Nor-Lake Stability Chambers User Manual
Page 8
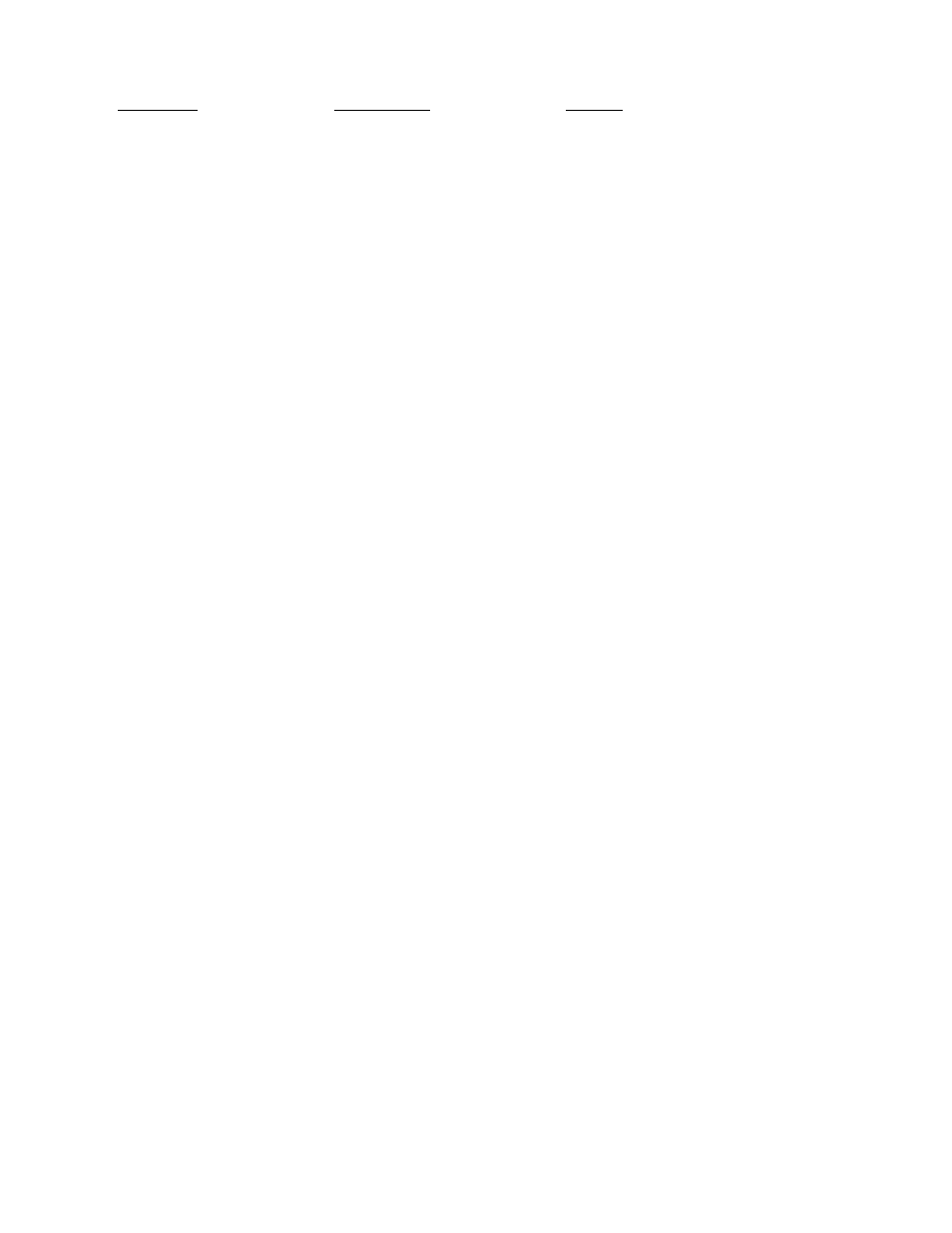
- 8 -
MALFUNCTION POSSIBLE
CAUSE SOLUTION
Compressor will not start -
1. Service cord unplugged
1. Plug in service cord
no hum
2. Fuse blown or removed
2. Replace fuse
3. Overload tripped
3. Determine reasons and correct
4. Control stuck open
4. Repair or replace
5. Wiring incorrect
5. Check wiring against the diagram
Compressor will not start -
1. Improperly wired
1. Check wiring against the diagram
hums but trips on overload
2. Low voltage to unit
2. Determine reason and correct
protector 3.
Starting
capacitor defective
3. Determine reason and replace
4. Relay failing to close
4. Determine reason, correct or replace
Compressor starts and runs,
1. Low voltage to unit
1. Determine reason and correct
but short cycles on overload
2. Overload defective
2. Check current, replace overload protector
protector
3. Excessive head pressure
3. Check ventilation or restriction in
refrigeration
system
4. Compressor hot-return gas hot
4. Check refrigerant charge, fix leak if
necessary
Compressor operates long
1. Short of refrigerant
1. Fix leak, add refrigerant
or continuously
2. Control contact stuck
2. Repair or replace
3. Evaporator coil iced
3. Determine cause, defrost manually
4. Restriction in refrigeration
4. Determine location and remove restriction
system
5.
Dirty
condenser 5.
Clean
condenser
Compressor runs fine, but
1. Overload protector
1. Check wiring diagram
short cycles
2. Cold control
2. Differential too close - widen
3.
Overcharge
3. Reduce
charge
4. Air in system
4. Purge and recharge
5. Undercharge
5. Fix leak, add refrigerant
Starting capacitor open,
1. Relay contacts stuck
1. Clean contacts or replace relay
shorted or blown
2. Low voltage to unit
2. Determine reason and correct
3.
Improper
relay
3.
Replace
Relay defective or burned out
1. Incorrect relay
1. Check and replace
2. Voltage too high or too low
2. Determine reason and correct
Refrigerated space too warm
1. Control setting too high
1. Reset control
2. Refrigerant overcharge
2. Purge refrigerant
3.
Dirty
condenser 3.
Clean
condenser
4. Evaporator coil iced
4. Determine reason and defrost
5.
Not
operating
5.
Determine
reason, replace if necessary
6. Air flow to condenser or
6. Remove obstruction for free air flow
evaporator
blocked
Standard temperature system
1. Control setting is too low
1. Reset the control
freezes the product
2. Control points stuck
2. Replace the control
Objectionable noise
1. Fan blade hitting fan shroud
1. Reform or cut away small section of shroud
2. Tubing rattle
2. Locate and reform
3. Vibrating fan blade
3. Replace fan blade
4. Condenser fan motor rattles
4. Check motor bracket mounting, tighten
5.
General
vibration
5.
Compressor suspension bolts not loosened
on applicable models - loosen them
6. Worn fan motor bearings
6. Replace fan motor
Pan Area
1. No cooling
1. Make sure switch is in the "on" position
2. Too cold
2. Adjust temperature control - see instructions
under pan area
3. Too warm
3. Adjust temperature control - see instructions
under pan area
Failure to Heat
1. Manual overload tripped
1. Push reset on hi-limit switch
2. Incorrect setting
2. See control manual
3. Alarm enabled
3. See control manual
Humidity level not correct
1. Water supply interrupted
1. Check water supply
2. Clean Humidifier
2. Incorrect control settings
1. See control manual
3. Piping not connected / sealed
1. Connect tubing
2. Seal
joints
4. No power to humidifier
1. Check power connections for humidifier
5. Unable to maintain higher humidity levels 1. Remove
restriction
on humidity output spout
6. Unable to maintain humidity tolerance. 1.
Confirm
humidity restrictor is properly positioned in output
Spout
7. Humidity range to high or low
1. Modify humidity ON/OFF parameters
2.
Modify
dehumidification ON/OFF parameters