Cirrus Logic CS5529 User Manual
Page 2
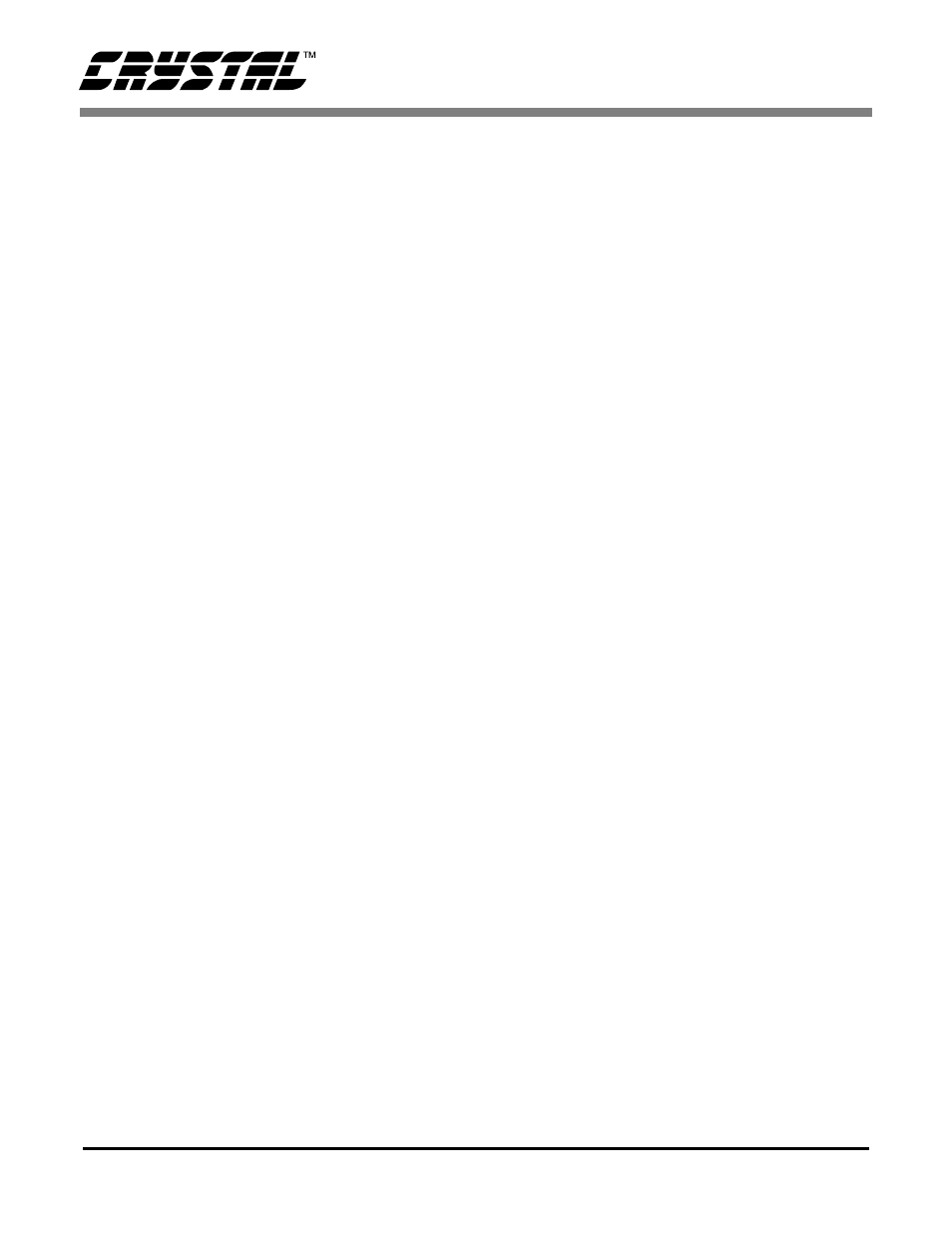
CS5525/6/9 FAQ
2
DS202TB1
(25 mV, 55 mV, 100 mV), the input current is
fVosC (where Vos is the offset of the instru-
mentation amplifier, typically less than 40 mV,
f is the chopping frequency, either 256 or
32,768, and C is 2 pF). A typical input current
for the lower ranges is 100 pA. For the higher
ranges (1 V, 2.5 V, and 5 V), the input current
is [(VAIN+)-(VAIN-)]fC where (VAIN+)-
(VAIN-) is the voltage between AIN+ and
AIN-, f is either 256 or 32,768, and C is 32 pF.
A typical input current for the higher ranges is
1.2
µ
A/V.
8) When reading the conversion data I get all ze-
roes no matter what the analog signal is. Please
explain why.
Check the voltage between pins 19 and 20
(VREF+ and VREF-). If it is zero, the converter
will compute all zeros because the digital out-
put word represents the ratio of the input signal
to the voltage reference.
9) Is calibration required to use the converter?
When the CS5525/26 is reset, the registers are
set to known values. If the signal to be mea-
sured by the converter is within the nominal
range, the converter can perform conversions
without the need for calibrations. Errors in the
system remain present when calibration is not
performed, however, this may be acceptable if
the errors are insignificant to the measurement
or if the errors are removed by some other
means, such as software and registers in the mi-
crocontroller.
10) How often do I need to recalibrate?
To answer this question one must ask: 1) What
accuracy is required from the A/D converter?
2) What effects will temperature changes have
upon the entire circuit, including components
outside the A/D? To obtain optimum calibra-
tion accuracy, a calibration should be per-
formed approximately one minute after power
is applied to allow the chip to reach thermal
equilibrium.
A higher accuracy measurement requirement
will generally require calibrations more often,
because, after the initial calibration has been
performed, the converter is subject to some
drift if the operating temperature changes. Typ-
ical offset drift and gain drift are given in the
data sheet tables. The observed drift in the ap-
plication circuit may be considerably greater
due to parasitic thermocouple effects and gain
drift caused by the limited tempco tracking of
the external resistors. Once an estimate of drift
is determined for the entire application circuit
(drift will usually be dominated by error sourc-
es external to the converter), an assessment of
how it affects measurement accuracy as tem-
perature changes can be made. Once the
amount of drift is known, you can determine if
a new calibration is required. A good rule of
thumb is to recalibrate the converter (or sys-
tem) with every ten degrees of ambient temper-
ature change.
11) What do the numbers in the calibration regis-
ters actually mean?
There are two internal read/write calibration
registers in the CS5525/26 (offset, and gain).
One LSB in the offset register is 2
-24
proportion
of the input span (bipolar span is 2 times the un-
ipolar span). The MSB in the offset register de-
termines if the offset that is to be trimmed is
either positive or negative. The converter can
typically trim ±50% of the input span. The gain
register spans from 0 to (2 - 2
-23
). The decimal
equivalent meaning of the gain register is:
D = b
0
2
0
+ b
1
2
-1
+ b
2
2
-2
+ b
3
2
-3
+ ... + b
N
2
-N
where the binary numbers have a value of either
zero or one. After a gain calibration has been
performed, the numeric value in the gain regis-
ter should not exceed the range of 0.5 to 2.0
(decimal) [400000(Hex) to FFFFFF(Hex)].