Part 1 installation – Midco DS24A User Manual
Page 2
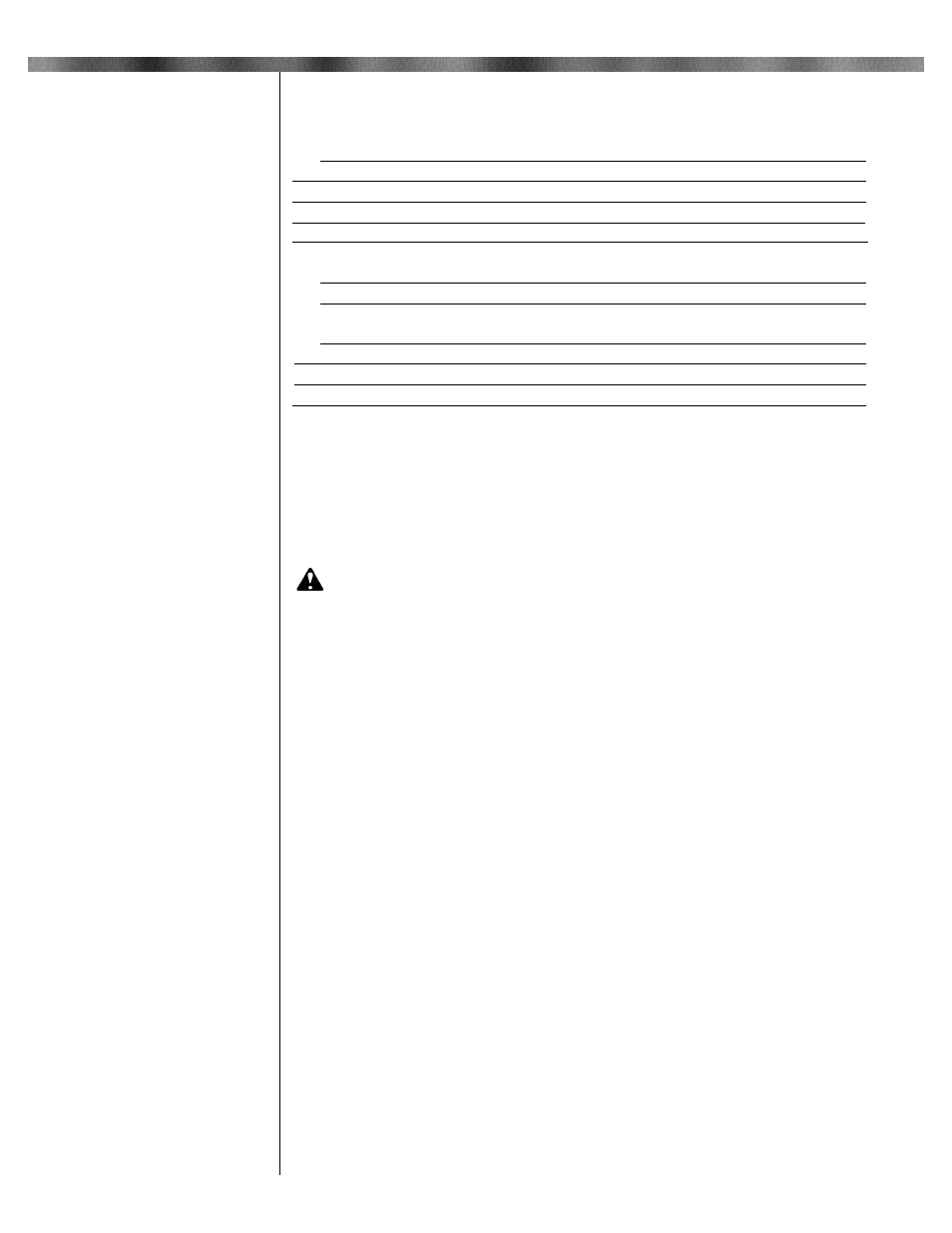
Part 1 Installation
Specifications
I Ventilation
II Preparation of the Gas
Utilization Equipment
III Combustion Chamber
NATURAL or PROPANE Gas
Air Delivery
(Approximate air delivery at zero draft)
Maximum Firing Rate**
Minimum Firing Rate**
Tube Diameter
Tube Length
Minimum Combustion Chamber Size
225 MBH
150 MBH
Gas Pressure Required
NATURAL or PROPANE
Standard Voltage
Flame Safety
Main Automatic Valve
47 SCFM*
225 MBH***
50 MBH***
4 inches
8 inches
7" W x 11" L or 10" dia.
6" W x 10" L or 9" dia.
5.0" to 14.0" W.C.
120 Volts 60 Cycle
Direct Spark Ignition of Main Flame, Electronic Safety
3 Function Redundant
Notes:
*
SCFM=Standard Cubic Feet/Minute
**
Ratings based on 1,000 BTU/cu. ft. NATURAL, 2500 BTU/cu. ft. PROPANE at Sea Level.
***
1 MBH=1,000 BTU/Hr.
One gallon of fuel oil=140,000 BTU.
Derate burner for altitudes over 2,000 feet by 4% for each 1,000 feet of additional elevation.
CAUTION: The ECONOMITE DS24A is not intended for outdoor installation and must
be protected from excessive moisture. Provide adequate clearance for service and proper
operation.
If the former automatic oil burner gave trouble-free operation, it is probable that the gas utiliza-
tion equipment area has sufficient infiltration of air for combustion and dilution of flue gases.
Nevertheless, the area must be checked:
■
■
■
■
Open basement or utility areas of normal construction, without storm windows or tight doors,
will generally allow sufficient air infiltration. However, if the gas utilization equipment is located in
a tight or separate room, ventilation to an open area as described above will be required. Install
two permanently open grilles, each sized on the basis of one square inch free area per 1,000 BTU
(but not less than 100 square inches) of the total input rating of all gas utilization equipment in
the confined space. One grille should be located within 12 inches of the ceiling, the other within
12 inches of the floor.
■
■
■
■
If the gas utilization equipment is located in an area of unusually tight construction, or if an
exhaust fan, kitchen ventilation system, clothes dryer and/or fireplace is installed in the building,
provision must be made for an outside air supply near the gas utilization equipment area. Install
permanently open grilles sized at not less than one square inch free area per 4,000 BTU of burner
input. When ventilating through horizontal ducts, grilles should be sized at not less than one
square inch free area per 2,000 BTU of all gas utilization equipment in the confined space. In any
case, the minimum dimension of rectangular air ducts shall not be less than 3 inches.
■
■
■
■
In Canada, for detailed ventilation requirements, refer to standard CAN/CGA 1-B149.1 or .2
and/or local codes.
■
■
■
■
Clean the gas utilization equipment, heat exchanger interior, combustion chamber, and flue
connections. Remove all adhering tars, scale, dirt and soot. Inspect for actual leaks and/or poten-
tial leaks.
■
■
■
■
Cement all joints, including those in the gas utilization equipment base and around door
frames, to prevent leakage into or out of the combustion chamber.
■
■
■
■
The access or firing door should open easily to relieve pressure. If positive latches exist, they
should be modified to permit easy opening; a spring loaded door holder is recommended.
■
■
■
■
On all boilers, make certain the pressure relief safety valve is in good operating condition.
A combustion chamber liner is normally required to protect non-heat transfer surfaces and to pro-
vide a radiant bed for rapid heat transfer to the primary surfaces of the heat exchanger. In most
cases, an existing oil burner combustion chamber liner can be used, if in good condition.
2