Midco F400-33 User Manual
Page 4
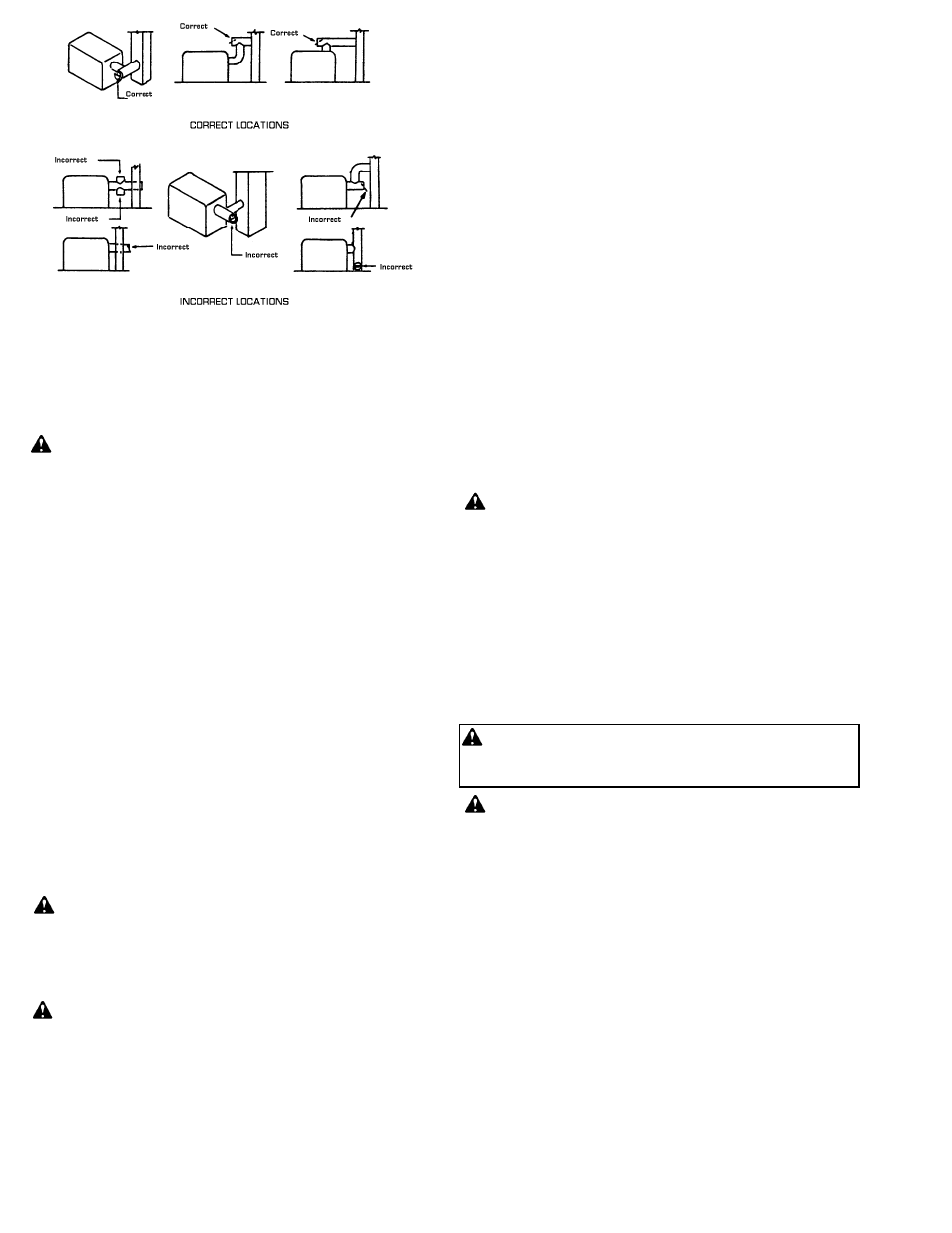
-4-
FIGURE 4 Location for Barometric Draft Regulators
Figure 3 and 4 : Copyright by the American Gas
Association. Used by permission of the copyright holder.
■
Provide a sediment trap, union and 1Ú8" pressure tap in
piping close to burner as shown in Figure 5.
■
Use pipe joint compound approved for use with Liquid
Petroleum Gases.
■
Piping must also comply with your local codes.
■
To obtain the maximum firing rate of 700 MBH, the
NATURAL gas supply piping must be sized to provide a
minimum of 5.0"W.C. pressure (11.0"W.C. PROPANE) to
the inlet of the main safety valve when the burner and all
other gas utilization equipment are on. The pilot regulator
can be mounted in any position, the main regulator
should be mounted upright and in a horizontal run of pipe.
■
If the burner piping must be rearranged because of
space limitation, be sure to carry out the general arrange-
ment shown in Figure 5.
■
Run full size pipe or tubing from regulator vent open-
ings to outside of building. Provide no traps in the vent
lines and terminate away from all doors and windows;
also make provisions for keeping rain and foreign objects
from entering the vent piping.
■
When the burner is installed in the vestibule of jacketed
equipment, it is recommended that the Safety Shut -
Off Valve(s) be left adjacent to the burner within the ves-
tibule and the Main Manual Shut-Off Valve be installed
outside.
■
When high supply gas pressure is encountered, as in
the case in many industrial plants, the gas line size can be
reduced to allow for a greater pressure drop; however, the
size must be sufficient to deliver burner rating pressure.
CAUTION: High gas pressure supply lines require
the proper pressure reducing regulators. Install two
separate high pressure regulators of the Tight Shut-
Off type upstream of the low pressure regulators. One
sized for main gas input, and one suitable for the min-
imum flow regulating capacity of the pilot.
■
The high pressure regulators may be substituted for the
low pressure regulators. If high pressure regulators are
used as substitutes, they must be adjustable down to a
minimum of 2.0"W.C. outlet pressure for the pilot and
5.0"W.C. for the main gas. If they are additions they must
be adjustable down to the maximum burner inlet pressure
rating (14.0"W.C.)
DANGER: Explosion hazard.
Do not use oxygen for pressure testing.
An explosion could occur during initial start up.
CAUTION: Because it is difficult to accurately
control pressure during supply pipe leak testing, it is
recommended that all low pressure (14.0"W.C. max.)
components, both main and pilot, be disconnected
during testing. Exposing low pressure regulators and
valves, including manual valves, to pressures over 1/2
PSIG (14.0"W.C.) will cause damage and void all
warranties.
■
When the gas supply line is about to be put into service
it must be rested to insure that it is gas tight. Use air or
inert gas under pressure and test with soap and water or
other liquids to locate leaks.
■
Before gas is turned into the system, a check must be
made to see that there are no open fittings and to make
sure the burner main and pilot manual valves are closed.
■
After checking above, purge the gas line up to the
burner inlet. Purging the air from the gas supply line at
this step will expedite the first light-off.
V
ELECTRICAL
CAUTION: Refer to separate wiring diagram in-
cluded with each burner.
Installation wiring and grounding to the burner must con-
form to local codes, or, in their absence in the United
States to National Electric Code, ANSI/NFPA No. 70
latest edition; in Canada, to Canadian Electrical Code
Part 1, CSA Standard C22.1
■
Use copper wire not less than 14 gage for line voltage
wiring. Hook up to a dedicated line with an on-off discon-
nect switch and a minimum 10 Amp breaker.
■
The frame of the burner should be well grounded. Nor-
mally the piping and/or electric conduit will provide suffi-
cient grounding. However, a ground lug is located in con-
trol box for positive grounding where insulated pipe
couplings are used or where any doubt exists regarding
grounding sufficiency.
■
Confirm that the polarity is correctÑhot wire to strip ter-
minal L1, neutral L2Ñand that the neutral line is not sub-
ject to induced low voltage (check L2 to earth ground)
from other equipment, as that can cause the electronic
flame safeguard to malfunction.
■
Each installation must include suitable limit control(s).
Existing oil burner combination operating and limit con-
trols are normally NOT SUITABLE for gas burner use.
■
Connect motors used on forced air furnace fans or boil-
er pumps to a combination limit control and switch.
CAUTION: Label all wires prior to disconnection
when servicing controls. Wiring errors can cause im-
proper and dangerous operation. Verify proper opera-
tion after servicing.
VI
PIPING
CAUTION: The available gas pressure should be
within the limits shown in SPECIFICATIONS section.
Excessive pressure may damage electric valves, regu-
lators and manual valves. If the supply pressure ex-
ceeds the 14.0"W.C. maximum, a suitable high pres-
sure regulator must be installed ahead of the Main
Manual Shut-Off Valve shown in Figure 5.
■
The burner gas supply piping should branch off from
the main line as close to the gas meter as possible. Do
not connect to the bottom of a horizontal section. Use new
black pipe and malleable fittings free of cutting and
threading burrs or defects.