Instruction manual ni-221e – WIKA MAB User Manual
Page 5
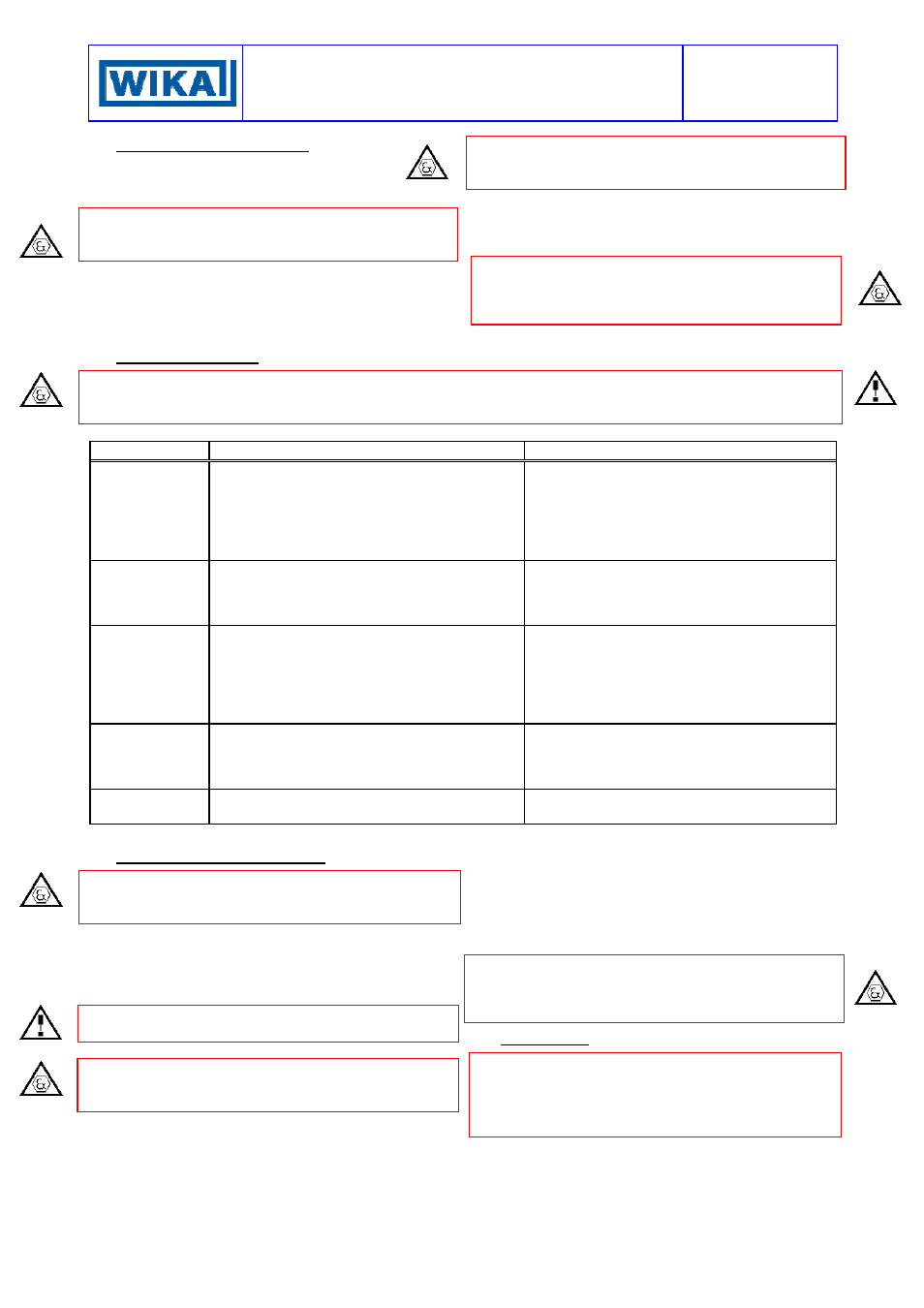
INSTRUCTION MANUAL
NI-221E
Rev. 1 11/02
9 FUNCTIONAL
VERIFICATION
This will be carried out according to the Client’s control
procedures. Series MW and MWH instruments can be
verified on the plant if installed as illustrated in Fig. 7 e 8.
The instruments Series MA may be checked on site only if
apparatus suitable for explosive atmospheres are used
and provided that the electric line is not energized.
If this is not the case it is necessary to stop operation,
dismount by means of the three-piece joints and carry out
the verification in a test room.
CAUTION: do not open the cover of explosionproof pres-
sure switches (Series MA) when energized, in explosive
atmospheres.
Verification consists in checking the calibration values
and possibly regulating the adjustment screw (see §4 )
Verification consists in checking the calibration value
and possibly regulating the adjustment bush (see §5).
In case of explosionproof instruments (Series MA), in-
spections of the electrical installation are to be carried out
also according to customer procedures and at least in
accordance with Standard EN-60079-17.
10 TROUBLESHOOTING
IMPORTANT NOTE: operations involving replacement of essential components must be carried out at our work-
shop, especially for instruments with explosionproof certificate; this is to guarantee the user the total and cor-
rect restoration of the product original characteristics.
MALFUNCTION PROBABLE
CAUSE
REMEDY
Set point shift
Permanent deformation of the sensitive ele-
ment due to fatigue or non-tolerated overages.
Variation of the elastic features of the sensitive
element due to its chemical corrosion.
O-ring wear (only MWH and MAH)
Recalibrate or replace the sensitive element.
Recalibrate or replace the sensitive element
with another made of a suitable material. If
necessary apply a fluid separator.
Replace the piston subgroup and recalibrate.
Poor repeatabil-
ity
O-ring wear (only MWH and MAH)
Air bubbles or condensation (only for types
with pressure <1 bar).
Replace the piston subgroup and recalibrate.
Drain the process connection line and if
necessary modify it.
Slow response
Clogged or obstructed connection line.
Root valve partially closed.
Too viscous fluid.
Check and clean line.
Open valve.
Provide instrument with suitable fluid separa-
tor.
No actuation or
undue actuation
Root valve closed.
Microswitch contacts damaged.
Loosened electrical joints.
Interrupted or short-circuited electrical line.
Open the valve.
Replace the Microswitch.
Check all electrical joints.
Check the conditions of the electrical line.
Undue actua-
tion
Accidental shocks or excessive mechanical
vibrations.
Modify the mounting.
11 STOPPING AND DISMOUNTING
Before proceeding with these operations ensure that the
plant or machines have been put into the conditions
foreseen to allow these operations.
With reference to Figures 7 e 8
Remove the power supply (signal) from the electrical line.
Close the root valve (6) and open the drain. Remove the
plug (2), open the valve (3) and wait until the process fluid
has drained from the tubing through the drain.
Do not dispose of the process fluid into the environment, if
this can cause pollution or damage to people.
Unscrew the three-piece joint (8).
CAUTION: do not open the cover of explosionproof pres-
sure switches (Series MA) when energized, in explosive
atmospheres.
Unscrew the three-piece joint (10) (electrical cable tubing).
Remove the instrument cover and disconnect the electrical
cables from the terminal block and earth screws.
Remove the screws fixing the case to the panel (or pipe)
and remove the instrument, taking care to slide the electri-
cal conductors out from the case. Mount instrument cover.
Insulate and protect cables around, if any. Temporarily
plug pipes not connected to the instrument.
In case of explosionproof instruments (Series MA) it is
recommended to follow - at least – the standard EN-
60079-17 for the withdrawal from service of electrical
apparatus.
12 DEMOLITION
The instruments are mainly made of stainless steel and
aluminium and therefore, once the electrical parts have
been dismounted and the parts coming into contact with
fluids which could be harmful to people or the environment
have been properly dealt with, they can be scrapped.