Sterlco SMC 2-3.5 Portable Chillers User Manual
Page 17
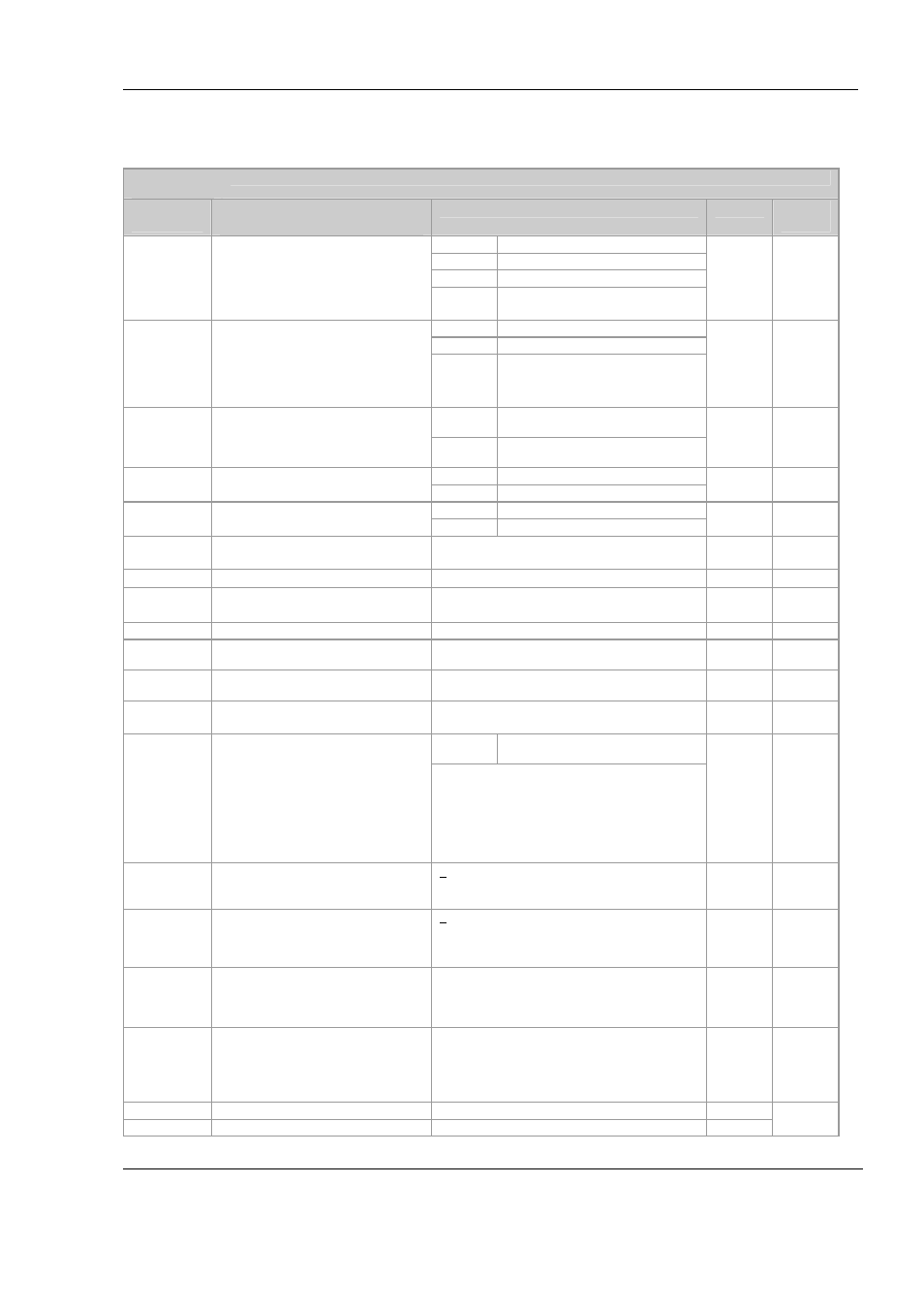
3200 Series
ACS 3216 Operators Manual 17
CONTROL
LIST
‘CTRL’
Parameter
Name
Parameter Description
(Scrolling Display)
Value
Default
Access
Level
Pid
PID
off
Heating off
on.of
On/Off
C T R L . H
HEATING TYPE
Selects the channel 1 control algorithm.
Different algorithms may be selected for
channels 1 and 2. In temperature control
applications, Ch1 is usually the heating
channel, Ch2 is the cooling channel.
MTr
Valve position control
As order
code
Conf
oFF
Cooling disable
pid
PID
C T R L . C
COOLING TYPE
Selects the channel 2 Control algorithm.
Different algorithms may be selected for
channels 1 and 2.
This is not available if the instrument is a
valve position controller
on.of
On/Off
As order
code
Conf
rev
Reverse acting. Output decreases as PV
increases
C T R L . A
CONTROL ACTION
Selects the direction of the control. i.e reverse
or direct acting.
dir
Direct acting. Output increases as PV
decreases
rev
Conf
enG
In engineering units
P B . U N T
PROPORTIONAL BAND UNITS
Perc
In percent
OFF
Autotune off
A T U N E
AUTO-TUNE ENABLE
On
Set to ‘on’ to start auto-tuning
OFF
L3
P B
PROPORTIONAL BAND
0.1 t 9999 display units or
1 to 999.9% if proportional band expressed as %
20
L3
T I
INTEGRAL TIME
Off to 9999 seconds
360 sec
L3
T D
DERIVATIVE TIME
Off to 9999 seconds
TD
defaults to OFF for valve position control
60 sec
L3
R 2 G
RELATIVE COOL GAIN
0.1 to 10.0
1.0
L3
C B H i
CUTBACK HIGH
Auto or 1to 3000 display units
Auto =
3xPb
L3
C B L o
CUTBACK LOW
Auto or 1 to 3000 display units
Auto =
3XPb
L3
M R
MANUAL RESET
0.0 to 100.0% (heat only)
-100.0 to 100.0% (heat/cool)
0.0% L3
Off
Setting loop Break Time to OFF disables
the Loop Break Alarm
L B T
LOOP BREAK TIME
The loop break alarm attempts to detect loss
of restoring action in the control loop by
checking the control output, the process value
and its rate of change.
Loop break detection works for all control
algorithms: PID, VP and ON-OFF.
Note: This is not to be confused with load
failure and partial load failure.
1 to 9999 minutes
OFF
L3
O P . H I
OUTPUT HIGH
Adjust to limit the maximum heating power
applied to the process
+100.0%
100.0% L3
O P . L O
OUTPUT LOW
Adjust to limit the maximum cooling power
applied to the process or to apply a minimum
heating power
+100.0%
0.0 (heat
only)
-100 (cool)
L3
M T R . T
MOTOR TRAVEL TIME
Set this value to the time that it takes for the
motor to travel from its fully closed to its
fully open position.
0.0 to 999.9 seconds
Note: In motorised valve control only the PB and TI
parameters are active. The TD parameter has no effect on
the control.
0.0 L3
D . B A N D
CHANNEL 2 DEAD BAND
Period when no output is demanded from
either channel 1 or channel 2
Adjust, for example, to increase the period
when no heating or cooling power is applied
Off or 0.1 to 100.0% of the cooling proportional band
OFF
L3
H Y S T . H
HEATING HYSTERESIS
-199.9 to 200.0 display units
1
H Y S T . C
COOLING HYSTERESIS
-199.9 to 200.0 display units
1
L3 On/off
only