installed on the return tee located in the lower vestibule compartment as
shown in Figure 9.2.
10) Low Water Cut-off (Required) - The low water cut-off supplied with this boiler must not be removed.
D. Piping for Special Situations
1) Systems containing oxygen - Many hydronic systems contain enough dissolved oxygen to cause severe corrosion
damage to an aluminum boiler such as the FCM. Some examples include:
• Radiant systems that employ tubing without an oxygen barrier.
• Systems with routine additions of fresh water.
• Systems which are open to the atmosphere.
If the boiler is to be used in such a system, it must be separated from the oxygenated water being heated with a heat
exchanger as shown in Figure 9.10. Consult the heat exchanger manufacturer for proper heat exchanger sizing as well as
fl ow and temperature requirements. All components on the oxygenated side of the heat exchanger, such as the pump and
expansion tank, must be designed for use in oxygenated water.
2) Piping with a Chiller - If the boiler is used in conjunction with a chiller, pipe the boiler and chiller in parallel as shown in
Figure 9.11. Use isolation valves to prevent chilled water from entering the boiler.
3) Air Handlers - Where the boiler is connected to air handlers through which refrigerated air passes, use fl ow control
valves in the boiler piping or other automatic means to prevent gravity circulation during the cooling cycle.