Zip 30 - mul – Dake Model Zip 30 User Manual
Page 14
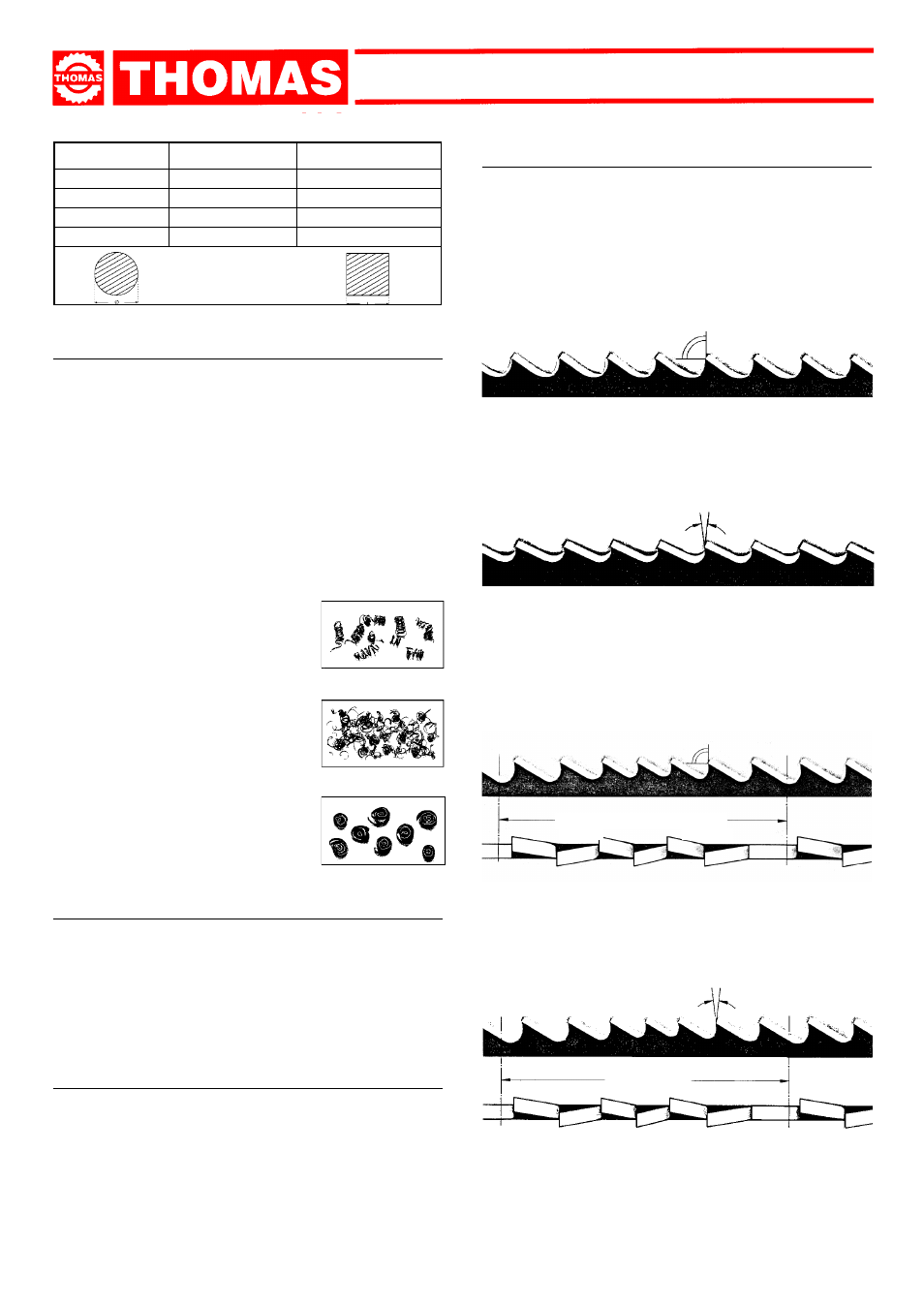
14
ZIP 30 - MUL
ZIP 30 - MUL
ZIP 30 - MUL
ZIP 30 - MUL
ZIP 30 - MULTI MODE
TI MODE
TI MODE
TI MODE
TI MODE
9.7 - Blade type
They differ essentially in their constructive characteristics, such
as:
- shape and cutting angle of tooth
- pitch
- set
Shape and angle of tooth
REGULAR TOOTH: 0° rake and constant pitch.
Most common form for transversal or inclined cutting of solid
small and average cross-sections or pipes, in laminated mild
steel and grey iron or general metal.
POSITIVE RAKE TOOTH: 9° - 10° positive rake and constant
pitch.
positive
Particular use for crosswise or inclined cuts in solid sections or
large pipes, but above all harder materials (highly alloyed and
stainless steels, special bronze and forge pig).
COMBO TOOTH: pitch varies between teeth and consequently
varying teeth size and varying gullet depths. Pitch varies be-
tween teeth which ensures a smoother, quieter cut and longer
blade life owing to the lack of vibration.
SOLID Ø OR L MM
Z CONTINUOUS
TOOTH DESIGN
Z COMBO
TOOTH DESIGN
TILL 30
8
5/8
FROM 30 TO 60
6
4/6
FROM 40 TO 80
4
4/6
MORE THAN 90
3
3/4
Ø = DIAMETER L = WIDTH
9.4 - Cutting and advance speed
The cutting speed (m/min) and the advance speed (cm
2
/min =
area travelled by the disk teeth when removing shavings) are
limited by the development of heat close to the tips of the teeth.
- The cutting speed is subordinate to the resistance of the ma-
terial (R = N/mm
2
), to its hardness (HRC) and to the dimen-
sions of the widest section.
- Too high an advance speed (= lowering of the saw frame)
tends to cause the disk to deviate from the ideal cutting path,
producing non rectilinear cuts on both the vertical and the
horizontal plane.
The best combination of these two parameters can be seen
directly examining the chips.
Long spiral-shaped chips indicate ideal
cutting.
Very fine or pulverized chips indicate lack
of feed and/or cutting pressure.
Thick and/or blue chips indicate overload
of the blade.
9.5 - Blade running-in
When cutting for the first time, it is good practice to run in
the tool making a series of cuts at a low advance speed
(= 30-35 cm
2
/min on material of average dimensions with re-
spect to the cutting capacity and solid section of normal steel
with R = 410-510 N/mm
2
), generously spraying the cutting
area with lubricating coolant.
9.6 - Blade structure
Bi-metal blades are the most commonly used. They consist in a
silicon-steel blade backing with electron beam or laser welded
high speed steel (HHS) cutting edge. The type of stocks are
classified in M2, M42, M51 and differ from each other because
of their major hardness due to the increasing percentage of
Cobalt (Co) and molybdenum (Mo) contained in the metal alloy.
distance between teeth
Another advantage offered in the use of this type of blade in the
fact that with an only blade it is possible to cut a wide range of
different materials in size and type.
COMBO TOOTH: 9° - 10° positive rake.
positive
This type of blade is the most suitable for the cutting of section
bars and large and thick pipes as well as for the cutting of solid
bars at maximum machine capacity. Available pitches: 3-4/4-6.