Dwyer PBV User Manual
Page 3
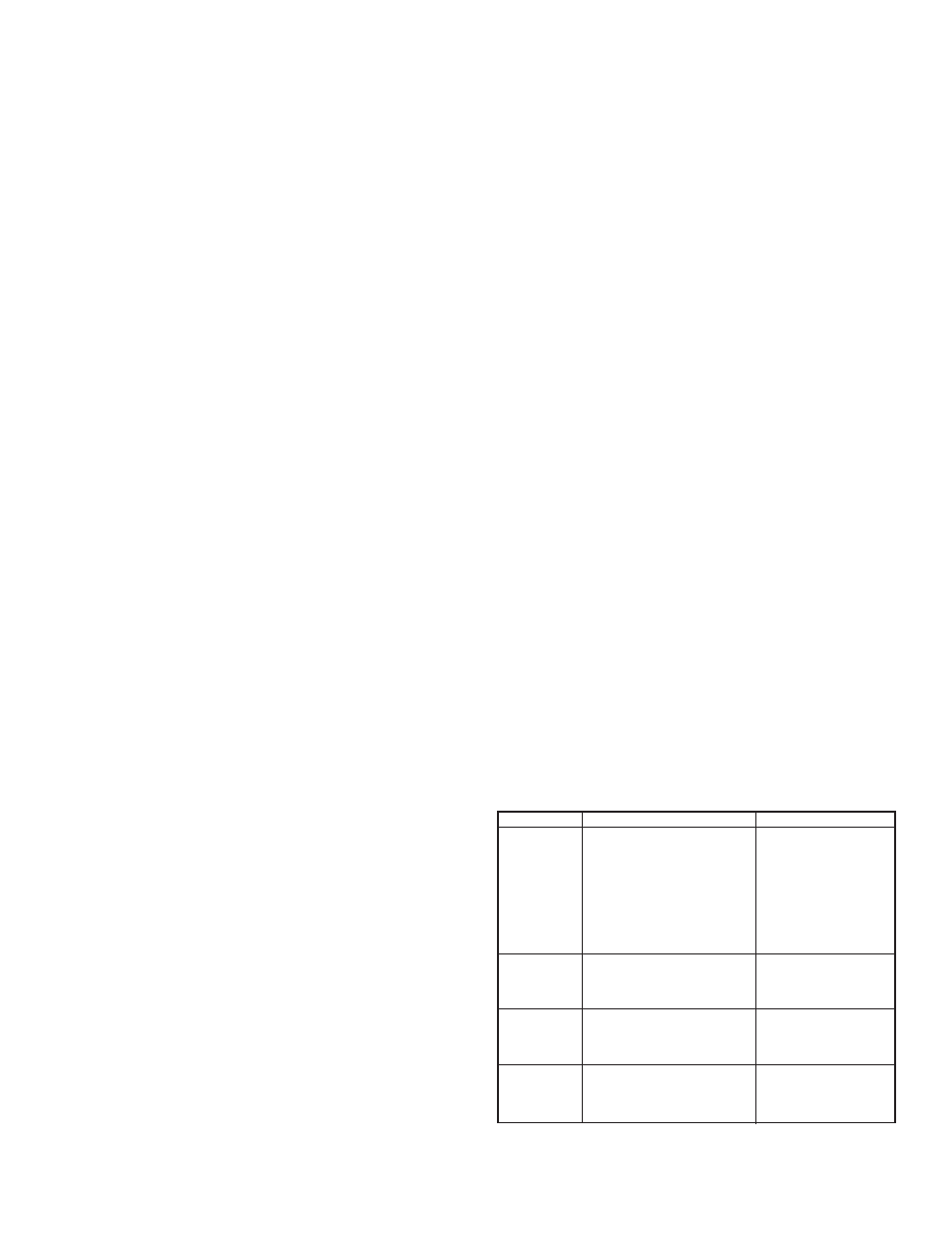
SYMPTOM
Actuator does
not respond to
control signal
Actuator will not
open and/or
close
completely
Valve oscillates
Actuator motor
runs but output
shaft does not
rotate
SOLUTION
• Turn on Power
• Check wiring diagram;
re-wire
• Bring correct supply
to actuator
• Allow motor to cool;
resets automatically
• Remove actuator;
remount after 90° turn
• Set cams per instructions
• Install correct unit
• Remove stops
• Torque of valve too high
• Install brake
• Adjust brake; tighten
screw
• Contact factory
PROBLEM
• Power is not on
• Actuator wired incorrectly
• Incorrect voltage
• Thermal Overload
• Actuator and Valve in opposite
positions when actuator installed
• Travel limit switch set incorrectly
• Valve torque too high
• Mechanical stops not
removed when installing actuator
• Torque of valve too high
• Actuator without brake
installed on butterfly valve
• Motor brake misadjusted
• Gear damaged/sheared pin
ELECTRIC ACTUATOR
I. BASIC INSTALLATION
1. Operate valve manually and place in the open position. (Note: ALL ELECTRIC
ACTUATORS ARE SHIPPED IN THE OPEN POSITION.)
2. Remove any mechanical stops the valve might have. (DO NOT REMOVE ANY
PARTS NECESSARY FOR THE PROPER OPERATION OF THE VALVE,
SUCH AS THE PACKING GLAND, PACKING NUT, ETC.)
3. Ensure that the actuator output shaft and valve stem are aligned properly. If
they are not, operate the valve manually until they are correct.
4. Mount actuator to valve. Do not tighten nuts and bolts at this time.
5. Remove actuator cover.
6. Bring power to the actuator. CAUTION: Make sure power is OFF at the main
box.
7. Wire the actuator per the diagram attached to the inside of the cover. Special
actuators (those with positioner boards, etc.) will have diagrams enclosed
inside the cover.
8. Securely tighten bolts used to mount the actuator to a mounting bracket or
directly to the valve mounting pad if it is ISO5211 compliant.
9. Cycle the unit several times and check the open and closed positions of the
valve. Cams are pre-adjusted at the factory; due to the variety of valve designs
and types, however, slight adjustments might be required. (SEE II and III).
10. Replace cover and tighten screws.
II. TO SET THE OPEN POSITION
1. Cycle the valve to the open position by applying power to terminals #1 and #2.
The top cam and switch control this position. In the open position, the set screw
in the top cam will be accessible.
2. If the valve is not open completely:
A. Slightly loosen the 8-32 x 1/4” set screw on the top cam.
B. Rotate the cam clockwise (CW) by hand until the switch makes contact.
Contact is made when a slight click can be heard. By making incremental
CW movements of the top cam, the valve can be positioned precisely in the
desired position.
C. When the top cam is set, tighten the set screw securely.
3. If the valve opens too far:
A. Apply power to terminals #1 and #3. This will begin to rotate valve CW.
When valve is full open and in the exact position desired, remove power
from actuator.
B. Loosen the set screw in the top cam.
C. Rotate the top cam counterclockwise (CCW) until the switch arm drops off
the round portion of the cam onto the flat section. A slight click can be heard
as the switch changes state.
D. Continue applying power to terminals #1 and #3 until valve is in the desired
position.
III. TO SET THE CLOSED POSITION
1. Apply power to terminals #1 and #3 to move the valve toward the closed
position. The bottom cam and switch control the closed position. In the closed
position, the set screw in the bottom cam will be accessible.
2. If the valve is not closed completely:
A. Slightly loosen the 8-32 x 1/4” set screw on the bottom cam.
B. Rotate the cam counter-clockwise (CCW) by hand until the switch makes
contact. Contact is made when a slight click can be heard. By making
incremental CCW movements of the bottom cam, the valve can be
positioned precisely in the desired position.
C. When the top cam is set, tighten the set screw securely.
3. If the valve closes too far:
A. Apply power to terminals #1 and #2. This will begin to rotate valve CCW.
When valve is fully closed and in the exact position desired, remove power
from actuator.
B. Loosen the set screw in the top cam.
C. Rotate the top cam clockwise (CW) until the switch arm drops off the round
portion of the cam onto the flat section. A slight click can be heard as the
switch is no longer making contact with the round part of the cam.
D. Continue applying power to terminals #1 and #2 until valve is in the desired
position.
XI. TROUBLESHOOTING
IV. MAINTENANCE
Once the actuator has been properly installed, it requires no maintenance. The
gear train has been permanently lubricated and in most cases will never be
disturbed. In the event it becomes necessary to open the gear box for any reason,
however, Shell Darina
®
#2 grease is recommended for re-lubricating.
V. DUTY CYCLE
Most standard electric actuators are rated for 25% duty cycle at 100% ambient
temperature at the rated torque.
VI. THERMAL OVERLOAD
All actuators are equipped with thermal overload protection to guard the motor
against damage due to overheating.
VII. MECHANICAL OVERLOAD
All actuators are designed to withstand stall conditions. It is not recommended to
subject the unit to repeated stall conditions.
VIII. SPARE PARTS
When ordering parts, please specify:
A. Model # B. Serial # C. Part Description
Recommended spare parts include:
A. Standard actuator: set of cams and switches.
B. Actuators w/positioner: set of cams and switches; 1K potentiometer; valve
positioner board.
IX. NEMA 7 ELECTRIC ACTUATORS
In general, operation and maintenance of a NEMA 7 electric actuator is no different
that of a NEMA 4 actuator. However, some precautions must be followed:
1. DO NOT under any circumstances remove the cover of the actuator while in a
hazardous location. Removal of the cover while in a hazardous location could
cause ignition of hazardous atmospheres.
2. DO NOT under any circumstances use a NEMA 7 electric actuator in a
hazardous location that does not meet the specifications for which the actuator
was designed.
3. Always mount and cycle test the actuator on the valve in a non-hazardous
location.
4. When removing the cover, care must be taken not to scratch, scar of deform
the flame path of the cover and base of the actuator, since this will negate the
NEMA rating of the enclosure.
5. When replacing the cover on actuators rated for both NEMA 4 & 7, take care
that the gasket is in place to assure proper clearance after the cover is
secured. After the cover screws are tightened, the clearance between the cover
and the base should be checked. A .002” thick by 1/2” wide feeler gauge is
used for this; it must not enter between the two mating faces more than .125".
6. All electrical connections must be in accordance with the specifications for
which the unit is being used.
7. Should the unit ever require maintenance, remove from the hazardous location
before attempting to work on the unit.
If the actuator is in a critical application, it is advisable to have a standby unit
in stock.
Darina
®
is a registered trademark of Shell Oil Company